The Oil and Gas industry uses a vast majority of equipment for its operation. They are broadly classified into two groups; Static or Stationery equipment with no moving parts and Rotary or Rotating equipment with moving parts. The rotating equipment forms the backbone of numerous processes, ensuring the extraction, transportation, refining, and distribution of hydrocarbons. The significance of rotating equipment in this industry cannot be overstated, as it plays a pivotal role in converting energy, facilitating fluid movement, and maintaining operational efficiency. In this article, we will learn about the major rotating equipment that is part of the oil and gas industry, providing a deep understanding of its definition, applications, types, and the specific functions each type serves.
What is a Rotary Equipment?
Rotating equipment in the oil and gas industries is the machinery that has at least one moving component. They use kinetic energy to move fluids, gases, and other commodities from the inlet to the outlet. Rotating equipment refers to a class of machinery that operates by using rotational motion to perform various tasks in the oil and gas industry. These machines are characterized by their ability to rotate around an axis, converting energy from one form to another. The rotational motion can be harnessed to pump, compress, generate power, or facilitate other essential processes in the production, refining, and distribution of oil and gas.
Applications of Rotating Equipment in the Oil and Gas Industry
Rotary equipment finds extensive applications across different phases of the oil and gas industry. These applications include:
- Exploration and Production:
In the exploration and production phase, rotating equipment is integral to drilling operations. Mud pumps, a type of rotating equipment, circulate drilling fluid to cool and lubricate the drill bit. Additionally, pumps are employed to transport extracted hydrocarbons from wells to processing facilities. - Refining:
During the refining process, compressors are crucial for pressurizing and moving gases for catalytic processes, while turbines generate power for various refining stages. Pumps handle the transfer of crude oil and refined products throughout the refining process. - Transportation:
Rotating equipment plays a key role in the transportation of oil and gas through pipelines. Compressors maintain the pressure required for long-distance pipeline transport, while pumps assist in loading and unloading at terminals. - Distribution:
In the distribution phase, pumps are essential for moving refined products from storage facilities to end-users. Compressors also play a critical role in maintaining the pressure in gas distribution networks.
Types of Rotating Equipment in the Oil and Gas Industry
Rotating equipment in the oil and gas industry encompasses a variety of machines designed to perform specific functions. The main types include:
- Pumps
- Compressors
- Turbines
- Fans and Blowers
Pumps:
Pumps in the oil and gas industry are primarily responsible for the movement of fluids. Centrifugal pumps utilize a rotating impeller to increase the fluid’s velocity and then convert this kinetic energy into potential energy, facilitating the fluid’s movement. These pumps are widely used for various applications, including transferring crude oil, water injection in reservoirs for enhanced oil recovery, and handling different chemicals in the refining process.
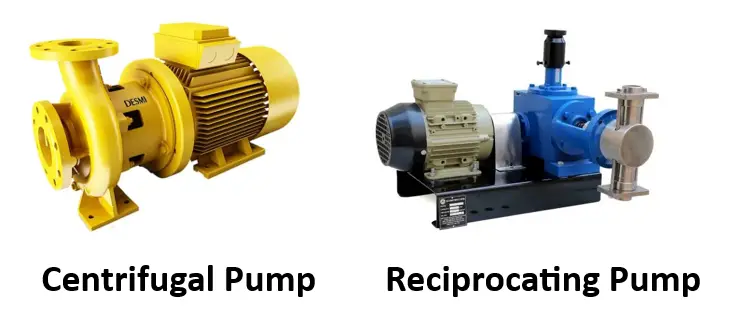
Positive displacement pumps, on the other hand, displace a fixed volume of fluid with each rotation, ensuring a constant flow. This type of pump is preferred for applications requiring precise control of flow rates, such as injecting chemicals into a process stream or transferring viscous fluids like heavy crude oil.
Compressors:
Compressors are vital for increasing the pressure of gases in the oil and gas industry. Centrifugal compressors utilize a rotating impeller to accelerate gas radially outward, increasing its pressure. These compressors are suitable for handling large volumes of gas and are often used in pipeline transportation and gas processing facilities.
Reciprocating compressors operate through a piston-cylinder mechanism, where the piston compresses the gas during its reciprocating motion. This type of compressor is well-suited for applications that require high pressure, such as gas lift in oil wells or the compression of natural gas for transportation.
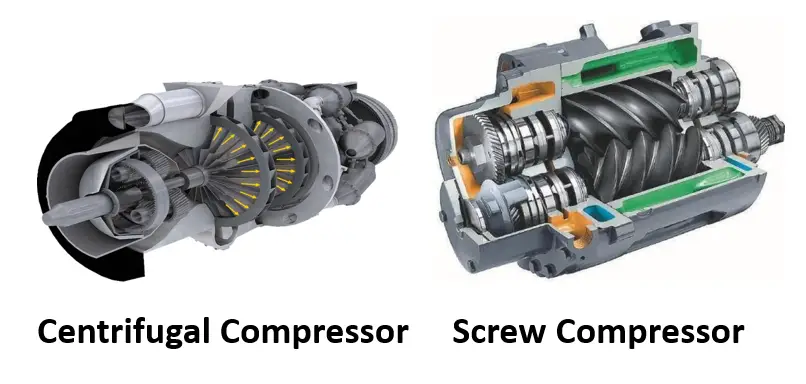
Rotary compressors, including screw compressors and vane compressors, operate through the continuous rotary motion of vanes or screws. They are commonly used in midstream and downstream processes for applications like gas gathering, gas processing, and refining.
Turbines:
Gas turbines are employed for power generation in the oil and gas industry. These turbines convert the energy from burning fuel into mechanical energy through combustion. The hot gases produced during combustion drive the turbine blades, generating rotational motion that is harnessed to drive a generator. Gas turbines are widely used in power plants associated with oil and gas facilities, providing a reliable source of electricity for various operations.
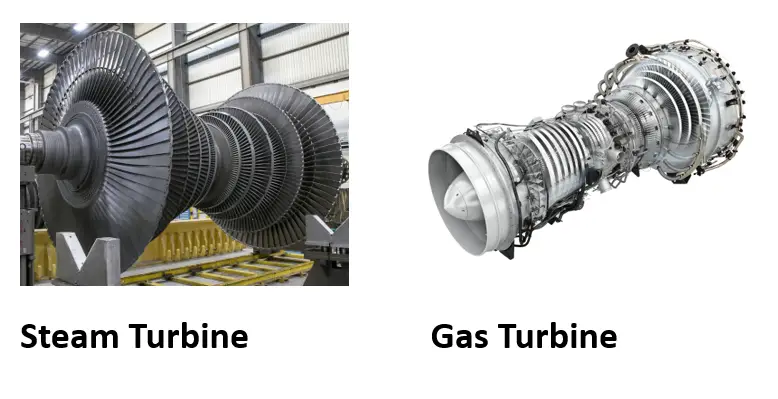
Steam turbines, another type of rotating equipment, utilize high-pressure steam to generate mechanical energy. In the oil and gas industry, steam turbines are often used in conjunction with steam generators to produce power for refining processes. The steam, produced by burning fuel, expands through the turbine, causing the blades to rotate and drive a generator.
Fans and Blowers:
Fans and blowers are essential for maintaining proper air circulation and managing temperatures in industrial processes. Axial fans move air parallel to the shaft around which the blades rotate. These fans are often used for applications like cooling towers in refineries, where a large volume of air needs to be moved.
Centrifugal fans, on the other hand, move air radially outward, creating a centrifugal force that propels the air stream. These fans are versatile and find applications in dust collection systems, ventilation, and air circulation in various refinery processes.
Positive displacement blowers, also known as rotary lobe blowers, displace a fixed volume of air with each rotation. They are commonly used for pneumatic conveying, a process where materials like cement or fly ash are transported through pipelines using air.
Centrifugal blowers, similar to centrifugal fans, accelerate air radially outward. They are often used in applications requiring a higher pressure, such as combustion air supply for burners in industrial furnaces.
Rotating equipment is the lifeblood of the oil and gas industry, ensuring the seamless flow of hydrocarbons from extraction to distribution. The diverse types of rotating equipment serve specific functions critical to the success of various processes within the industry. From pumps facilitating fluid movement to compressors increasing gas pressure, and turbines generating power, each type