Fluid systems play a vital role in countless industries, from manufacturing and agriculture to healthcare and automotive. These systems rely on a network of components to transport liquids or gases efficiently and safely. While valves, pumps, and pipes often steal the spotlight, one unsung hero quietly facilitates the flow of fluids – the barbed fitting.
What is a Barbed Fitting?
A barbed fitting is a simple yet ingenious device designed to connect flexible tubing or hoses to other components within a fluid system, such as valves, pumps, or tanks. They are called “barbed” fittings because of their characteristic barbed or ribbed exterior, which provides a secure grip on the tubing. The basic design of a barbed fitting consists of a tubular body with ridges or barbs along its length, a threaded or smooth end for attachment, and a means of tightening or securing the connection, often a nut or clamp. As they are frequently connected to hose or flexible tubing connections they are also popularly known as Hose Barb Fittings.
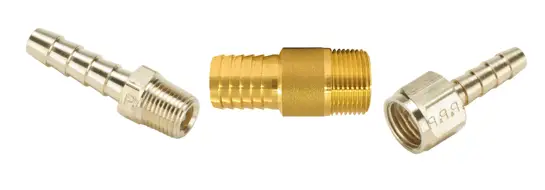
Hose barb fittings are available in many shapes and sizes. The gripping and sealing ability of
hose barbs depend on the following factors:
- The slope and depth of the barb,
- The sharpness of the gripping edge,
- The number of barbs, and
- The spacing of barbs
Why Barbed Fittings Matter?
The main features of barbed fittings are
Versatility:
Barbed fittings are incredibly versatile. They can accommodate a wide range of tubing materials, including plastic, rubber, and even metal, making them suitable for various applications.
Ease of Installation:
Unlike some complex fluid connectors, barbed fittings are easy to install. The barbs grip the tubing securely, eliminating the need for adhesives or specialized tools in most cases. This simplifies assembly, reduces labor costs, and minimizes the risk of leaks.
Cost-Effective:
Barbed fittings are cost-effective, both in terms of initial purchase and long-term maintenance. Their simplicity makes them affordable, and their reliability minimizes the need for frequent replacements or repairs.
Resilience:
These fittings are built to withstand the rigors of their intended applications. Whether in a high-pressure hydraulic system or a low-pressure irrigation setup, barbed fittings provide a dependable connection.
Leak Prevention:
The barbed design ensures a tight and leak-resistant connection, crucial in applications where fluid loss or contamination could have serious consequences.
Wide Range of Sizes and Styles:
Barbed fittings come in a variety of sizes and styles to suit different needs. Whether you’re connecting two tubes, transitioning from one diameter to another, or splitting a line into multiple branches, there’s likely a barbed fitting designed for your specific requirements.
Common Applications of Barbed Fittings
Barbed fittings find applications in numerous industries and settings:
- Automotive: In vehicles, they connect hoses for fuel, coolant, and brake fluid.
- Agriculture: Barbed fittings are used in irrigation systems to transport water to fields efficiently.
- Medical: They play a role in medical equipment, such as oxygen delivery systems.
- Industrial: Barbed fittings are found in hydraulic systems, pneumatic systems, and chemical processing plants.
- Home and Garden: From water filters to aquariums, barbed fittings are present in various household and recreational applications.
- Chemical and Pharmaceutical: In laboratories and manufacturing plants, these fittings are used to transport various chemicals and fluids safely.
Types of Barbed Fittings
Barbed fittings come in various shapes and sizes, each designed for specific applications and requirements within fluid systems. These fittings, with their ribbed exteriors that grip onto hoses or tubing, offer secure connections without the need for soldering, welding, or adhesives. Here are some common types of barbed fittings:
Straight Barbed Fittings:
Straight barbed fittings have a simple, straight design, making them suitable for connecting two hoses or tubing pieces end-to-end. These fittings are versatile and find use in a wide range of industries, including automotive, plumbing, and agriculture.
Elbow Barbed Fittings:
Elbow barbed fittings have a 90-degree or 45-degree bend, allowing for changes in direction while maintaining the hose or tubing’s flow. Elbow barbed fittings are commonly used in applications where space constraints or hose routing necessitate bends, such as in irrigation systems or machinery.
Tee Barbed Fittings:
Tee barbed fittings have three openings, allowing one hose or tube to split into two branches or merge two flows into one. These fittings are handy for creating multiple connections from a single line, often seen in plumbing, automotive, and chemical transfer systems.
Y-Barbed Fittings:
Y-barbed fittings are similar to tee fittings but have a Y-shaped configuration, providing a symmetrical split in the hose or tubing. Y-barbed fittings are used when equal distribution of fluid flow is necessary, such as in irrigation systems or laboratory setups.
Reducer Barbed Fittings:
Reducer barbed fittings have different-sized openings on each end, allowing for the transition from a larger diameter hose or tubing to a smaller one. These fittings are essential when adapting hoses or tubes of varying sizes, commonly used in plumbing and automotive systems.
Bulkhead Barbed Fittings:
Bulkhead barbed fittings are designed to pass through walls, panels, or containers. They have barbed ends on both sides of the barrier. Bulkhead barbed fittings are found in applications where hoses or tubing need to pass through walls or enclosures, such as in tanks, reservoirs, or equipment.
Threaded Barbed Fittings:
Threaded barbed fittings have one end with external threads that can be screwed into a corresponding threaded port, providing a secure connection. These fittings are commonly used in plumbing and hydraulic systems to create a threaded connection with hoses or tubing.
Push-to-Connect Barbed Fittings:
Push-to-connect barbed fittings are designed for quick and easy assembly. They allow hoses or tubing to be pushed onto the barbs without the need for clamps or other securing methods. These fittings are popular in pneumatic and low-pressure hydraulic systems, offering rapid installation and disassembly.
Camlock Barbed Fittings:
Camlock barbed fittings feature a camlock coupling mechanism for fast and secure connections. They are often used in industrial applications for quick hose changes. Camlock barbed fittings are prevalent in industries such as agriculture, construction, and chemical processing.
Barbed Fitting Materials
Barbed fittings are essential components in fluid systems, providing secure connections for hoses or tubing in a wide range of industries and applications. To ensure the proper functioning and longevity of a fluid system, it’s crucial to choose the right barbed fitting material. Different materials offer varying levels of durability, corrosion resistance, and compatibility with specific fluids. In this article, we’ll explore some common barbed fitting materials and their respective advantages and applications.
Brass Barb Fittings:
- Advantages:
- Brass is corrosion-resistant, making it suitable for water and non-corrosive fluid applications.
- It has good thermal conductivity, making it useful in applications where temperature control is essential.
- Brass barbed fittings are known for their strength and durability.
- Applications:
- Plumbing and water distribution systems.
- Compressed air systems.
- Hydraulic systems with non-corrosive fluids.
Stainless Steel Barb Fittings:
- Advantages:
- Stainless steel is highly resistant to corrosion, making it suitable for a wide range of fluids, including aggressive chemicals.
- It offers excellent strength and durability.
- Stainless steel is easy to clean and maintain, making it suitable for sanitary applications.
- Applications:
- Chemical processing industries.
- Food and beverage processing.
- Medical and pharmaceutical applications.
- Marine environments.
Plastic Barb Fittings (Polypropylene, Nylon, PVC):
- Advantages:
- Plastic barbed fittings are lightweight and cost-effective.
- They are resistant to corrosion and suitable for various non-corrosive fluid applications.
- These materials are often used in applications where weight reduction is critical.
- Applications:
- Irrigation systems.
- Aquariums and fish tanks.
- Automotive fluid systems (e.g., windshield washer fluid).
Aluminum Barbed Fittings:
- Advantages:
- Aluminum is lightweight, making it ideal for applications where weight reduction is essential.
- It offers good corrosion resistance.
- Aluminum barbed fittings are often used in aerospace and automotive applications.
- Applications:
- Aircraft and aerospace systems.
- Automotive fluid systems.
- Some industrial and manufacturing settings.
Nickel-Plated Brass Barb Fittings:
- Advantages:
- Nickel-plated brass combines the corrosion resistance of brass with an additional layer of protection from nickel plating.
- It provides enhanced resistance to abrasive and corrosive fluids.
- Applications:
- Pneumatic systems.
- Automotive brake lines.
- Certain chemical processing applications.
Bronze Barb Fittings:
- Advantages:
- Bronze is known for its strength, durability, and resistance to corrosion.
- It is often used in seawater and marine environments due to its resistance to saltwater corrosion.
- Applications:
- Marine applications.
- Saltwater handling systems.
- Certain industrial settings.
Choosing the Right Barbed Fitting
Selecting the appropriate barbed fitting for your application involves considering factors such as material compatibility, size, pressure, and temperature requirements, and the type of tubing being used. The internal diameter of the tube, the flexibility of the tube material, and the intended application are the prominent factors required for selecting the proper barbed fitting for the job.
Choosing the right barbed fitting material depends on several factors:
- Fluid Compatibility: Consider the nature of the fluid being transported. Some materials are more resistant to corrosion and chemical attack than others.
- Environmental Conditions: Evaluate the operating environment, including temperature, humidity, and exposure to chemicals or saltwater.
- Application: Determine the specific requirements of your application, such as pressure ratings, flow rates, and regulatory standards.
- Cost Considerations: Budget constraints may influence your material choice.
- Weight: In some applications, reducing weight may be a priority, favoring materials like aluminum or plastic.
Barbed Fitting vs Quick-Connect Fittings
Here’s a table highlighting the main differences between barbed fittings and quick-connect fittings:
Feature | Barbed Fittings | Quick Connect Fittings |
---|---|---|
Connection Method | Use ribbed or barbed ends to grip hoses or tubing securely. | Employ a push-to-connect mechanism for rapid assembly and disassembly without tools. |
Ease of Installation | Typically require hose clamps or other securing methods to ensure a leak-free connection. | Quick and easy installation without the need for additional tools or clamps. |
Leak Resistance | Effective but may require proper clamping to prevent leaks, especially under high pressure. | Designed for leak-free connections with built-in seals and locking mechanisms. |
Connection Speed | Slower compared to quick connect fittings due to the need for additional securing measures. | Faster connections and disconnections are ideal for applications where speed matters. |
Reusable | Can be reused, but may require re-clamping or additional components for a secure connection after disassembly. | Designed for multiple uses with consistent reliability. |
Applications | Commonly used in a wide range of applications, including plumbing, automotive, and industrial systems. | Widely used in pneumatic, hydraulic, and fluid handling systems, as well as in applications where frequent changes are required. |
Fluid Compatibility | Suitable for various fluids, but material compatibility must be considered for corrosive or aggressive substances. | Compatibility depends on the material and seals used; can be chosen specifically for the type of fluid being transported. |
Variety of Types | Available in various types, such as straight, elbow, tee, and reducer fittings, to accommodate different needs. | Offered in various configurations, including straight, elbow, tee, and more, to suit diverse applications. |
Cost | Generally cost-effective, but the total cost may increase due to the need for clamps and additional securing materials. | May have a higher upfront cost due to the integrated sealing and locking mechanisms but can reduce labor costs. |
While they may not always be in the spotlight, barbed fittings are indispensable components in fluid systems. Their simplicity, versatility, and reliability make them the unsung heroes that keep liquids and gases flowing smoothly across various industries. So, the next time you turn on a faucet, drive a car, or receive medical treatment, remember the humble barbed fitting working quietly behind the scenes to make it all possible.