In the sprawling landscapes of oil-rich regions, towering structures known as oil derricks stand as testaments to human ingenuity and resource extraction. These iconic structures play a pivotal role in the process of extracting crude oil from beneath the Earth’s surface. Beyond their functional significance, oil derricks are engineering marvels that have evolved over time to increase efficiency, safety, and environmental responsibility in the oil drilling process. Join us as we explore the fascinating world of oil derricks and uncover the intricate workings behind these towering giants.
What are Oil Derricks?
Oil derricks are the load-bearing towering structures that symbolize the age-old pursuit of fueling the world’s energy demands. They are permanent structures used to support and position a drill string over an oil well. Mainly found in offshore drilling applications, Oil derricks extend like a tall tower above the drilling operations.
History and Evolution of Oil Derricks
The history of oil derricks dates back to the late 19th century when the demand for petroleum products began to soar. The oil derricks as we know is named after a hangman ‘Thomas Derrick’ due to its resemblance to gallows.
Early oil drilling methods were rudimentary and often involved manual labor and basic tools. However, as the need for increased production and efficiency grew, so did the need for advanced drilling technologies.
The iconic wooden derricks that characterized early oil drilling operations were eventually replaced by more robust steel structures. These new designs allowed for greater height, stability, and the incorporation of mechanized equipment. The evolution of oil derricks was marked by innovations like the introduction of rotary drilling and hydraulic systems, all of which revolutionized the industry.
The early 20th century saw significant changes in the design of oil derricks due to technical advancements and changing industry requirements. Motorized drilling became standard, delivering more power and speed than the manual method. As well, steam power was replaced by internal combustion engines and electric motors. By the mid-20th century, oil derricks were equipped with rotary systems that allowed rotary drilling, facilitating faster and more efficient drilling. Furthermore, the evolution of horizontal drilling and hydraulic fracturing technologies in the late 20th century greatly enhanced the capacity of these structures.
Components of Oil Derricks
Oil derricks are composed of several key components that work in tandem to extract oil from deep within the Earth’s crust. Here are the main components of a typical oil derrick:
- Mast or Derrick Structure: This towering framework supports various equipment and provides stability during drilling operations.
- Crown Block: Located at the top of the mast, the crown block guides the drilling line and supports the weight of the drill string and other equipment.
- Drilling Line: A heavy-duty steel cable that supports the drill string and aids in lowering and raising equipment.
- Drawworks: The drawworks consist of a powerful winch that controls the movement of the drilling line, allowing for a controlled descent and an ascent of the drill string.
- Rotary Table: Situated on the derrick floor, the rotary table facilitates the rotation of the drill string and bit, which are essential for drilling through rock formations.
- Drill Bit: The drill bit is the tool at the end of the drill string that breaks through rock and other formations to access the oil reservoirs.
- Derrick Floor: This is the elevated platform where drilling operations are coordinated and equipment is positioned.
Fig. 1 shows a typical schematic of Oil Derrick.
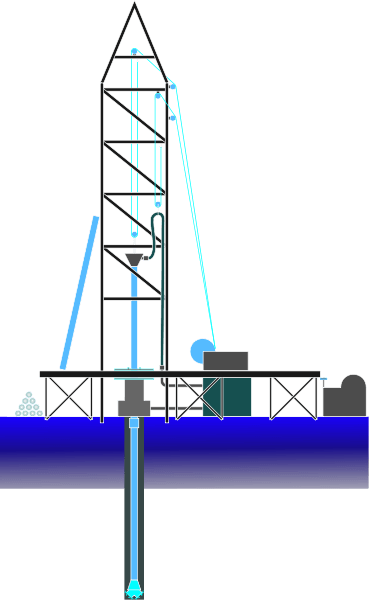
Types of Oil Derricks
Types of oil derricks can be broadly categorized into two main categories: fixed (land-based) derricks and floating (offshore) derricks. Land-based derricks are anchored to the ground and are often used in onshore drilling operations. Floating derricks, on the other hand, are used in offshore drilling and are located on floating platforms known as drilling rigs.
Land-Based Derricks:
Conventional Land Rigs: These are fixed structures anchored to the ground and are commonly used for drilling onshore, where the drilling rig remains stationary throughout the operation. They can range from relatively small, portable rigs to large, permanent installations.
Mobile Land Rigs: Mobile land rigs are designed for quick setup and mobility. They are often used in remote or temporary drilling locations where it’s impractical to establish a permanent drilling platform. Mobile rigs can be transported to the site and assembled relatively quickly.
Cluster Drilling Rigs: Cluster rigs are a variation of conventional land rigs, where multiple drilling rigs are positioned closely together on a single pad. This setup is efficient for drilling multiple wells from a single location.
Offshore Derricks:
Fixed Platform Rigs: These rigs are situated on fixed offshore platforms anchored to the seabed. Fixed platform rigs are used in shallow to moderately deep waters, and they provide a stable drilling environment. They are common in regions like the Gulf of Mexico.
Jack-Up Rigs: Jack-up rigs are mobile drilling platforms equipped with legs that can be extended to lift the rig above the water’s surface. They are used in waters of varying depths and are towed to the drilling site. Once on location, the legs are lowered to the seabed to create a stable platform for drilling.
Semi-Submersible Rigs: Semi-submersible rigs are large, floating structures that can be partially submerged by filling ballast tanks with water. This allows them to remain stable even in rough seas. They are used in deepwater drilling operations.
Drillships: Drillships are self-propelled vessels with drilling equipment onboard. They can operate in ultra-deep waters and are highly mobile, making them suitable for exploratory drilling in remote locations.
Tender-Assisted Rigs: These rigs are used in locations where a fixed platform is not feasible. A tender barge is used to support the drilling operations, and it provides accommodation, supplies, and other services to the rig.
Submersible Rigs: Submersible rigs are designed to be towed to the drilling site and then submerged underwater, allowing them to operate in extreme water depths. They are less common than other offshore rig types.
Specialized Rigs:
Arctic Rigs: Designed to withstand harsh Arctic conditions, these rigs have reinforced structures and systems to operate in freezing temperatures and icy waters.
Helicopter Portable Rigs: These compact rigs are designed to be easily transported by helicopter to remote drilling locations, particularly in rugged or inaccessible terrain.
Coiled Tubing Rigs: These rigs are used for specialized drilling and well intervention techniques, such as coiled tubing operations, which involve pumping fluid or tools down a continuous tubing string into the well.
How do Oil Derricks Work?
Oil derricks, also known as drilling rigs or oil rigs, are complex structures designed to extract crude oil and natural gas from deep beneath the Earth’s surface. They work through a series of carefully coordinated steps and components. Here’s a simplified overview of how oil derricks work:
- Location and Setup:
- Oil derricks are typically set up in areas where geological surveys suggest the presence of oil or natural gas reserves. These locations can be on land or offshore, depending on the drilling operation.
- Drilling Preparation:
- Before drilling begins, the drilling crew conducts preliminary site preparations. This includes clearing the area, leveling the ground, and setting up safety measures.
- Drill Bit and Drill String Assembly:
- The drill bit, a specialized cutting tool, is attached to the end of a long, thick cable called the drill string. The drill string is composed of interconnected drill pipes that transmit torque and axial force to the drill bit.
- Derrick and Crown Block:
- The derrick, a tall steel structure, is the central component of the oil rig. It provides the necessary height and support for the drilling equipment. At the top of the derrick is the crown block, which guides the drilling line and supports the weight of the drill string.
- Rotary Table and Drawworks:
- The rotary table, located on the derrick floor, is a large rotating platform. It facilitates the rotation of the drill string and bit. The draw works a powerful winch, and controls the movement of the drilling line, allowing for controlled lowering and raising of the drill string.
- Drilling Fluid (Mud):
- Drilling fluid, often referred to as “mud,” is pumped into the wellbore through the drill string. Mud serves multiple purposes, including cooling the drill bit, carrying rock cuttings to the surface, and preventing blowouts by exerting pressure on the wellbore.
- Drilling Operation:
- As the drill bit rotates, it penetrates through layers of rock and sediment. The weight of the drill string provides the downward force needed to break through the Earth’s crust. The drilling crew continuously monitors and adjusts the drilling parameters based on real-time data from sensors and geophysical measurements.
- Coring and Logging:
- At various depths, the drilling crew may extract core samples and use specialized instruments to log geological information. This data helps geologists and engineers assess the composition of the subsurface and make informed decisions about the drilling process.
- Casing and Cementing:
- As the well progresses, steel casing pipes are inserted and cemented in place to secure the wellbore and prevent contamination of underground water sources. This process reinforces the integrity of the well.
- Completion and Production:
- Once the drilling reaches the desired depth and the well is secured, it may undergo completion processes, such as perforation and hydraulic fracturing (fracking), to enhance oil and gas production. Production tubing and wellhead equipment are installed to bring the oil and gas to the surface.
- Transport and Refining:
- Extracted crude oil and natural gas are transported via pipelines or tankers to refineries for processing into various petroleum products, including gasoline, diesel fuel, and petrochemicals.
- Maintenance and Monitoring:
- Oil derricks require regular maintenance to ensure safe and efficient operation. Advanced monitoring systems continuously track well conditions, allowing for early detection of potential issues.
Design and Structure of Oil Derricks
The Structure and Design of Oil Derricks
Oil derricks are specialized rigs designed with the sole purpose of drilling oil wells. They stand as the pivotal point of extraction operations, with their towering stature often commanding attention in the landscape. The complexity of these rigs is no accident. Each one is meticulously designed and constructed to pierce deep below the earth’s surface to reach the underground reservoirs where oil and other hydrocarbons sit.
Foundational Elements of Oil Derricks
The foundation of an oil derrick plays a crucial role in its overall stability. It’s usually composed of concrete and steel, laid deep in the ground to provide steady support to the above structures. The base must resist not only gravitational forces from the derrick’s weight but also potential forces from lateral movement, wind, and seismic activity. The specific design of the foundation varies widely depending on the ground condition and the particular requirements of the drill site.
Derrick’s Support Framework
The support framework forms the main body of an oil derrick. This above-ground structure is most typically a four-legged, square pyramidal tower constructed from high-strength steel. The steel trusses are designed to bear the load of the heavy drill string and casing pipes that lengthen as the well digs deeper. The taller the derrick, the deeper it can drill, with some towering structures reaching up to 50 meters tall.
The Drill Floor
At the heart of the oil derrick structure is the drill floor which houses all the primary drilling equipment. This includes the drill string, the big rotary table, and the blowout preventer (BOP), a device that stops the flow of oil in case of overpressure. Here, workers connect and disconnect the pieces of the drill pipe, inserting them into the ground one by one as the drill digs deeper.
Mast and Drawworks System
Above the drill floor are the derrick’s mast and a winch system known as the draw works. This assembly is responsible for raising and lowering the drill string into and out of the borehole. The mast itself is a large, durable structure that supports the weight of the drill string and other heavy drilling equipment.
Crown Block and Derrick Man Stand
Something else of note on an oil derrick is the crown block and the Derrick Man stand. The crown block is located at the very top of the derrick, and it houses a complex system of pulleys through which the drill line runs. Below the crown block, there is a small platform known as the Derrick Man stand. This is where a specialized operator, known as the Derrick Man, operates control levers and monitors drilling operations.
Designing for Efficiency and Safety
Also, of utmost importance in the design and structure of oil derricks is the prioritization of efficiency and safety. Safety measures, ranging from escape routes, and fire suppression systems, to safety harness attachment points, are woven into the design of every piece of the derrick. Modern designs also incorporate elements that improve the efficiency of oil extraction, such as automation and remote monitoring technologies.
An oil derrick is a large, towering structure made primarily of hardy steel. Its purpose? To delve deep into the Earth’s crust, seeking out and tapping into the rich reservoirs of oil that lie beneath. Every aspect of the oil derrick, from its formidable structure to the high-tech adoptions on its drill floor, is meticulously designed, demonstrating a blend of impressive engineering and practical need. It’s fair to say that oil derricks play a crucial role in the production and supply of energy worldwide.
The Functioning of Oil Derricks
Exploring the Significance of Oil Derricks in Oil Drilling Operations
Oil derricks play an indispensable role in the exploration and extraction of oil and gas. They are often depicted as towering structures amidst drilling sites, responsible for stabilizing the uppermost portion of the drilling mechanism. The term “oil derrick” is sometimes used colloquially to describe the whole drilling rig, which encompasses not just the derrick, but a complex system of machinery and equipment vital to drilling operations. The core function of an oil derrick extends to facilitating drilling and handling of the pipe or drill stem, thereby enabling access to the rich oil deposits hidden deep beneath the surface.
Understanding the Drilling Process
The initial stage of drilling involves sinking a steel casing into the ground and cementing it in place. After setting the casing, a drill bit—attached to a string of drill pipes—is lowered into the well to bore through the earth. Drilling mud is pumped down the drill pipes and exits through nozzles in the drill bit. This cools the bit, lubricates the drilling process, carries off the cuttings, and maintains pressure at the bottom of the well to prevent the intrusion of water, oil, or gas.
The drilling continues, with the drill bit cutting deeper into the earth. Periodically, the drill bit is withdrawn, a new section of casing is added, and the drill bit is returned to continue the drilling process. This method is known as “rotary drilling”.
Drilling Techniques and Machinery Involved
Oil derricks employ a variety of drilling methods. Apart from rotary drilling, “directional drilling” has become increasingly utilized in recent years. This method allows drills to create wells at different angles, not just vertically, maximizing the exposure to the oil-bearing formations.
The machinery and equipment involved at a drilling site are not limited to the oil derrick and drill bit. There are also mud pumps to circulate drilling fluids, draw works to control the movement of the drill string, blowout preventers for preventing uncontrolled releases of oil or gas (“blowouts”), and shale shakers for separating the cuttings from the drilling fluids.
Safety Measures in Oil Derrick Operations
Given the potential hazards of drilling, stringent safety measures are taken to ensure safety and prevent environmental contamination. Blowout preventers are used as last-resort safety devices to seal off the well if pressure control systems fail.
Personnel are also trained in safety procedures and emergency response tactics. Further, flame and gas detection systems are implemented, along with regular inspections and preventive maintenance of all equipment and machinery.
After the drilling operation, the well is capped or “completed” to allow the controlled extraction of oil. Pumps, valves, and lines are installed to enable the safe flow of oil to the surface for processing and distribution. Throughout the process, the well’s pressure and output are closely monitored to prevent blowouts or leaks.
Understanding the Role of Oil Derricks in Processing Crude Oil
Oil derricks are a critical player in processing crude oil. Extraction is just the beginning of a lengthy process to transform crude oil into consumable items. Initially, the crude oil is separated from water and residual particles right after extraction at the drilling site. Following this, the oil is usually transported via pipelines for further refinement. During distillation, a process involving heating the crude oil and separating it into various components based on their boiling points, the oil is converted into usable products.
In every step of this complicated process, from the initial drilling to the subsequent processing, specialized technicians and engineers alongside high-tech apparatus are required. Therefore, the smooth functionality of oil derricks is crucial. They serve as the central operational unit, responsible for delivering our oil and energy requirements.
Environmental Impact of Oil Derricks
However, much like other industrial procedures, oil derricks have a considerable environmental impact. Prominent among the reasons are emissions from drilling activities. A lot of machinery and technology involved in the oil extraction process relies on burning fossil fuels, emitting greenhouse gases such as carbon dioxide in the process. For example, potent drilling equipment often depends on diesel, increasing the level of air pollution.
Another prominent environmental concern with oil derricks relates to oil spills, a serious ecological hazard. Such spills can happen throughout various stages of oil extraction, from drilling to transportation. These spills inflict profound harm on both marine and terrestrial ecosystems, killing wildlife, contaminating soil and groundwater, and inflicting long-term environmental damage. The 2010 Deepwater Horizon oil spill, which led to a discharge of approximately 4.9 million barrels of oil into the Gulf of Mexico, serves as a potent reminder of such potential hazards.
Apart from the threat of oil spills, the physical presence of oil derricks leading to the decimation of habitats is another significant ecological concern. These towering structures often disrupt land and sea ecosystems, interfering with animal movements and causing a negative impact on biodiversity. Noise pollution originating from oil derricks further disturbs animal communication and behavior patterns.
Economic Impact of Oil Derricks
Despite the environmental concerns, oil derricks play a critical role in an economic context. One of the tangible benefits is job creation. The oil and gas industry supports millions of jobs worldwide, from those directly involved in drilling operations to indirect roles in fields like transport, equipment manufacturing, and administration. In the United States, the petroleum industry alone supports approximately 10.3 million jobs, as reported by the American Petroleum Institute.
Oil derricks contribute significantly to the global energy supply, playing an essential role in supporting modern lifestyles and industrial activities. Much of the world’s transportation system and power generation infrastructure largely depend on petroleum products, so a robust oil industry is fundamental for maintaining energy security.
The influence of oil derricks extends to global commodity markets as well. Oil is one of the world’s most heavily traded commodities, and oil prices have a profound impact on those markets. Shifts in oil prices can affect everything from the cost of manufactured goods to transportation prices to the cost of food. Therefore, the oil industry – and by extension, oil derricks – wield significant influence over global economic conditions.
As we wheel each facet of oil derricks – the history, structure, functioning, and impacts, one cannot help but marvel at their embodiment of the human quest for energy. These towering edifices not only represent a significant era of industrial advancement, but they also stand as potent symbols of the environmental and economic balances we strike in our ongoing energy pursuit. Acknowledging oil derricks’ relevance helps us comprehend the broader narrative of our energy story – one steeped in innovation, economic improvement, but also environmental challenges. This exploration provides a foundational insight into our intricate relationship with these colossal structures, contextualizing not just their past, but also their significance to the future of our energy landscape.