Plastic welding is a process of joining two pieces of plastic together by heating the surfaces to be joined and applying pressure to fuse them together. The process is similar to traditional welding, but instead of using heat to melt and join metal pieces, it uses heat to melt and join plastic parts.
Plastic welding is used in a variety of industries, including automotive, aerospace, medical, and consumer goods. It is a popular choice for joining plastic parts because it produces strong and durable bonds, and it is a cost-effective alternative to other joining methods.
Benefits of Plastic Welding
Plastic welding offers several benefits over other methods of joining plastic parts, including:
- Strong and Durable Bonds: Plastic welding creates strong and durable bonds between plastic parts, ensuring that they stay securely joined even under heavy stress.
- Cost-Effective: Plastic welding is a cost-effective method of joining plastic parts compared to other methods like adhesive bonding or mechanical fastening.
- Versatile: Plastic welding can be used to join a wide range of plastics, including thermoplastics, composites, and engineered plastics.
- Consistent Results: Plastic welding can be automated, which ensures that the process is consistent and produces high-quality results every time.
- No Surface Damage: Unlike other methods like drilling or punching, plastic welding does not damage the surface of the plastic parts, resulting in a clean and aesthetically pleasing finish.
- Environmentally Friendly: Plastic welding produces little to no waste, making it an environmentally friendly method of joining plastic parts.
Applications of Plastic Welded Parts
Plastic welded parts have a wide range of applications across various industries. Some of the common applications of plastic welded parts include:
- Automotive: Plastic welding is used to manufacture various components of automobiles such as fuel tanks, bumpers, dashboard components, and door panels.
- Aerospace: In aerospace, plastic welding is used to manufacture components of aircraft such as cockpit windows, fuel tanks, and ducts.
- Medical: Plastic welding is used in the medical industry to manufacture medical devices, such as tubing, blood bags, and IV bags.
- Consumer goods: Plastic welding is used to manufacture a wide range of consumer goods, such as water bottles, toys, and electronics.
- Construction: In the construction industry, plastic welding is used to manufacture pipes, tanks, and containers.
- Packaging: Plastic welding is used to manufacture various types of packaging, such as bags, pouches, and containers.
- Marine: Plastic welding is used to manufacture components of boats and ships, such as fuel tanks, buoys, and dock fenders.
Overall, plastic welding is a versatile process that can be used to manufacture a wide range of products, making it a popular choice across many different industries.
Types of Plastic Welding
There are several types of plastic welding methods, and the most commonly used methods include:
Hot Plate Welding:
Hot plate plastic welding is a process of joining plastic parts by heating them with a hot plate until they reach their melting point and then pressing them together to create a bond. The hot plate is a heating element that is typically made of aluminum or copper and is heated to a specific temperature based on the type of plastic being welded.
Advantages of Hot Plate Plastic Welding:
- Strong and durable welds: Hot plate plastic welding can produce high-strength welds that are resistant to stress, vibration, and other environmental factors.
- Suitable for a wide range of plastics: Hot plate plastic welding can be used with a wide range of plastic materials, including polyethylene, polypropylene, PVC, and more.
- Versatile process: Hot plate plastic welding can be used to weld large or irregularly shaped parts, as well as to weld multiple layers or thick sections of plastic.
- Precise control: Hot plate plastic welding allows for precise temperature control, which can ensure uniform and consistent welds.
Disadvantages of Hot Plate Plastic Welding:
- Slow process: Hot plate plastic welding can be a slow process, particularly for large parts or thick sections of plastic.
- Requires special equipment: Hot plate plastic welding requires specialized equipment, including a hot plate and a clamping system, which can be expensive.
- Surface preparation: The plastic surfaces being welded need to be clean and smooth, as any contaminants or irregularities can affect the quality of the weld.
- Joint design: The design of the plastic parts being welded needs to be considered carefully, as certain joint designs may not be suitable for hot plate plastic welding.
Overall, hot plate plastic welding is a versatile and efficient method for joining plastic parts, particularly when strong and durable welds are required. However, it may not be suitable for all applications, and careful consideration needs to be given to joint design, surface preparation, and equipment requirements.
Ultrasonic Welding:
Ultrasonic plastic welding is a method of joining plastic parts using high-frequency ultrasonic vibrations to create heat and melt the plastic surfaces. The process involves applying pressure to the plastic parts, while ultrasonic vibrations are directed through a horn to create friction between the surfaces. The friction generates heat, which melts the plastic, and then, upon cooling, fuses the parts together. This method is commonly used in industries such as automotive, medical devices, packaging, and electronics, as it can provide strong and precise welds, with no additional materials needed.
Advantages of Ultrasonic Plastic Welding:
- Strong and durable welds: Ultrasonic plastic welding can create high-strength welds that are resistant to stress, vibration, and other environmental factors.
- Fast process: Ultrasonic plastic welding is a fast process that can produce welds in seconds, which makes it suitable for high-volume production.
- No additional materials needed: Unlike other welding methods, ultrasonic plastic welding does not require additional adhesives, screws, or fasteners, which can save costs.
- Precise control: Ultrasonic plastic welding allows for precise control over the welding process, enabling uniform welds and reducing the risk of damage to plastic parts.
- Environmentally friendly: Ultrasonic plastic welding does not produce any harmful emissions or waste, making it an environmentally friendly process.
Disadvantages of Ultrasonic Plastic Welding:
- Limited to certain types of plastics: Ultrasonic plastic welding is limited to certain types of plastics, such as thermoplastics, which can be melted by high-frequency vibrations.
- Initial setup costs: Ultrasonic plastic welding equipment can be expensive, and may not be practical for small-scale or low-volume production.
- Surface preparation: The plastic surfaces being welded need to be clean and smooth, as any contaminants or irregularities can affect the quality of the weld.
- Joint design: The design of the plastic parts being welded needs to be considered carefully, as certain joint designs may not be suitable for ultrasonic plastic welding.
Overall, ultrasonic plastic welding is a versatile and efficient method for joining plastic parts, particularly for high-volume production, provided the plastic type and joint design are suitable.
Radio Frequency (RF) Welding:
Radio Frequency (RF) plastic welding, also known as high frequency (HF) plastic welding, is a process of joining plastic parts by exposing them to high-frequency electromagnetic waves. In this process, the plastic parts are placed between two electrodes, which generate an oscillating electromagnetic field that causes the plastic to heat up and melt, forming a bond between the parts.
RF plastic welding is typically used for joining thin or small plastic parts, such as PVC or PETG packaging materials. The process is fast and efficient and can produce high-strength welds without the need for additional adhesives or fasteners. RF plastic welding is commonly used in the medical, packaging, and automotive industries, among others.
Advantages of RF Plastic Welding:
- Fast process: RF plastic welding is a fast process, and can join plastic parts in a matter of seconds.
- Strong and durable welds: RF plastic welding can produce high-strength welds that are resistant to stress, vibration, and other environmental factors.
- No additional materials needed: RF plastic welding does not require additional adhesives, screws, or fasteners, which can save costs and reduce the risk of contamination.
- Versatile process: RF plastic welding can be used to weld a wide range of plastic materials, including PVC, PETG, polyethylene, and more.
- Minimal heat affected zone: RF plastic welding produces minimal heat, which reduces the risk of thermal damage to the plastic parts.
Disadvantages of RF Plastic Welding:
- Limited to certain types of plastics: RF plastic welding is limited to certain types of plastics, such as those that contain polar molecules, which are able to absorb electromagnetic energy and heat up.
- Limited to thin or small parts: RF plastic welding is typically used for thin or small plastic parts, and may not be suitable for larger or thicker parts.
- Equipment requirements: RF plastic welding requires specialized equipment, including an RF generator, which can be expensive.
- Joint design: The design of the plastic parts being welded needs to be considered carefully, as certain joint designs may not be suitable for RF plastic welding.
RF plastic welding is a fast and efficient method for joining plastic parts, particularly for thin or small parts that require high-strength welds. However, it may not be suitable for all applications, and careful consideration needs to be given to joint design, plastic material selection, and equipment requirements.
Spin Welding:
Spin welding is a process used to join two plastic parts together by spinning one part against the other, generating heat and pressure to form a weld between the two parts. In this process, one plastic part is held stationary while the other is rotated at high speed, causing the two parts to rub together and generate frictional heat. As the plastic heats up and softens, the two parts are pressed together, forming a weld between them.
Spin welding is commonly used for joining thermoplastic parts, particularly for parts that have a circular or cylindrical shape, such as tubing or bottles. The process is fast and efficient and can produce strong and durable welds.
Advantages of Spin Welding:
- Fast process: Spin welding is a fast process, and can join plastic parts in a matter of seconds.
- Strong and durable welds: Spin welding can produce high-strength welds that are resistant to stress, vibration, and other environmental factors.
- Minimal heat affected zone: Spin welding produces minimal heat, which reduces the risk of thermal damage to the plastic parts.
- No additional materials needed: Spin welding does not require additional adhesives, screws, or fasteners, which can save costs and reduce the risk of contamination.
- Versatile process: Spin welding can be used to weld a wide range of plastic materials, including polyethylene, polypropylene, PVC, and more.
Disadvantages of Spin Welding:
- Limited to certain types of parts: Spin welding is typically used for circular or cylindrical parts, and may not be suitable for parts with more complex shapes.
- Equipment requirements: Spin welding requires specialized equipment, including a spin welder, which can be expensive.
- Joint design: The design of the plastic parts being welded needs to be considered carefully, as certain joint designs may not be suitable for spin welding.
Spin welding is a fast and efficient method for joining plastic parts, particularly for circular or cylindrical parts that require high-strength welds. However, it may not be suitable for all applications, and careful consideration needs to be given to joint design, plastic material selection, and equipment requirements.
Laser Welding:
Laser plastic welding is a process that uses a high-powered laser beam to melt and join two plastic parts together. In this process, the laser beam is directed onto the joint area of the plastic parts, which causes the plastic to melt and form a bond. The laser is typically delivered through an optic fiber, which allows for precise control of the laser beam. Refer to Fig. 1 (Image Credit: https://www.rapiddirect.com/)
Advantages of Laser Plastic Welding:
- Strong and precise welds: Laser plastic welding can produce high-strength welds that are precise and uniform, even on small or intricate parts.
- Minimal heat affected zone: Laser plastic welding produces minimal heat, which reduces the risk of thermal damage to the plastic parts.
- No additional materials needed: Laser plastic welding does not require additional adhesives, screws, or fasteners, which can save costs and reduce the risk of contamination.
- Fast process: Laser plastic welding can be a fast process, particularly for small or simple parts.
- No tool wear: Laser plastic welding does not use any mechanical tools, which means that there is no tool wear and no need for tool maintenance.
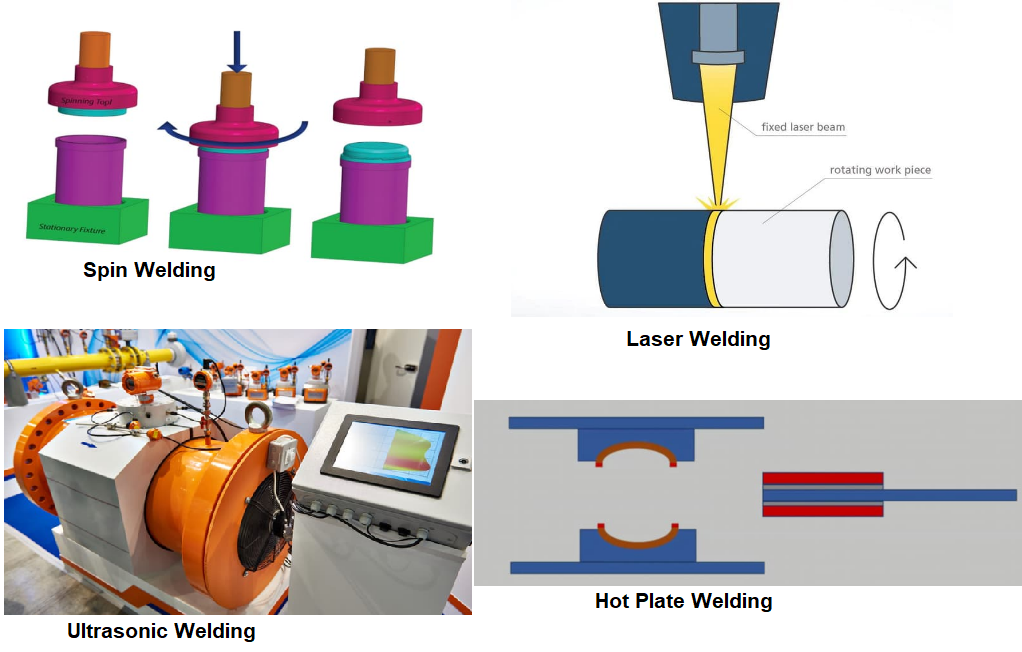
Disadvantages of Laser Plastic Welding:
- Limited to certain types of plastics: Laser plastic welding is limited to certain types of plastics, such as transparent or translucent plastics, which allow the laser beam to pass through and melt the plastic.
- High initial setup costs: Laser plastic welding equipment can be expensive, which may not be practical for small-scale or low-volume production.
- Surface preparation: The plastic surfaces being welded need to be clean and smooth, as any contaminants or irregularities can affect the quality of the weld.
- Joint design: The design of the plastic parts being welded needs to be considered carefully, as certain joint designs may not be suitable for laser plastic welding.
Laser plastic welding is a precise and efficient method for joining plastic parts, particularly for small or intricate parts that require high-strength and precise welds. However, it may not be suitable for all applications, and careful consideration needs to be given to joint design, surface preparation, and equipment requirements.
Friction Plastic Welding:
Friction welding is a plastic welding process that uses frictional heat to melt and join two plastic parts together. In this process, one plastic part is held stationary while the other is rotated at high speed. The two parts are then brought together, and the frictional heat generated by the rotation of the second part melts the plastic at the joint interface, creating a molten pool. When the rotation is stopped, the plastic solidifies, forming a strong, permanent bond between the two parts.
Friction welding is commonly used for joining thermoplastic parts, particularly those with irregular shapes, such as automotive components, household appliances, and medical devices. There are two types of friction welding; Continuous Induce Friction Welding, and Inertia friction welding.
Advantages of Friction Welding:
- Fast and efficient process: Friction welding is a fast process that can join plastic parts in a matter of seconds, making it a highly efficient method of assembly.
- High-strength welds: Friction welding produces high-strength welds that are resistant to stress, vibration, and other environmental factors.
- Minimal heat affected zone: Friction welding produces minimal heat, which reduces the risk of thermal damage to the plastic parts.
- No additional materials needed: Friction welding does not require additional adhesives, screws, or fasteners, which can save costs and reduce the risk of contamination.
- Versatile process: Friction welding can be used to weld a wide range of plastic materials, including polyethylene, polypropylene, PVC, and more.
Disadvantages of Friction Welding:
- Limited to certain types of parts: Friction welding may not be suitable for all types of plastic parts, particularly those that are highly sensitive to heat or have complex shapes.
- Equipment requirements: Friction welding requires specialized equipment, including a friction welder, which can be expensive.
- Joint design: The design of the plastic parts being welded needs to be considered carefully, as certain joint designs may not be suitable for friction welding.
Friction welding is a fast and efficient method for joining plastic parts, particularly for irregularly shaped parts that require high-strength welds. However, it may not be suitable for all applications, and careful consideration needs to be given to joint design, plastic material selection, and equipment requirements.
Vibration Plastic Welding:
Vibration welding is a plastic welding process that uses mechanical vibrations to generate heat and join two plastic parts together. In this process, the two plastic parts to be joined are held together under pressure, and one part is vibrated at a high frequency against the other. The frictional heat generated by the vibration melts the plastic at the joint interface, creating a molten pool. When the vibration is stopped, the plastic solidifies, forming a strong, permanent bond between the two parts. Vibration welding is of two types; Linear Vibration Welding, and Orbital Vibration Welding.
Vibration welding is commonly used for joining thermoplastic parts, particularly those with complex shapes, such as automotive components, electronic housings, and medical devices. However, it may not be suitable for all applications, and careful consideration needs to be given to joint design, plastic material selection, and equipment requirements.
Hot Gas Welding:
Hot gas welding is a plastic welding process that uses a stream of heated gas to melt and join two plastic parts together. In this process, a welding rod made of the same plastic material as the parts to be joined is heated and melted using a hot air gun or other heating tools. The molten plastic from the welding rod is then used to join the two plastic parts together by pressing them together while the plastic is still molten.
Hot gas welding is commonly used for joining thermoplastic parts, particularly those that are too large or thick for other welding processes. It is also used for repairing plastic components such as tanks, pipes, and other equipment. It requires a skilled operator and careful attention to joint design, temperature control, and surface preparation to achieve consistent and high-quality results.
Extrusion welding:
Extrusion welding is a plastic welding technique that involves heating and melting a plastic material to form a continuous bead or line of molten plastic, which is then used to join two plastic parts together. In this process, a plastic welding rod is fed into a handheld extrusion welding tool, which heats the rod and melts it into a liquid state. The melted plastic is then extruded through a nozzle or die, forming a continuous bead of molten plastic that is used to weld the two plastic parts together.
Extrusion welding is commonly used for joining thermoplastic parts, particularly those that are large or have complex shapes. It is also used for repairing plastic components such as tanks, pipes, and other equipment.
Each of these methods has its unique advantages and is suitable for specific types of plastic materials and applications.
Process of Welding Plastics
The process of welding plastics depends on the type of welding method being used. However, here is a general process that can be followed:
- Prepare the surfaces to be welded: The surfaces to be welded should be clean and free of any debris or contaminants. This can be done by wiping them down with a solvent.
- Choose the welding method: Select the appropriate welding method based on the type of plastic and the desired application.
- Set up the welding equipment: Set up the equipment according to the manufacturer’s instructions.
- Heat the plastic: Apply heat to the plastic surfaces to be welded. The amount of heat and the time required will depend on the type of plastic and the welding method being used.
- Apply pressure: Apply pressure to the plastic parts to be joined. The amount of pressure required will depend on the type of plastic and the welding method being used.
- Allow the plastic to cool: Once the plastic has been welded, allow it to cool down and solidify.
- Finish the welded part: Trim any excess plastic and smooth out any rough edges to create a finished product.
It is essential to follow the manufacturer’s instructions and safety guidelines when welding plastics to ensure a successful and safe outcome.
Welding Plastic Pipes
The process of welding plastic pipes depends on the type of plastic and the welding method being used. Here is a general process for welding plastic pipes using the butt fusion welding method:
- Cut the pipes: Use a pipe cutter or saw to cut the pipes to the desired length, ensuring that the ends are square and clean.
- Prepare the pipes: Clean the ends of the pipes to be welded using a pipe scraper or sandpaper to remove any dirt, debris, or oxidation.
- Clamp the pipes: Use a clamping device to hold the pipes in place during the welding process.
- Heat the pipes: Heat the ends of the pipes using a heating element or a hot plate until they reach the melting point of the plastic.
- Join the pipes: Remove the heating element and quickly join the melted ends of the pipes together, ensuring that they are aligned and that the welding pressure is maintained until the plastic solidifies.
- Allow the joint to cool: Allow the joint to cool down and solidify before releasing the clamping device.
- Trim the joint: Use a pipe cutter or saw to trim any excess plastic from the joint and smooth out any rough edges.
It is important to follow the manufacturer’s instructions and safety guidelines when welding plastic pipes to ensure a successful and safe outcome.
Plastic Welding Kit
A plastic welding kit is a set of tools and equipment used for welding and repairing plastic materials. The kit typically includes a heating tool, welding rods, a scraper or sandpaper, and other accessories that may vary depending on the specific kit.
The heating tool in the kit is used to melt the plastic surface, which can then be joined or repaired using the welding rods. The welding rods are made of the same type of plastic as the material being welded and are used to fill in the gaps or cracks in the plastic.
The scraper or sandpaper is used to prepare the plastic surface before welding, ensuring that it is clean and free of any debris or contaminants that may affect the welding process.
A plastic welding kit can be used for various applications, including repairing broken plastic parts, sealing cracks and gaps, and even creating new plastic parts. They are commonly used in automotive, construction, and home repair projects.
It is important to choose the right type of plastic welding kit for the specific type of plastic being repaired or welded, as different plastics have different melting points and require different types of welding rods.
Is Plastic Welding Strong?
Yes, plastic welding can be very strong if done properly. The strength of a plastic weld depends on several factors, including the welding method, the type of plastic being welded, and the skill and experience of the operator. In general, some plastic welding methods, such as ultrasonic welding, vibration welding, and hot plate welding, can produce very strong and durable welds. These methods use heat and pressure to melt and fuse the plastic together, creating a strong bond between the two parts.
Other plastic welding methods, such as solvent welding and hot gas welding, can also produce strong welds but may be more susceptible to environmental factors, such as temperature and moisture, which can weaken the weld over time. It’s important to note that not all types of plastic can be welded, and some plastics are more difficult to weld than others. Additionally, proper surface preparation and joint design are critical for achieving strong welds.
Overall, with the right equipment, materials, and techniques, plastic welding can be a very strong and effective method for joining plastic parts.
Plastic Welding Machine
A plastic welding machine is a specialized piece of equipment used for joining two plastic parts together through a welding process. There are several types of plastic welding machines available, each designed for specific welding methods such as ultrasonic welding, hot plate welding, laser welding, and more.
In general, a plastic welding machine will consist of a power source, a heating element, a welding tool or fixture, and controls for regulating the welding process. The machine may also include additional features such as temperature sensors, timers, and pressure gauges to ensure proper welding conditions.
The type of plastic welding machine needed will depend on the specific welding method being used, the size and shape of the plastic parts being welded, and the desired strength and quality of the weld. Some machines are designed for large-scale production and may be fully automated, while others are smaller and more portable for on-site repairs and maintenance.
Plastic welding machines can be found in a variety of industries, including automotive, aerospace, medical, and manufacturing, and are used to create a wide range of plastic products and components.
Plastic Welding Gun
A plastic welding gun, also known as a heat gun, is a handheld tool that is used for plastic welding, particularly for the hot air welding method. It works by heating the plastic material to its melting point, allowing it to be fused together with another plastic part or component.
A plastic welding gun typically consists of a heating element, a fan or blower to direct hot air onto the plastic, and controls for adjusting the temperature and airflow. The gun may also include a nozzle or attachment to focus the heat on a specific area or joint.
Plastic welding guns are commonly used in automotive repair, construction, and fabrication industries for repairing or joining plastic parts, such as bumpers, dashboards, and other interior components. They are also used in the manufacturing of plastic products, such as PVC pipes, plastic sheets, and packaging materials.
Plastic welding guns are available in different sizes and power ratings, depending on the size and thickness of the plastic being welded. They are generally easy to use and can produce strong, durable welds when used correctly.