A sampling connection is a type of connection in piping that allows for the extraction of a representative sample of a fluid or gas from within a pipeline for the purpose of analysis or testing. Sampling connections can be found in a variety of industries, including oil and gas, chemical processing, pharmaceuticals, and food and beverage production.
Types of Sampling Connections
There are several types of sampling connections that can be used, depending on the specific application and the requirements of the sampling process. Depending on the connection to a piping system, the common types of sampling connections are:
- Flanged sampling connections: These are typically used for high-pressure or high-temperature applications and feature a flange that is bolted onto the pipeline. A valve is then attached to the flange, which can be used to control the flow of fluid or gas through the sampling connection.
- Welded sampling connections: These are welded directly onto the pipeline and are typically used for lower-pressure or lower-temperature applications. They can be designed to include a valve or other components for controlling the flow of fluid or gas.
- Threaded sampling connections: These feature a threaded connection that is screwed onto the pipeline and is typically used for lower-pressure or lower-temperature applications. They can be designed to include a valve or other components for controlling the flow of fluid or gas.
Again they can be classified as follows:
- Retractable sampling connections: These are sampling connections that use a retractable probe or nozzle to take a sample from within the pipeline. Retractable connections are commonly used in applications where the sampling location may change or where the pipeline is not easily accessible.
- Fixed sampling connections: These are sampling connections that use a fixed probe or nozzle to take a sample from within the pipeline. Fixed connections are commonly used in applications where the sampling location is known and where the pipeline is easily accessible.
Sampling connections are important for ensuring the quality and safety of products and processes in a variety of industries. Proper design, installation, and maintenance of sampling connections are critical to ensure accurate and representative sampling. Fig. 1 below shows a typical sampling connection system of an oil and gas industry.
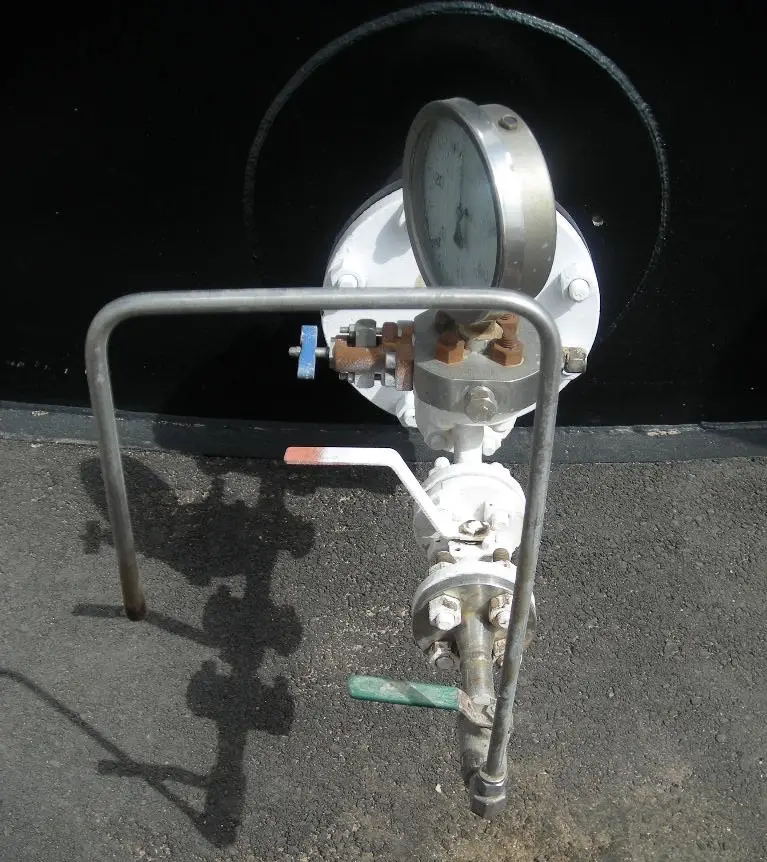
Requirements for a Sampling Connection
The requirements for a sampling connection depend on the specific application and the intended use of the sample. However, in general, sampling connections should meet the following requirements:
- Compatibility: The materials used in the sampling connection should be compatible with the fluid or gas being sampled. This includes considerations such as chemical resistance, temperature and pressure ratings, and potential for contamination.
- Representative sampling: The sampling connection should be designed to ensure that the sample collected is representative of the fluid or gas being sampled. This may require careful selection of the sampling point, as well as the use of appropriate sampling techniques and equipment.
- Cleanliness: The sampling connection should be designed and maintained to minimize the risk of contamination, which can affect the accuracy and reliability of the sample. This may include regular cleaning and sanitization, the use of appropriate sealing materials, and proper handling of the sample.
- Ease of use: The sampling connection should be designed to be easy to use and maintain, including features such as accessible valves, clear labeling, and simple installation and removal.
- Compliance: The sampling connection should comply with relevant industry standards and regulations, including those related to safety, quality control, and environmental protection.
Proper design, installation, and maintenance of sampling connections are critical to ensure accurate and representative sampling and to support the overall quality and safety of products and processes in a variety of industries.
Sampling Connection Components
The components of a sampling connection in the oil and gas industry can vary depending on the specific application and requirements. However, some common components of a sampling connection in the oil and gas industry may include:
- Sampling valve: This is the main component of the sampling connection and allows for the control of fluid or gas flow through the connection. There are various types of sampling valves, including ball valves, needle valves, and plug valves.
- Sampling probe or nozzle: This component is used to extract a representative sample of the fluid or gas from within the pipeline. The sampling probe or nozzle can be designed in a variety of shapes and sizes, depending on the specific application and the requirements of the sampling process.
- Connector or fitting: This component connects the sampling valve to the pipeline and can include flanges, threaded connections, or welded connections.
- Pressure gauge or indicator: This component allows for the monitoring of pressure within the sampling connection, which can help to ensure safe and accurate sampling.
- Drain or purge valve: This component is used to flush out the sampling connection and remove any residual fluid or gas before taking a sample. This helps to ensure that the sample collected is representative and free from contamination.
- Locking mechanism: This component is used to secure the sampling valve in the closed position and prevent accidental or unauthorized sampling.
Proper design, installation, and maintenance of these components is critical to ensure accurate and representative sampling in the oil and gas industry. Additionally, the selection of appropriate materials and components should be based on factors such as fluid composition, temperature, and pressure, as well as industry standards and regulations.
Design Codes and Standards for Sampling Connection
There are several design codes and standards for sampling connections in the oil and gas industry, depending on the specific application and location. Some commonly used codes and standards include:
- ANSI/ASME B31.3: This code covers process piping design for the oil and gas industry and provides guidelines for the selection of materials, fabrication, installation, and testing of sampling connections.
- API 14.1: This standard provides guidelines for the design, installation, operation, and maintenance of sampling systems for liquids and gases in the petroleum industry.
- ISO 3171: This standard provides guidelines for the measurement of petroleum and related products using automatic pipeline sampling systems.
- ASTM D4177: This standard provides guidelines for the automatic sampling of petroleum and petroleum products, including requirements for sampling systems and procedures.
- NACE MR0175/ISO 15156: This standard provides guidelines for the selection of materials for use in environments containing H2S in the oil and gas industry.
- ASME BPVC: This code covers the design, fabrication, and testing of pressure vessels, including sampling connections used in high-pressure applications in the oil and gas industry.
Proper adherence to these design codes and standards is critical to ensure the safety and reliability of sampling connections in the oil and gas industry. It is important to consult with experts and experienced professionals to ensure that the appropriate codes and standards are being followed for a specific application.
Applications of Sampling Connection Systems
Sampling connection systems have many applications in the oil and gas industry, as well as in other industries that require the sampling of fluids or gases. Some major applications of sampling connection systems include:
- Quality control: Sampling connection systems are commonly used to ensure the quality and consistency of raw materials, intermediates, and final products in the oil and gas industry. Samples can be taken at various stages of the production process to monitor and control product quality.
- Process monitoring and optimization: Sampling connection systems can be used to monitor and optimize process parameters, such as temperature, pressure, and flow rate, in the oil and gas industry. By taking regular samples, operators can identify potential issues and make adjustments to improve process efficiency.
- Environmental monitoring: Sampling connection systems can be used to monitor and sample air, water, and soil in the oil and gas industry, as well as in other industries that generate pollutants or hazardous waste. This can help to ensure compliance with environmental regulations and protect public health and safety.
- Research and development: Sampling connection systems are also used in research and development applications, such as testing new materials, investigating chemical reactions, and developing new products in the oil and gas industry.
- Safety monitoring: Sampling connection systems can be used to monitor safety conditions, such as the presence of toxic or explosive gases, in the oil and gas industry. This can help to prevent accidents and ensure the safety of workers and the environment.
Overall, sampling connection systems play a critical role in ensuring the safety, quality, and efficiency of processes in a wide range of industries, including the oil and gas industry.