Computational Fluid Dynamics (CFD) has emerged as a cornerstone in the field of piping engineering, revolutionizing the way engineers analyze and design fluid flow within pipelines. In this write-up, we will learn the meaning of CFD and its applications in piping engineering covering the underlying principles, benefits, challenges, and the future directions of this powerful tool.
What is Computational Fluid Dynamics or CFD?
CFD or computational fluid dynamics is a specialized branch of fluid mechanics that employs numerical methods and algorithms to simulate and analyze fluid flow. In the context of piping engineering, CFD provides a virtual environment to study the behavior of liquids and gases within pipes. This simulation allows engineers to gain insights into complex phenomena such as turbulence, heat transfer, and pressure distribution.
Governing Equations
At the core of CFD are the Navier-Stokes equations, which describe the motion of fluid substances. These equations, coupled with additional equations for energy and mass transfer, form the foundation for simulating fluid flow in pipes. The complexity of these equations often necessitates the use of numerical methods for solving them, and various algorithms, such as finite difference, finite volume, and finite element methods, are employed in CFD simulations.
Importance of Mesh Generation
Mesh generation is a critical aspect of CFD simulations. The computational domain is discretized into a mesh of cells or elements, defining the spatial resolution of the simulation. The quality of the mesh directly impacts the accuracy of the results. Engineers must strike a balance between having a fine enough mesh to capture details and a coarse enough mesh to ensure computational efficiency.
Applications of CFD in Piping Engineering
CFD can be used to simulate various problems in piping engineering. Some of the typical applications include:
Fluid Flow Analysis
One of the primary applications of CFD in piping engineering is fluid flow analysis. Engineers can simulate the movement of liquids and gases within pipes, predicting velocity profiles, pressure distributions, and flow patterns. This information is invaluable for optimizing pipe designs to achieve desired performance metrics.
Heat Transfer Simulation
CFD facilitates the simulation of heat transfer within piping systems. Engineers can analyze temperature distributions, identify areas of high heat flux, and optimize thermal management strategies. This is particularly crucial in industries where precise temperature control is essential, such as chemical processing and power generation.
Species Transport
In cases involving multiple fluid components or chemical reactions, CFD can simulate species transport within pipes. This capability is vital in industries where the mixing of different substances is a critical consideration, such as in chemical and pharmaceutical manufacturing.
Multiphase Flow
CFD can handle multiphase flow scenarios, where different phases of matter (e.g., gas-liquid or liquid-solid) coexist. This is pertinent in industries like oil and gas, where pipelines may transport a combination of liquids and gases.
Transient Analysis
Transient simulations in CFD allow engineers to study how fluid flow parameters change over time. This is essential for understanding dynamic behaviors in piping systems, such as startup/shutdown processes or sudden changes in flow rates.
Benefits of CFD in Piping Engineering
The main advantages of using CFD in piping engineering are:
Accurate Simulation and Visualization
CFD provides a high level of accuracy in simulating fluid dynamics, offering engineers a detailed view of how fluids behave within a piping system. Visualization tools enable the representation of complex flow patterns, aiding in the interpretation of results.
Optimization of Designs
The iterative nature of CFD simulations allows engineers to optimize piping designs efficiently. By assessing various design scenarios, engineers can identify the most efficient configurations that meet performance requirements, reducing the need for costly physical prototypes and testing.
Early Detection of Flow Anomalies
CFD simulations can identify potential issues such as turbulence, cavitation, and pressure drops that might go unnoticed in traditional analyses. Detecting these anomalies early in the design phase enables engineers to make informed decisions to mitigate or eliminate these issues before implementation.
Thermal Analysis
The ability of CFD to simulate thermal effects within pipes is a significant advantage. Engineers can analyze temperature distributions and heat transfer, ensuring that piping systems can handle thermal loads effectively. This is crucial in industries where temperature control is paramount.
Cost Reduction
By leveraging CFD in the design phase, engineers can reduce costs associated with physical prototyping and testing. The ability to simulate and predict fluid behavior accurately minimizes the risk of design flaws, leading to more cost-effective and reliable piping systems. Fig. 1 (Image Credit: https://www.savener.es/) below shows a typical example of CFD in Piping.
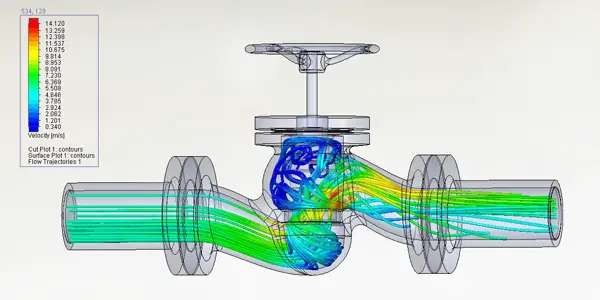
Some of the typical applications of CFD in piping can be presented as follows:
- Oil and Gas Industry: In the oil and gas sector, CFD has been instrumental in optimizing the layout of pipelines. Simulations help engineers understand fluid behavior over long distances, ensuring that the design minimizes frictional losses, and pressure drops, and ensures a consistent flow of fluids.
- Power Generation: In thermal power generation, CFD has played a vital role in designing cooling systems. Simulations allow engineers to optimize the flow of coolant, ensuring efficient heat dissipation and preventing overheating of critical components.
- Chemical Processing: In chemical processing plants, CFD is utilized to simulate the mixing of different substances within piping systems. This helps in optimizing the design to achieve the desired chemical reactions and product quality.
Software Programs for Computational Fluid Dynamics
Several software programs are widely used for studying Computational Fluid Dynamics (CFD) in piping and pipeline networks. These tools offer a range of features for simulating fluid flow, heat transfer, and other related phenomena. Here are some of the best-known software programs in this domain:
ANSYS Fluent:
Key Features: ANSYS Fluent is a widely used CFD software that provides a comprehensive set of tools for simulating fluid flow, heat transfer, and chemical reactions. It offers a user-friendly interface and robust solver capabilities, making it suitable for a variety of applications, including piping and pipeline network analysis.
COMSOL Multiphysics:
Key Features: COMSOL is a multiphysics simulation software that allows engineers to model and simulate various physical phenomena, including fluid flow and heat transfer. It supports both laminar and turbulent flow simulations, making it applicable to a wide range of piping scenarios.
OpenFOAM:
Key Features: OpenFOAM is an open-source CFD software with a large user community. It provides a flexible and extensible framework for solving complex fluid flow problems, including those related to piping and pipeline networks. OpenFOAM is known for its versatility and can be customized for specific applications.
CFD-ACE+ (by ESI Group):
Key Features: CFD-ACE+ is a CFD software package that offers a range of capabilities for fluid flow, heat transfer, and chemical reactions. It is suitable for analyzing multiphase flows, combustion, and other phenomena relevant to piping systems. The software provides a user-friendly interface and advanced simulation capabilities.
Simcenter STAR-CCM+ (by Siemens Digital Industries Software):
Key Features: Simcenter STAR-CCM+ is a comprehensive CFD software package that covers a broad spectrum of applications, including piping and pipeline network simulations. It features robust meshing tools, advanced physics models, and parallel processing capabilities for efficient simulations.
PIPE-FLO (by Engineered Software, Inc.):
Key Features: PIPE-FLO is a specialized software tool designed specifically for piping system analysis and optimization. It provides a user-friendly interface for modeling and simulating fluid flow in pipelines, considering factors such as pipe sizing, pump selection, and pressure drop calculations.
Autodesk CFD:
Key Features: Autodesk CFD is a simulation tool that integrates with other Autodesk products, offering a seamless workflow for engineers. It provides capabilities for fluid flow and thermal simulations, making it suitable for analyzing piping and heat transfer in industrial applications.
FloMASTER (by Mentor, a Siemens Business):
Key Features: FloMASTER is a thermal-fluid system simulation tool designed for analyzing complex piping and fluid systems. It allows engineers to model and simulate fluid flow, heat transfer, and pressure drop in piping networks. The software is known for its ease of use and efficiency in system-level simulations.
AFT Fathom (by Applied Flow Technology):
Key Features: AFT Fathom is a specialized software tool for fluid dynamic simulation of piping systems. It provides capabilities for modeling and analyzing fluid flow, pressure drop, and heat transfer in pipelines. AFT Fathom is widely used in industries such as oil and gas, chemical, and water distribution.
FLOW-3D:
Key Features: FLOW-3D is a CFD software known for its capabilities in simulating free-surface flows and complex fluid interactions. While it is often used in applications such as water and environmental engineering, it can also be applied to specific scenarios within piping systems.
Computational Fluid Dynamics has emerged as a transformative force in piping engineering, providing engineers with the tools to simulate and understand fluid behavior in unprecedented detail. From fluid flow analysis to thermal simulations, CFD has diverse applications that contribute to the optimization and reliability of piping systems. While challenges exist, ongoing advancements in computing power, algorithms, and user accessibility position CFD as an indispensable tool for the future of piping engineering. By harnessing the capabilities of CFD, engineers can navigate the complexities of fluid dynamics with confidence, ultimately contributing to the development of safer, more efficient, and sustainable industrial systems.