Positive displacement pumps are a vital component in various industries, including manufacturing, agriculture, oil and gas, and many others. They play a crucial role in moving fluids from one place to another, whether it’s transferring water in a municipal water supply system, pumping crude oil in an oil refinery, or dosing chemicals in a chemical processing plant. In this comprehensive guide, we will delve deep into the world of positive displacement pumps, covering everything from their basic principles to their applications, types, advantages, disadvantages, and maintenance.
1. Introduction to Positive Displacement Pumps
1.1 Definition and Basic Function
A positive displacement pump is a mechanical device designed to transfer fluids by trapping a fixed amount of fluid and then forcing it into a discharge pipe or outlet. Unlike dynamic pumps, which rely on kinetic energy to move fluids, positive displacement pumps work by creating a sealed chamber that enlarges and contracts to move the fluid. This mechanism allows them to provide a constant flow rate regardless of the discharge pressure or system resistance.
Positive displacement pumps are employed in a wide range of applications, from small-scale domestic use, such as in household water wells, to large-scale industrial processes, like pumping crude oil in a refinery. Their ability to handle various fluids, including viscous and abrasive substances, makes them indispensable in many industries.
1.2 Importance in Various Industries
Positive displacement pumps are integral to several industries due to their reliability, versatility, and precise control over flow rates. Here are some industries where they play a crucial role:
a. Oil and Gas Industry
Positive displacement pumps are extensively used in the oil and gas sector for tasks like transferring crude oil, injecting chemicals into wells for enhanced oil recovery, and transporting natural gas.
b. Chemical Manufacturing
In chemical plants, these pumps are employed to move a wide range of chemicals, including corrosive and viscous substances, for mixing, blending, and processing.
c. Food and Beverage
Positive displacement pumps are vital for food processing, where they handle ingredients, transfer products, and control precise dosing for recipes.
d. Pharmaceutical Industry
In pharmaceutical manufacturing, these pumps are used to handle delicate and sensitive fluids, ensuring accurate dosing and product quality.
e. Water Treatment
Municipal water treatment facilities use positive displacement pumps for processes like dosing chemicals, boosting water pressure, and handling wastewater.
Now that we’ve established the importance of positive displacement pumps in various industries, let’s dive deeper into how they operate.
2. Operating Principles of Positive Displacement Pumps
2.1 Positive Displacement vs. Dynamic Pumps
To understand how positive displacement pumps work, it’s essential to distinguish them from dynamic pumps, also known as centrifugal pumps. Dynamic pumps operate on the principle of imparting kinetic energy to the fluid, which then converts into pressure energy as the fluid moves through the pump. They are more suitable for high-flow, low-pressure applications, where a consistent flow rate is not a primary concern.
Positive displacement pumps, on the other hand, trap a fixed volume of fluid and displace it into the discharge pipe. This action ensures a constant flow rate, making them ideal for applications that require precise control over flow rates, handle viscous fluids, or require high-pressure delivery.
2.2 Fluid Flow Mechanism
Positive displacement pumps work on the fundamental principle of creating a sealed chamber within the pump housing that expands to draw in fluid and contracts to expel it. This mechanism occurs in a cyclic fashion, resulting in a continuous flow of fluid.
The essential components of a positive displacement pump include:
- Casing: The outer structure that encloses the internal components of the pump.
- Inlet: The point where the fluid enters the pump.
- Outlet: The point where the fluid exits the pump.
- Suction Valve: Prevents fluid from flowing back into the inlet during the contraction phase.
- Discharge Valve: Prevents fluid from flowing back into the pump chamber during the expansion phase.
- Rotor or Piston: The moving part of the pump is responsible for creating the varying chamber volume.
The fluid flow mechanism can be divided into two main types: reciprocating and rotary motion.
2.3 Pumping Action
Reciprocating Pumps
Reciprocating positive displacement pumps use a back-and-forth (reciprocating) motion to change the volume of the pump chamber. There are two primary types of reciprocating pumps:
a. Piston Pumps
Piston pumps employ a piston that moves within a cylinder. As the piston moves away from the inlet, it creates a vacuum, drawing fluid into the chamber. When it moves back towards the inlet, the fluid is expelled through the outlet.
Piston pumps are known for their high-pressure capabilities and precise flow control. They are often used in applications where accuracy and pressure are critical, such as in hydraulic systems.
b. Diaphragm Pumps
Diaphragm pumps use a flexible diaphragm to separate the fluid from the pump’s mechanical components. The diaphragm flexes back and forth, creating a pumping action that draws fluid into and expels it from the chamber.
Diaphragm pumps are favored in applications where maintaining fluid purity and preventing contamination are essential, as the diaphragm acts as a barrier between the fluid and the pump internals.
Rotary Pumps
Rotary positive displacement pumps use a rotating mechanism to change the volume of the pump chamber continuously. There are several types of rotary pumps, each with its unique design and advantages:
a. Gear Pumps
Gear pumps consist of two interlocking gears—one driven by a motor and the other idler gear. As the gears rotate, they create voids that draw in fluid at the inlet and expel it at the outlet.
Gear pumps are known for their simplicity and durability. They are commonly used for applications involving low to medium-viscosity fluids.
b. Vane Pumps
Vane pumps use a rotor with vanes that slide in and out of slots within the pump housing. As the rotor rotates, the vanes create expanding and contracting chambers that move the fluid.
Vane pumps offer a good balance between flow rate and pressure capabilities. They are often used in hydraulic systems and automotive applications.
c. Screw Pumps
Screw pumps feature one or more screws or helical rotors that rotate to draw in and expel fluid. The screw’s design varies, with options like single-screw, twin-screw, or triple-screw pumps.
Screw pumps are suitable for high-flow, high-pressure applications, including oil and gas transfer and industrial processes.
Peristaltic Pumps
Peristaltic pumps use a flexible tube or hose and a rotating roller mechanism to squeeze the tube at various points along its length. This squeezing action propels the fluid through the tube in a pulsating manner.
Peristaltic pumps are excellent for applications where fluid contamination is a concern, as the fluid only comes into contact with the interior of the tube. They are often used in medical devices and laboratory equipment.
3. Types of Positive Displacement Pumps
Positive displacement pumps come in various types, each suited to specific applications based on factors like flow rate, pressure, and the nature of the fluid being pumped. Let’s explore these types in more detail.
3.1 Reciprocating Pumps
Reciprocating pumps are characterized by their back-and-forth (reciprocating) motion, which creates varying chamber volumes to move fluid. Two common types of reciprocating pumps are piston pumps and diaphragm pumps.
a. Piston Pumps
Structure and Operation:
- Piston pumps consist of a piston that moves within a cylinder.
- The piston is connected to a crankshaft, which converts rotary motion from a motor into reciprocating motion.
- As the piston moves away from the inlet, it creates a vacuum, drawing fluid into the chamber.
- When the piston moves back towards the inlet, the fluid is expelled through the outlet.
Applications:
- Hydraulic systems
- High-pressure applications
- Fluid dosing and metering
b. Diaphragm Pumps
Structure and Operation:
- Diaphragm pumps use a flexible diaphragm to separate the fluid from the pump’s mechanical components.
- The diaphragm flexes back and forth, creating a pumping action that draws fluid into and expels it from the chamber.
- Some diaphragm pumps use a hydraulic mechanism to drive the diaphragm, while others rely on mechanical linkages.
Applications:
- Chemical processing
- Pharmaceuticals
- Food and beverage
- Water treatment
3.2 Rotary Pumps
Rotary pumps use a rotating mechanism to continuously change the volume of the pump chamber. Several types of rotary pumps are commonly used in various industries.
a. Gear Pumps
Structure and Operation:
- Gear pumps consist of two interlocking gears—one driven by a motor and the other an idler gear.
- As the gears rotate, they create voids that draw in fluid at the inlet and expel it at the outlet.
- The gears can be either external or internal, depending on the pump’s design.
Applications:
- Lubrication systems
- Fuel transfer
- Chemical transfer
b. Vane Pumps
Structure and Operation:
- Vane pumps use a rotor with vanes that slide in and out of slots within the pump housing.
- As the rotor rotates, the vanes create expanding and contracting chambers that move the fluid.
- Vane pumps can be designed with various numbers of vanes, affecting flow rate and pressure capabilities.
Applications:
- Hydraulic systems
- Automotive applications
- Refrigeration
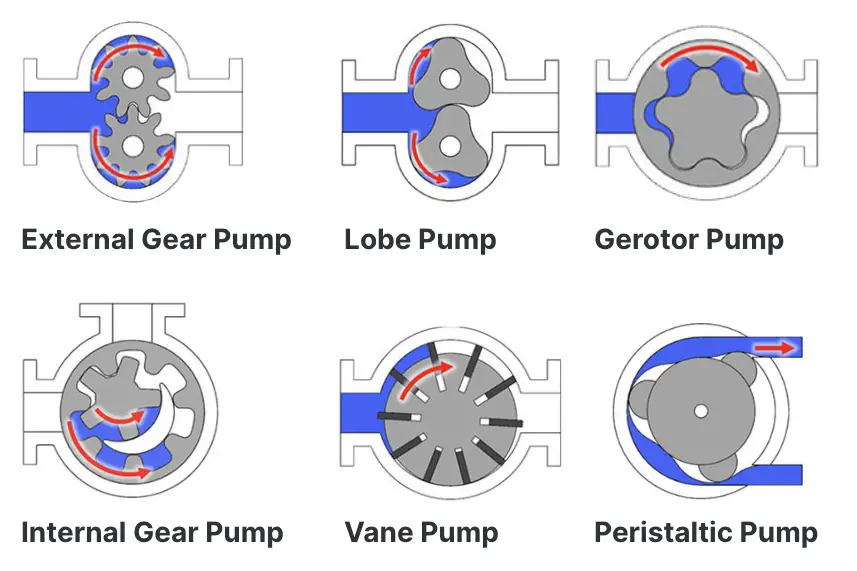
c. Screw Pumps
Structure and Operation:
- Screw pumps feature one or more screws or helical rotors that rotate to draw in and expel fluid.
- The screw’s design can vary, with options like single-screw, twin-screw, or triple-screw pumps.
- The intermeshing screws create chambers that move the fluid as they rotate.
Applications:
- Oil and gas transfer
- Industrial processes
- Marine applications
3.3 Peristaltic Pumps
Peristaltic pumps use a unique mechanism that involves a flexible tube or hose and a rotating roller mechanism to squeeze the tube at various points along its length. This squeezing action propels the fluid through the tube in a pulsating manner.
Structure and Operation:
- Peristaltic pumps consist of a flexible tube or hose that carries the fluid.
- A rotating roller mechanism, often driven by a motor, squeezes the tube at multiple points along its length.
- This squeezing action creates a positive displacement effect, moving the fluid through the tube.
Applications:
- Medical devices
- Laboratory equipment
- Chemical dosing
- Food and beverage processing
Each type of positive displacement pump has its unique advantages and limitations, making it essential to select the right pump for a specific application.
4. Applications of Positive Displacement Pumps
Positive displacement pumps find applications in a wide range of industries due to their versatility and ability to handle various fluids. Let’s explore some common applications in more detail.
4.1 Industrial Applications
a. Oil and Gas Industry
Positive displacement pumps are used for:
- Transferring crude oil from wells to processing facilities
- Injecting chemicals into wells for enhanced oil recovery
- Transporting natural gas in pipelines
- Pumping drilling mud for oil well drilling
b. Chemical Manufacturing
These pumps handle:
- Transfer and mixing of chemicals
- Precise dosing of chemicals for industrial processes
- Handling corrosive and abrasive chemicals
c. Food and Beverage
Positive displacement pumps are employed in:
- Food processing for transferring ingredients
- Filling and packaging of beverages and sauces
- Accurate dosing of flavorings and additives
d. Pharmaceutical Industry
They are used for:
- Handling sensitive pharmaceutical compounds
- Precise dosing for drug formulation
- Maintaining product purity and quality
e. Water Treatment
In municipal and industrial water treatment facilities, positive displacement pumps are essential for:
- Chemical dosing for water purification
- Pumping and transferring wastewater
- Maintaining consistent water pressure in distribution systems
4.2 Domestic and Municipal Applications
a. Residential Water Supply
Positive displacement pumps can be found in private wells and water supply systems to:
- Pump water from underground wells to storage tanks
- Provide consistent water pressure for households
b. Firefighting
Fire engines use positive displacement pumps to:
- Deliver high-pressure water or foam for firefighting efforts
- Maintain a continuous flow of water during firefighting operations
c. Sewage and Wastewater
In sewage systems, these pumps are used for:
- Pumping raw sewage to treatment plants
- Handling sludge and wastewater in treatment facilities
5. Advantages of Positive Displacement Pumps
Positive displacement pumps offer several advantages that make them suitable for specific applications:
5.1 Precise Flow Control
One of the primary advantages of positive displacement pumps is their ability to provide precise control over flow rates. The fixed displacement per cycle ensures consistent and accurate delivery of fluids, making them ideal for applications where dosing and metering are critical.
5.2 Handling Viscous and Abrasive Fluids
Positive displacement pumps excel at handling viscous and abrasive fluids that would challenge dynamic pumps. Their robust design and ability to create a sealed chamber make them suitable for applications involving chemicals, slurries, and high-viscosity substances.
5.3 Self-Priming Capability
Many positive displacement pumps, particularly diaphragm and rotary pumps, have self-priming capabilities. This means they can draw fluid into the pump even when the pump is not initially filled with liquid. This feature is valuable in applications where maintaining a primed pump is challenging.
5.4 High Pressure Applications
Certain positive displacement pump types, such as piston and screw pumps, are well-suited for high-pressure applications. They can deliver fluids at the required pressure levels consistently, making them essential in industries like oil and gas and hydraulic systems.
6. Disadvantages and Limitations of Positive Displacement Pumps
While positive displacement pumps offer numerous advantages, they also come with certain disadvantages and limitations:
6.1 Efficiency and Energy Consumption
Positive displacement pumps can be less energy-efficient than dynamic (centrifugal) pumps, especially at high flow rates. The constant displacement per cycle can lead to inefficiencies when the system requires variable flow rates. Energy consumption may be higher, resulting in increased operating costs.
6.2 Wear and Maintenance
The mechanical components of positive displacement pumps are subject to wear and tear due to continuous movement and friction. This wear can result in reduced efficiency and require frequent maintenance or replacement of parts like seals, valves, and diaphragms.
6.3 Limited Flow Range
Positive displacement pumps have a relatively limited flow range compared to dynamic pumps. They may not be the best choice for applications that require very high flow rates with low-pressure differentials.
6.4 Risk of Overpressurization
In some cases, if a positive displacement pump is operated against a closed valve or blockage in the discharge line, it can build up excessive pressure, potentially damaging the pump and the system. Pressure relief valves or safeguards must be in place to prevent overpressurization.
7. Maintenance and Troubleshooting
Maintaining positive displacement pumps is essential to ensure their reliability and longevity. Here are some maintenance tips and common problems associated with these pumps:
7.1 Routine Maintenance
- Lubrication: Ensure that moving parts are adequately lubricated to reduce friction and wear.
- Seal Inspection: Regularly inspect and replace seals, gaskets, and diaphragms as needed to prevent leaks and maintain system integrity.
- Valve Maintenance: Check and maintain suction and discharge valves to ensure proper operation and prevent backflow.
- Cleaning: Clean pump components, including chambers and rotors, to prevent the buildup of debris or residue that can impede performance.
- Alignment: Maintain proper alignment of the pump with the drive mechanism (e.g., motor or engine) to prevent excessive wear.
7.2 Common Problems and Solutions
a. Leakage: Leaking can occur due to damaged seals, gaskets, or diaphragms. Identify and replace the damaged components.
b. Reduced Flow: Reduced flow can result from wear on the pump’s internal components or blockages in the suction or discharge lines. Inspect and clean the pump, and check for blockages in the lines.
c. Noisy Operation: Unusual noise can indicate issues with misalignment, worn bearings, or damaged components. Inspect and repair as necessary.
d. Overheating: Overheating may be caused by excessive friction or insufficient lubrication. Address the root cause and ensure proper lubrication.
e. Cavitation: Cavitation occurs when the pump’s suction pressure drops too low, leading to the formation of vapor bubbles and subsequent damage. Prevent cavitation by maintaining adequate inlet pressure.
8. Safety Considerations
Safety is paramount when working with positive displacement pumps, especially in industrial settings where they are used for handling hazardous substances. Here are some key safety considerations:
8.1 Pump Safety
a. Pressure Relief Valves: Install pressure relief valves to prevent overpressurization and protect the pump and system components.
b. Lockout/Tagout: Implement lockout/tagout procedures when performing maintenance or repairs to prevent accidental start-ups.
c. Proper Ventilation: Ensure proper ventilation in areas where pumps are used to prevent the buildup of fumes or gases.
8.2 Fluid Handling Safety
a. Chemical Compatibility: Verify that the pump materials and components are compatible with the fluids being pumped to prevent chemical reactions or corrosion.
b. Personal Protective Equipment (PPE): Provide appropriate PPE, such as gloves, eye protection, and respiratory protection, when handling hazardous fluids.
c. Emergency Procedures: Establish emergency response protocols in case of leaks, spills, or accidents involving the pumped fluid.
9. Conclusion
Positive displacement pumps are integral to various industries, offering precise flow control, versatility in handling fluids, and reliability in various applications. Understanding their operating principles, types, advantages, disadvantages, and maintenance requirements is essential for ensuring their efficient and safe operation. Whether in the oil and gas sector, chemical manufacturing, food processing, or municipal water treatment, positive displacement pumps continue to play a crucial role in enabling essential processes and services worldwide.