Galvanization or Galvanizing is one of the most widely used manufacturing processes of applying a thin zinc coating over steel or iron material for the purpose of protecting it from corrosion or rusting. Once this is done the steel or iron is called galvanized steel or galvanized iron. That zinc coating (silver color) in galvanized material shields (barrier) the metal from the surrounding environment. Thus galvanization extends the life of the base metal (Steel) to a considerable extent. That zinc coating is applied in several layers as per requirement.
In a corrosive environment, Galvanized Steel is one of the cost-effective alternative solutions to avoid using costly materials like SS or DSS. Galvanizing also prevents the metal from “galvanic corrosion” as the Zinc layer acts as an anode and slows the corrosion tendency of the base metal.
Methods of Galvanization/ Galvanizing Methods
Galvanization is achieved by various methods as listed below:
- Hot-Dip Galvanization
- Electro-galvanization
- Pre-galvanization
- Galvannealing
Hot-Dip Galvanization
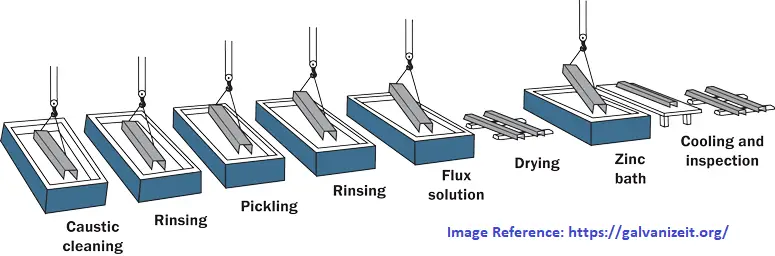
The hot-dip galvanization process provides long-lasting, maintenance-free metal at a cheap cost and the process is quite simple. In the Hot-Dip Galvanizing process, the base metal is dipped into a pool of molten zinc. Fig. 1 shows the steps involved in the complete process. There are three major steps that are followed in the hot-dip galvanizing process.
- Surface Preparation
- Degreasing
- Stripping
- Rinsing
- Fluxing and
- Drying
- Galvanizing and
- Post-Process Treatment.
Electro-galvanization
In the Electro-galvanizing process, Zinc ions are transferred to the base metal by utilization of an electrical current source in an electrolyte solution. Electro-galvanizing is normally applied continuously.
Pre-galvanization
Pre-galvanizing is performed at the steel mill, usually on materials that already have a specific shape. After cleaning, The metal is passed through a pool of hot molten zinc similar to the hot-dip galvanization process and then recoiled. This method offers large-scale galvanization.
Galvannealing
Galvannealing is basically a combination of two methods; hot-dip galvanization and annealing. This method produces a specialized high-quality coating on steel. The process involves hot-dipping and then instantaneous annealing, to produce a matte gray finish.
Galvanization Standards
The codes and standards that govern the galvanization process are listed below:
- ISO 1461
- EN/ISO 14713-1 & 2
- BS 7371-Part 6
- EN 10348‑2
- BS 3083
- EN 15773
- ASTM A123/A123M
- ASTM A153/A153M
- ASTM A767/A767M
- CSA G164
- ASTM B6
- ASTM A143/A143M
- ASTM A384/A384M
- ASTM A385/A385M
- ASTM A780
- ASTM D6386
- ASTM D7803
- ASTM E376
Need for Galvanized Steel Pipes
There are various services where care should be taken to avoid rusting of the pipeline as it might be hazardous to personnel, cause damage, malfunction of equipment, instruments, etc. so for that reason, the piping is galvanized. Galvanized pipes can work satisfactorily for up to 70 years. The other advantages that galvanized steel pipe (Fig. 2) offers are
- Reduced cost as compared to stainless.
- Very Little maintenance which results in the lowest long-term cost.
- Highly Durable. Hence, Long life expectancy.
- Reliable performance.
- Resistance to mechanical damage.
- Good protection against rusting and galvanic corrosion.
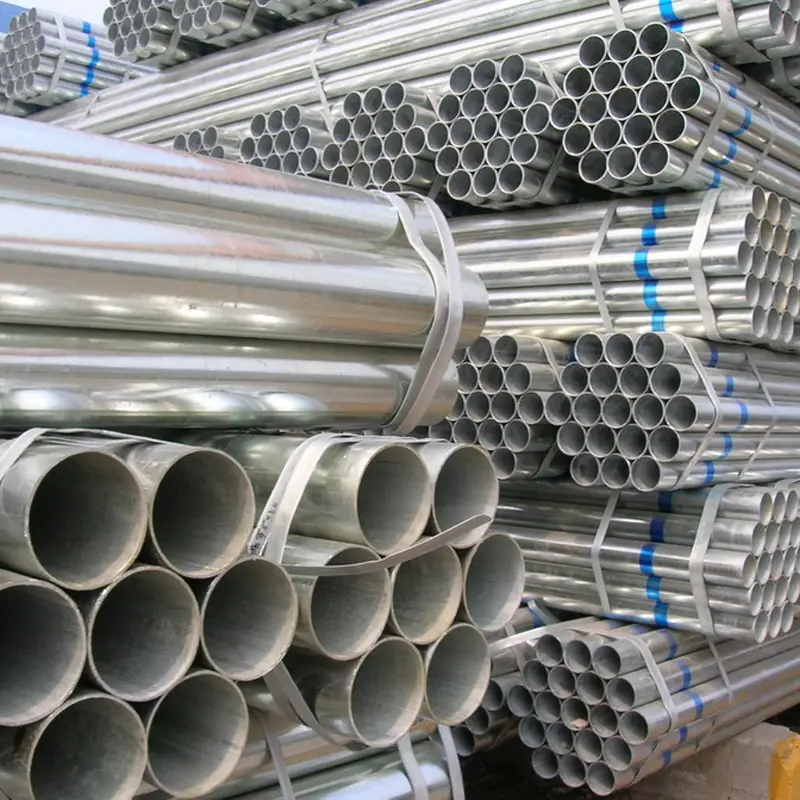
However, for piping applications, the only disadvantage is that galvanized pipes can not be welded (Click here to know how to weld galvanized pipes). So, clamped pipe supports are used for galvanized piping systems.
Difference between Hot-dip Galvanization and Electro-Galvanization
Below are the differences between Hot-dipped galvanization and Electro-galvanization. And the advantages of one over the other-
Hot dip galvanization | Electro-galvanization |
In hot-dip galvanization, a stringent cleaning procedure is followed (usually termed as a 7-bath process: cleaning in alkaline solution, water rinsing, pickling, water rinsing, pickling, water rinsing, fluxing). | The cleaning Procedure in electro-galvanization is not stringent. |
Governing codes and standards are ASTM A123; ISO 1461; IS 2629 or BS 729 | IS 1573 governs the Electro-galvanization process |
Highly Durable; of the order of 20-50 years | Comparatively low life |
It produces a Fe-Zn alloy layer on the steel surface and leaves a coat of pure zinc on the outer surface. The alloy is very hard. Usual abrasion does not damage the coating although it may damage the soft pure zinc on the top | Produces a layer of Zn on the surface which is not continuous with steel metallurgically |
Steel is dipped into the molten bath of Zinc @460ºC to achieve the coat | Steel is made the cathode in the electrolytic cell thereby forming the coating by an Electroplating process |
The surface finish is not smooth, or dull finish. | Good surface finish |
Depending on the dipping duration, the coating thickness is 80-100µm. It is also affected by the composition & roughness of steel | Normally coating thickness is 10-12 µm. Coating thickness depends on the current density and temperature of the electrolyte |
With normal coat thickness about 40% more expensive than electro-galvanizing | A normal coat thickness is cheaper in comparison to hot dip galvanizing. However, at higher coating thickness the cost increases proportionately and hence becomes exceptionally expensive. |
Non-uniform coating | Uniform coating |
Suitable for any size | Suitable for small components |
Why is Zinc used in the Galvanization of Steel Pipes?
Zinc is used in the galvanization of steel pipes primarily for its ability to provide excellent corrosion protection. Here are the key reasons why zinc is used for galvanization:
1. Corrosion Resistance
- Barrier Protection: Zinc serves as a physical barrier between the steel and environmental elements such as moisture and oxygen, which are necessary for rust formation.
- Sacrificial Protection: Zinc has a lower electrochemical potential compared to steel. This means that zinc will corrode preferentially, sacrificing itself to protect the steel underneath. This sacrificial anode effect ensures that even if the zinc coating is scratched or damaged, the underlying steel remains protected from corrosion.
2. Durability and Longevity
- Extended Lifespan: Galvanized steel pipes have a significantly longer lifespan compared to non-galvanized steel pipes. The zinc coating can protect the steel for decades, depending on the environmental conditions.
- Low Maintenance: The corrosion-resistant properties of zinc reduce the need for frequent maintenance and repairs, making galvanized steel pipes a cost-effective option over the long term.
3. Self-Healing Properties
- Galvanic Action: When the zinc coating is damaged, the surrounding zinc will corrode to protect the exposed steel. This galvanic action helps to “heal” minor scratches and abrasions, maintaining the protective barrier.
4. Ease of Application
- Hot-Dip Galvanization: The process of hot-dip galvanization, where steel pipes are submerged in molten zinc, ensures a uniform and thorough coating. This method is efficient and widely used in industry.
- Adhesion and Coverage: Zinc adheres well to steel surfaces, providing consistent coverage that is difficult to achieve with other coatings. The metallurgical bond formed between zinc and steel during galvanization enhances durability and protection.
5. Cost-Effectiveness
- Initial Investment: Although the initial cost of galvanized steel pipes may be higher than non-galvanized pipes, the extended lifespan and reduced maintenance costs make it a cost-effective solution in the long run.
- Availability and Process Efficiency: Zinc is relatively abundant and the galvanization process is well-established, making it a practical and economical choice for protecting steel pipes.
6. Environmental Benefits
- Recyclability: Both steel and zinc are recyclable materials. Galvanized steel can be recycled without losing its valuable properties, contributing to sustainable practices in construction and manufacturing.
- Reduced Environmental Impact: By extending the lifespan of steel pipes and reducing the need for replacements and maintenance, galvanization helps lower the overall environmental impact associated with steel production and usage.
Hot-Dip Galvanization Video Tutorial
The following hot-dip galvanization video tutorial by the American Galvanizers Association clearly explains the Galvanization process.