Oxygen cutting, also known as oxy-fuel cutting or flame cutting, is a thermal cutting process used to sever or shape metal materials. It involves the use of a high-temperature flame generated by the combustion of oxygen and fuel gas, typically acetylene or propane. The process relies on the exothermic reaction between oxygen and the fuel gas, which produces a focused flame with temperatures reaching around 3,500 degrees Celsius (6,332 degrees Fahrenheit).
How Does Oxygen Cutting Work?
Here’s a general overview of the oxygen-cutting process:
- Equipment setup: A cutting torch is used, consisting of a handle, oxygen, and fuel gas valves, a mixing chamber, and a cutting tip. The gases are supplied from separate cylinders and mixed in the torch.
- Preheating: The cutting torch flame is adjusted to produce a high-temperature preheating flame. The preheating flame is directed onto the metal surface, which raises its temperature to the ignition point.
- Piercing: Once the metal is preheated, the oxygen valve is opened to release a high-velocity jet of pure oxygen through the cutting tip. The oxygen reacts with the hot metal, creating an exothermic reaction that generates intense heat. The heat causes the metal to oxidize rapidly, forming a molten metal oxide.
- Cutting: The high-pressure oxygen jet is then moved along the preheated cut line, directed into the molten metal oxide. The exothermic reaction between oxygen and the molten metal creates additional heat, and the metal is blown away as slag or expelled as sparks.
- Continuous cutting: The torch continues to move along the desired cutting path, with the preheating flame heating the metal ahead of the cutting line, and the oxygen jet severing the material.
Oxygen cutting is primarily used for cutting carbon steels, but it can also be used on some low-alloy steels and cast iron. The process is widely employed in metal fabrication, manufacturing, and construction industries for various applications, such as cutting plates, sheets, pipes, and structural components. Fig. 1 below shows the process of Oxygen Cutting
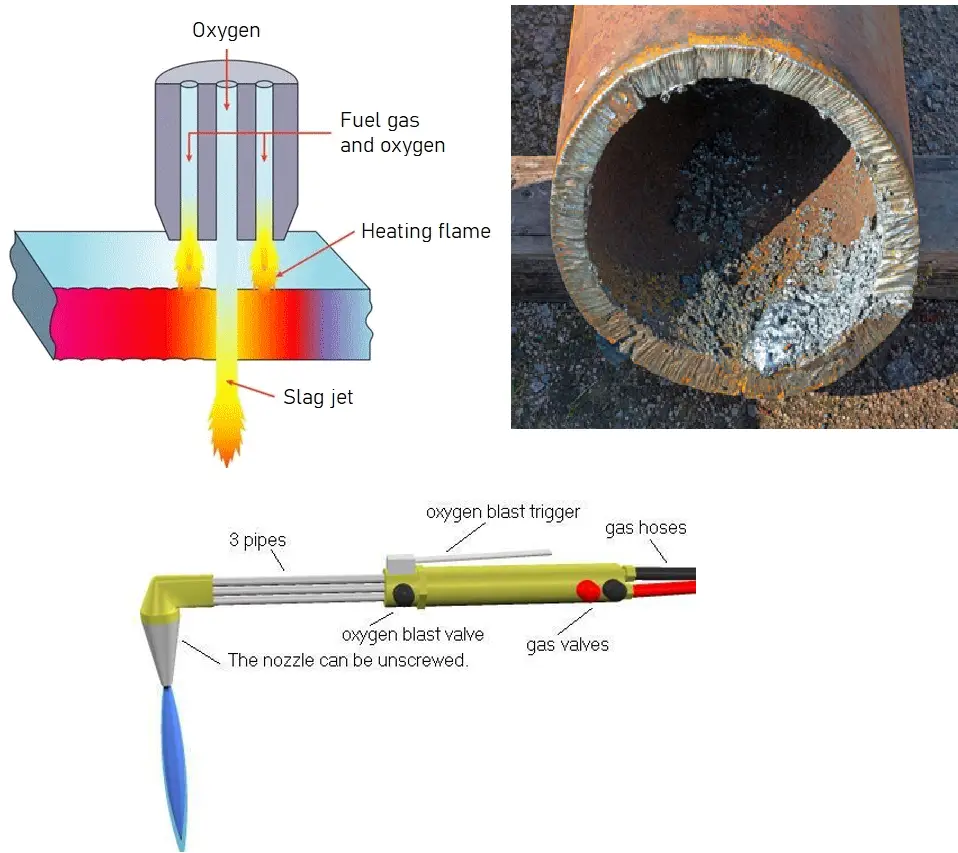
Gases Used for Oxygen Cutting
In the oxygen-cutting process, two primary gases are used:
Oxygen:
Oxygen is the main gas used for cutting. It supports the combustion process and reacts with the metal to create the exothermic reaction required for cutting. High-purity oxygen is typically used to ensure efficient and effective cutting.
Fuel Gas:
Fuel gas is required to provide the heat source for the cutting process. The choice of fuel gas depends on factors such as availability, cost, and specific requirements. The most commonly used fuel gases are:
- Acetylene: Acetylene is a widely used fuel gas in oxy-fuel cutting. It has a high flame temperature and provides excellent heat intensity, making it suitable for cutting thick metals.
- Propane: Propane is another commonly used fuel gas. It has a lower flame temperature compared to acetylene but still provides sufficient heat for cutting various metal thicknesses.
- Natural Gas: In some applications, natural gas may be used as a fuel gas for oxygen cutting. However, it has a lower flame temperature compared to acetylene or propane and may not be suitable for cutting thicker materials.
Oxygen Cutting Equipment
Oxygen-cutting equipment typically consists of several key components that work together to facilitate the cutting process. Here are the main parts of oxyfuel cutting equipment:
- Oxygen Cylinder: The oxygen cylinder contains high-pressure, compressed oxygen gas. It serves as the supply source for the oxygen required in the cutting process.
- Fuel Gas Cylinder: The fuel gas cylinder holds the compressed fuel gas, such as acetylene, propane, or natural gas. The fuel gas is mixed with oxygen to create the necessary flame for cutting.
- Regulators: Regulators are devices attached to the cylinders to control and regulate the flow and pressure of oxygen and fuel gas as they leave the cylinders. They ensure a consistent and safe supply of gases to the cutting torch.
- Cutting Torch Handle: The cutting torch handle is the handheld part of the equipment. It provides a grip for the operator to hold and control the torch during the cutting process. The handle typically has valves to control the flow of oxygen and fuel gas, as well as other features such as a trigger or lever for ignition.
- Cutting Tips: Cutting tips are replaceable attachments at the end of the cutting torch. They are designed to shape and direct the flow of the oxygen and fuel gas mixture, creating the desired flame for cutting. Cutting tips come in various sizes and shapes to accommodate different cutting applications and metal thicknesses.
- Mixing Chamber: The mixing chamber is located inside the cutting torch handle. It is where the oxygen and fuel gas are combined in the correct proportions before they are ignited. The mixing chamber ensures a well-mixed and stable flame for cutting.
- Hoses: Hoses connect the regulators to the cutting torch handle, allowing the flow of oxygen and fuel gas from the cylinders to the torch. These hoses are typically flexible and designed to withstand high pressures.
- Flashback Arrestors: Flashback arrestors are safety devices installed between the hoses and the regulators. They are designed to prevent the flame from traveling back into the hoses, cylinders, or regulators. Flashback arrestors help to minimize the risk of accidents and ensure safer operation.
- Ignition System: The ignition system is responsible for igniting the oxygen and fuel gas mixture to initiate the cutting process. It can consist of a manual ignition method using a spark lighter or an automatic ignition system integrated into the torch handle.
Other notable components are:
- Non-Return Valve/ Check valve
- Torch
- Acetylene oxygen cutting torch,
- Oxygen cutting torch,
- Propane oxygen-cutting torch
Acetylene Oxygen Cutting Torch:
An acetylene oxygen cutting torch, also known as an oxy-acetylene cutting torch, is a type of cutting torch used in oxygen-cutting processes. It is designed to handle acetylene gas as the fuel gas and oxygen as the oxidizer. The torch typically has a handle with valves to control the flow of oxygen and acetylene, a mixing chamber to mix the gases, and a cutting tip at the end.
The acetylene oxygen-cutting torch produces a high-temperature flame by combining acetylene and oxygen in the correct ratios. The acetylene gas serves as the fuel source and, when combined with oxygen, undergoes combustion, generating the necessary heat for cutting. This type of cutting torch is commonly used in metal fabrication, construction, and other applications where a high flame temperature is required.
Oxygen Cutting Torch:
An oxygen-cutting torch, also known as an oxy-fuel cutting torch or flame-cutting torch, is a torch specifically designed for the oxygen-cutting process. It is a versatile tool that can use various fuel gases, such as acetylene, propane, or natural gas, depending on the specific application and availability.
The oxygen-cutting torch consists of a handle with valves to control the flow of oxygen and the chosen fuel gas, a mixing chamber where the gases are combined, and a cutting tip. The torch is connected to oxygen and fuel gas cylinders through hoses and regulators. The torch produces a high-temperature flame by mixing oxygen and the fuel gas, allowing the metal to be melted and cut.
Propane Oxygen Cutting Torch:
A propane oxygen-cutting torch is a type of oxygen-cutting torch that uses propane gas as the fuel source. Propane is a commonly used fuel gas in oxy-fuel cutting, known for its high energy content and lower cost compared to acetylene. The torch is designed to handle oxygen and propane and typically has similar components to other oxygen-cutting torches.
When the propane gas is combined with oxygen in the torch, it undergoes combustion, generating the required heat for cutting. The propane oxygen cutting torch is used in various applications, including metal fabrication, construction, and automotive industries, where it provides sufficient heat for cutting different metal thicknesses.
Role of Oxygen in Oxygen Cutting
Oxygen plays a crucial role in the oxygen-cutting process. It serves several important functions throughout the cutting operation. Here are the key roles of oxygen in oxygen cutting:
- Combustion: Oxygen is the primary oxidizer in the oxygen-cutting process. When combined with a fuel gas, such as acetylene or propane, in the correct proportions, oxygen supports the combustion reaction. The combustion of the fuel gas releases heat energy, which is necessary for melting and severing the metal.
- Heat Generation: Oxygen is responsible for generating the intense heat required to melt and cut through the metal. As the oxygen reacts with the preheated metal, an exothermic oxidation reaction occurs. This reaction produces a significant amount of heat energy, raising the temperature of the metal to its melting point and facilitating the cutting process.
- Oxidation: Oxygen is the oxidizing agent in the oxygen-cutting process. It reacts with the metal being cut and initiates an oxidation reaction. The high-temperature oxygen jet rapidly oxidizes the metal, causing it to form a molten metal oxide. This oxidation reaction releases additional heat energy, aiding in the cutting process.
- Metal Removal: The oxygen stream in oxygen cutting not only provides the heat for cutting but also aids in removing the molten metal from the cutting path. The high-pressure oxygen jet blows away the molten metal oxide or expels it as sparks, clearing the way for the cutting process and ensuring a clean and precise cut.
- Speed and Efficiency: Oxygen cutting with pure oxygen allows for faster cutting speeds compared to air-based cutting methods. The high purity of oxygen ensures efficient combustion and oxidation, resulting in quicker metal severing. Oxygen also allows for improved energy transfer to the metal, increasing the overall cutting efficiency.
Applications of Oxygen Cutting
Oxygen cutting, or oxy-fuel cutting, has a wide range of applications in various industries. Here are some common applications:
- Metal Fabrication: Oxygen cutting is extensively used in metal fabrication processes. It is employed to cut and shape metal components, such as plates, sheets, beams, and pipes. Metal fabricators utilize oxygen cutting for tasks like creating openings, separating sections, trimming edges, and preparing parts for further processing.
- Construction: Oxygen cutting plays a vital role in construction projects. It is used to cut structural steel elements, including beams, columns, and plates. Contractors rely on oxygen cutting for tasks like modifying or adapting metal structures, fabricating connections, and preparing materials for welding or assembly.
- Shipbuilding: Shipbuilding industries utilize oxygen cutting for various purposes. It is employed to cut and shape metal plates used in the construction of ship hulls, decks, bulkheads, and other structural components. Oxygen cutting is also used to prepare the edges of plates for welding and to dismantle or salvage metal structures.
- Automotive Industry: In the automotive sector, oxygen cutting is employed for different applications. It is used to cut and shape metal components for vehicles, such as chassis, frames, exhaust systems, and body parts. Oxygen cutting is also utilized in automotive repair and maintenance for tasks like removing damaged sections, cutting through bolts or brackets, and modifying metal structures.
- Demolition and Salvage: Oxygen cutting is employed in demolition and salvage operations. It helps to dismantle or cut through metal structures and components in buildings, bridges, industrial plants, and other infrastructure. Oxygen cutting allows for precise and controlled severing of materials during the demolition process.
- Scrap and Recycling: Oxygen cutting is utilized in scrap yards and recycling facilities. It enables the cutting and processing of metal materials into manageable sizes for recycling and reuse. Oxygen cutting helps in separating different metal components and preparing them for subsequent recycling processes.
- Artistic and Decorative Applications: Oxygen cutting is also employed in artistic and decorative applications. Metal artists and sculptors use oxygen cutting to create intricate designs, patterns, and shapes on metal sheets or plates. It allows for precise and detailed cutting, enabling the realization of artistic visions.
Characteristics of Oxygen Cutting
Oxygen cutting, also known as oxy-fuel cutting or flame cutting, possesses several key characteristics that make it suitable for specific cutting applications. Here are the main characteristics of oxygen cutting:
- Versatility: Oxygen cutting is versatile and can be used to cut a wide range of materials, including carbon steels, low-alloy steels, and cast iron. It is particularly effective for cutting thick materials.
- Heat Intensity: Oxygen cutting produces a high-temperature flame with temperatures reaching around 3,500 degrees Celsius (6,332 degrees Fahrenheit). The intense heat generated by the combustion of oxygen and fuel gas allows for efficient and rapid cutting.
- Material Thickness: Oxygen cutting is well-suited for cutting thick metal materials. It can effectively cut through heavy plates, beams, pipes, and other structural components.
- Portability: Oxygen-cutting equipment is relatively portable, making it suitable for on-site or remote cutting operations. It can be used in various work environments, including construction sites and fabrication shops.
- Cost-effective: Oxygen cutting is generally more cost-effective compared to some other cutting methods, such as plasma cutting or laser cutting. The equipment and fuel gases used in oxygen cutting are often more affordable, making it a cost-efficient option for many applications.
- Ease of Operation: Oxygen cutting is relatively easy to operate and does not require extensive technical expertise. With proper training and adherence to safety guidelines, operators can quickly learn to perform oxygen-cutting tasks effectively.
- Wide Range of Applications: Oxygen cutting finds applications in diverse industries, including metal fabrication, construction, shipbuilding, automotive, and demolition. It is commonly used for tasks such as cutting plates, sheets, and structural components and preparing materials for welding or assembly.
- Surface Finish: Oxygen cutting can result in a rougher cut surface compared to some other cutting methods. The cutting process may produce slag or dross that needs to be cleaned or removed after cutting.
- Equipment Requirements: Oxygen cutting requires specific equipment, including an oxygen-cutting torch, appropriate fuel gas cylinders, regulators, hoses, and safety devices like flashback arrestors. Proper maintenance and inspection of equipment are essential for safe and effective operation.
Safety Considerations During Oxygen Cutting
Safety is paramount when performing oxygen cutting due to the high temperatures, potential hazards, and combustible nature of the process. Here are some essential safety measures to follow during the oxygen-cutting process:
Adequate Training:
Ensure that operators have received proper training in oxy-fuel cutting techniques, equipment operation, and safety procedures. Training should cover topics such as handling cylinders, setting up equipment, proper torch operation, and emergency protocols.
Ventilation:
Ensure that the work area is well-ventilated to prevent the accumulation of flammable gases, fumes, or vapors. Adequate ventilation helps disperse any potential hazards and maintain a safe working environment.
Personal Protective Equipment (PPE):
Operators should wear appropriate personal protective equipment, including:
- Flame-resistant clothing: Wear fire-resistant clothing, such as a welding jacket or apron, to protect against sparks and molten metal.
- Eye protection: Wear safety goggles or a full-face shield to protect the eyes from radiant heat, sparks, and debris.
- Hand and arm protection: Use heat-resistant gloves and arm sleeves to protect against burns and heat radiation.
- Foot protection: Wear safety boots with heat-resistant soles and toe protection.
- Respiratory protection: Use respiratory protection, such as a properly fitted mask or respirator, if there is a risk of inhaling fumes or gases.
Fire Safety:
Implement fire safety measures to prevent and manage fires:
- Keep a fire extinguisher nearby and ensure it is appropriate for use on flammable metals.
- Clear the work area of flammable materials, including fuels, solvents, and combustible debris.
- Have a fire watch person present during and after cutting operations to monitor for any potential fire hazards.
Cylinder Safety:
Handle oxygen and fuel gas cylinders with care:
- Secure cylinders in an upright position, using appropriate cylinder restraints or chains.
- Store cylinders in a well-ventilated area, away from heat sources, open flames, and combustible materials.
- Ensure cylinders are regularly inspected, maintained, and within their designated service life.
Proper Connections and Hoses:
Check for leaks and ensure proper connections between regulators, hoses, and the cutting torch. Inspect hoses regularly for wear, cracks, or damage, and replace them if necessary.
Flashback Prevention:
Install flashback arrestors on the oxygen and fuel gas lines to prevent flashbacks of the flame into the hoses or cylinders. Ensure they are in good working condition and regularly inspected.
Safe Work Practices:
Adhere to safe work practices during oxygen cutting:
- Conduct a risk assessment before starting work and identify potential hazards.
- Follow manufacturer guidelines and recommended operating procedures for the specific equipment being used.
- Maintain a safe distance from the cutting operation and ensure others in the vicinity are also at a safe distance.
- Never leave the cutting torch unattended, and shut off the oxygen and fuel gas supply when not in use.
Oxygen Cutting vs Plasma Cutting
Here’s a tabular comparison highlighting the major differences between oxygen cutting and plasma cutting:
Parameter | Oxygen Cutting | Plasma Cutting |
---|---|---|
Heat Source | Combustion of oxygen and fuel gas | Electrically generated plasma arc |
Cutting Speed | Slower compared to plasma cutting | Faster compared to oxygen cutting |
Cutting Thickness | Primarily used for thick carbon steels | Versatile for various thicknesses and materials |
Cutting Precision | Moderate precision and rougher cut edges | High precision and cleaner cut edges |
Kerf Width | Wider kerf width | Narrow kerf width |
Metal Suitability | Mainly used for carbon steels and some alloys | Suitable for a wide range of metals and alloys |
Initial Investment | Lower initial equipment cost | Higher initial equipment cost |
Operating Cost | Higher operating costs due to electricity usage | Higher operating costs due to electricity usage |
Cleanliness | Produces slag and requires post-cut cleaning | Minimal slag and reduced post-cut cleaning |
Portability | More portable and can be used in remote areas | Requires power source and less portable |
Environmental Impact | May produce fumes, smoke, and airborne pollutants | Minimal fumes and environmental impact |