A Material Test Report (MTR) is a document that provides information on the physical and chemical properties of a material. The report is typically generated by the manufacturer or supplier of the material and provides information on the material’s composition, mechanical properties, heat treatment, and other important information.
Purpose of a Material Test Report
The purpose of the MTR is to ensure that the material meets the required specifications and standards for a particular application. The report provides assurance to the purchaser that the material is of the specified quality and is suitable for use in the intended application.
Typically, an MTR will include the following information:
- Material identification and description
- Chemical composition and analysis
- Mechanical properties (such as tensile strength, yield strength, and elongation)
- Heat treatment information
- Dimensional measurements and tolerances
- Non-destructive testing results (if applicable)
- Any additional testing or inspection results
MTRs are commonly used in industries such as manufacturing, construction, and engineering, where the quality and reliability of materials are critical to the success of a project.
Reading a Material Test report
Reading a Material Test Report (MTR) can seem overwhelming at first, but breaking it down into individual sections can make it easier to understand. Here’s a general guide on how to read an MTR:
Material Identification
This section provides information on the material’s identity, including its name, grade, material dimension, product form, and product specifications metallurgy. Make sure the information matches the material you ordered. The product specifications metallurgy section refers to the ASTM or ASME standards applicable to the material that usually outline the specific requirements for the material’s composition, properties, and dimensions, and they vary depending on the application.
Material Heat Number / Heat Code
The material heat number or Material heat code is a unique identifier assigned to a specific batch of material during the manufacturing process. This number is useful for tracking the material’s origin, processing, and any testing performed on it.
The heat number is a very essential component of a material test report because it allows for the traceability of the material. By comparing the heat number on the MTR with the corresponding heat number on the material and accompanying paperwork, the material’s identity and history can be verified. This is needed to ensure that the material meets the required specifications and is suitable for its intended use.
Chemical Analysis
This section lists the chemical composition of the material, including the elements present and their percentages. Check that the values fall within the specified range for the material grade. The chemical composition of a material is critical as it can affect the material’s physical properties, performance, and suitability for specific applications.
Mechanical Properties
This section provides information on the material’s mechanical properties, such as tensile strength, yield strength, hardness, impact strength, fatigue strength, and elongation. Compare these values to the specified requirements for your application. These properties are essential to understand when selecting materials for specific applications to ensure that the material can withstand the required loads and stresses.
Heat Treatment
This section lists the details of any heat treatment the material has undergone, such as annealing, quenching, or tempering. This may also include details on the temperature range, duration, and cooling method used in the process. Check that the heat treatment process matches the specified requirements.
Dimensional Measurements
This section provides information on the material’s dimensions and tolerances. Verify that the measurements fall within the specified range for your application.
Non-Destructive Testing
If applicable, this section lists the results of any non-destructive testing, such as ultrasonic testing or magnetic particle inspection. Review the results to ensure that the material meets the specified requirements.
Additional Testing or Inspection
This section lists any additional testing or inspection performed on the material, such as corrosion testing or impact testing. Review the results to ensure that the material meets the specified requirements.
Certified Mill Signature
The Certified Mill Signature is a signature provided by the responsible employee for preparing the report. This signature certifies that the information included in the Material Test Report (MTR) is genuine, accurate, and has been verified by the mill’s quality control team.
The Certified Mill Signature serves as a declaration of the quality of the material and the accuracy of the information provided in the MTR. It is an essential component of the MTR, providing assurance that the material has been manufactured to the required standards and specifications.
In general, the signature includes the name and title of the responsible employee, along with the date and time of the signature. The signature is usually accompanied by a stamp or seal from the source mill to further authenticate the report.
Overall, it’s important to compare the values listed in the MTR to the specified requirements for your application. If you have any questions or concerns about the MTR, reach out to the manufacturer or supplier for clarification. Fig. 1 Below shows a typical example of a material test report:
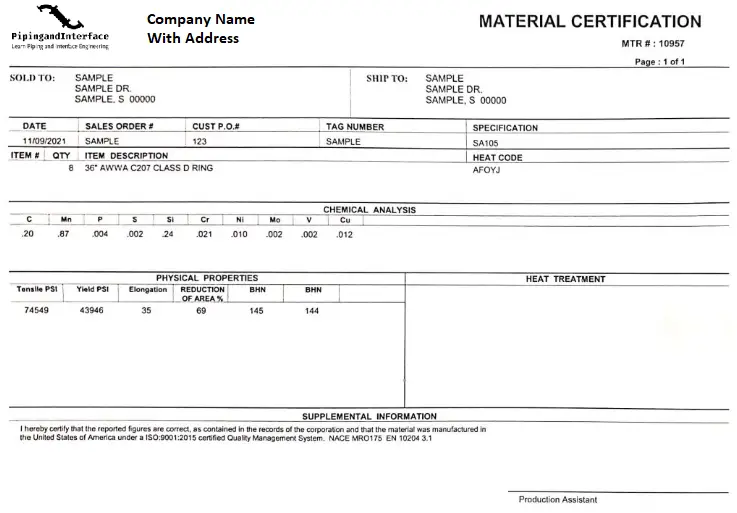
Types of Material Test Report
There are several types of Material Test Reports (MTRs) used in different industries and applications. Some common types of MTRs are:
- Mill Test Report (MTR): This is the most common type of MTR used in the manufacturing industry. It is generated by the manufacturer of the material and provides information on the physical and chemical properties of the material.
- Heat Number Traceability Report: This report provides a record of the material’s production history, including the raw material used, the heat treatment process, and any inspections performed during the production process. This report is commonly used in the oil and gas industry.
- Inspection Test Plan (ITP): This report outlines the testing and inspection procedures that will be performed on the material during production. It includes a checklist of the tests to be performed and the required specifications.
- Material Certification: This report certifies that the material has been tested and meets the specified requirements. It is typically issued by a third-party testing laboratory and is commonly used in the construction industry.
- Material Test Certificate (MTC): This is a generic term used to refer to any type of MTR that provides information on the material’s properties and composition. It may include any or all of the information listed above.
The type of MTR required will depend on the industry and application. It’s important to verify that the MTR provided meets the specified requirements for your application.
Codes and Standards for Material Test Reports
There are several codes and standards that provide guidelines for preparing Material Test Reports (MTRs). Some of the most common ones include:
- ASTM E29: Standard Practice for Using Significant Digits in Test Data to Determine Conformance with Specifications – This standard provides guidelines on how to round and report numerical values in MTRs to ensure accuracy and consistency.
- ASME Section II, Part A: Ferrous Material Specifications – This code provides specifications for various types of ferrous materials used in pressure vessels, boilers, and other applications. It also provides guidelines on how to prepare MTRs for these materials.
- ASME Section II, Part B: Nonferrous Material Specifications – This code provides specifications for various types of nonferrous materials used in pressure vessels, boilers, and other applications. It also provides guidelines on how to prepare MTRs for these materials.
- API Specification Q1: Specification for Quality Management System Requirements for Manufacturing Organizations for the Petroleum and Natural Gas Industry – This specification provides guidelines for quality management systems used in the oil and gas industry, including requirements for MTRs.
- ISO 10474: Steel and Steel Products – Inspection Documents – This standard provides guidelines for the preparation of inspection documents, including MTRs, for steel and steel products.
It’s important to verify which codes and standards apply to your specific industry and application and to ensure that MTRs are prepared in accordance with these guidelines.
Material Test Report Requirements
The requirements for Material Test Reports (MTRs) can vary depending on the industry and application. However, some common requirements include:
- Accurate and Complete Information: The MTR should include accurate and complete information on the material’s physical and chemical properties, including its composition, mechanical properties, heat treatment, dimensional measurements, and any testing or inspection results.
- Traceability: The MTR should provide traceability information, such as the heat number, to allow the material to be traced back to its source and production history.
- Compliance with Specifications: The material should be tested in accordance with the specified requirements for the industry and application, and the MTR should demonstrate compliance with these specifications.
- Third-Party Verification: In some industries, such as the construction industry, MTRs may need to be verified by a third-party testing laboratory to ensure that the material meets the specified requirements.
- Consistency: The MTR should be prepared consistently for each batch or lot of material to ensure that the information provided is reliable and accurate.
- Retention: The MTR should be retained for a specified period of time, typically several years, to allow for future reference and verification.
It’s important to verify the specific requirements for MTRs in your industry and application to ensure that the material meets the specified requirements and is suitable for the intended use.
Material Test Report Format
Material Test Reports (MTRs) can vary in format depending on the industry, application, and requirements. However, some common elements that may be included in the format of an MTR are:
- Heading: The MTR should have a heading that clearly identifies it as a Material Test Report and includes information such as the material type, lot number, and heat number.
- Material Specifications: The MTR should provide information on the material’s specifications, including the applicable standards, grade, and composition.
- Mechanical Properties: The MTR should include the material’s mechanical properties, such as tensile strength, yield strength, and elongation.
- Chemical Analysis: The MTR should include the results of the material’s chemical analysis, including the composition of the material and any impurities or trace elements.
- Heat Treatment: If the material has been heat-treated, the MTR should include information on the heat treatment process and the resulting properties.
- Test Results: The MTR should include the results of any testing or inspection performed on the material, including dimensional measurements, non-destructive testing, and any other tests required by the industry or application.
- Traceability: The MTR should provide traceability information, such as the heat number, to allow the material to be traced back to its source and production history.
- Certification: The MTR should include a certification statement indicating that the material meets the specified requirements for the industry and application.
The specific format of an MTR can vary, but it’s important to ensure that the information provided is accurate, complete, and meets the specified requirements for your industry and application.
Difference between Material Test Report and Material Test Certificate
Material Test Reports (MTRs) and Material Test Certificates (MTCs) are both documents that provide information about the material’s properties and testing. However, there are some differences between the two:
- Scope: Material Test Reports typically provide detailed information about the material’s properties and testing, while Material Test Certificates provide a summary of this information.
- Format: Material Test Reports can vary in format depending on the industry and application, while Material Test Certificates typically have a standardized format that is used across the industry.
- Third-Party Verification: Material Test Certificates are often verified by a third-party testing laboratory to ensure that the material meets the specified requirements, while Material Test Reports may or may not be verified in this way.
- Compliance: Material Test Certificates typically provide certification that the material meets the specified requirements for the industry and application, while Material Test Reports may or may not include this certification.
- Use: Material Test Certificates are often required in industries such as construction and manufacturing, while Material Test Reports may be used in a wider range of industries and applications.
Material Test Report vs Mill Test Report
Material Test Reports (MTRs) and Mill Test Reports (MTRs) are both documents that provide information about the material’s properties and testing. However, there are some differences between the two:
- Scope: Material Test Reports typically provide detailed information about the material’s properties and testing, while Mill Test Reports providing information on the production process of the material.
- Content: Material Test Reports focus on the testing and inspection of the material after production, while Mill Test Reports providing information on the material’s production process, including the source of the raw materials, the manufacturing process, and any heat treatment or processing that was done.
- Format: Material Test Reports can vary in format depending on the industry and application, while Mill Test Reports typically have a standardized format that is used across the industry.
- Traceability: Both Material Test Reports and Mill Test Reports provide traceability information, such as the heat number, to allow the material to be traced back to its source and production history.
- Use: Material Test Reports may be used in a wider range of industries and applications, while Mill Test Reports are typically required in industries such as construction and manufacturing, where traceability and quality control are critical.
The material test report (MTR) is an important document that provides essential information about the quality and composition of a particular material. It is usually prepared and provided by a manufacturer or supplier of materials.