Vane pumps are a type of positive displacement pump that plays a crucial role in various industrial and hydraulic applications. They are known for their simplicity, efficiency, and reliability. In this comprehensive guide, we will delve deep into the world of vane pumps, covering their design, working principles, types, applications, advantages, disadvantages, maintenance, and more.
1. Introduction to Vane Pumps
What is a Vane Pump?
A vane pump is a type of positive displacement pump that moves fluid by utilizing the back-and-forth movement of vanes or blades within a cylindrical chamber. These pumps are designed to provide a continuous flow of fluid, making them ideal for various applications where a consistent and reliable fluid transfer is required. Vane pumps are known for their simplicity, efficiency, and versatility, which have led to their widespread use in industries such as hydraulics, automotive, aviation, and manufacturing.
Historical Background
The concept of vane pumps dates back to the early 20th century. One of the earliest patents for a vane pump was filed by Charles C. Barnes in 1921. However, it was not until the mid-20th century that vane pumps gained significant popularity in industrial applications. Over the years, advancements in materials, manufacturing processes, and design have improved the performance and reliability of vane pumps, making them a cornerstone of many industries.
2. Design and Components
Vane Pump Anatomy
A typical vane pump consists of several key components, each playing a crucial role in its operation:
1. Rotor:
- The rotor is a central shaft that extends through the pump’s housing. It is connected to a power source, such as an electric motor or an engine, and is responsible for driving the vanes.
2. Vanes:
- The vanes are flat or slightly curved blades made of various materials, including metal, plastic, or composite materials. These vanes are typically inserted into slots in the rotor.
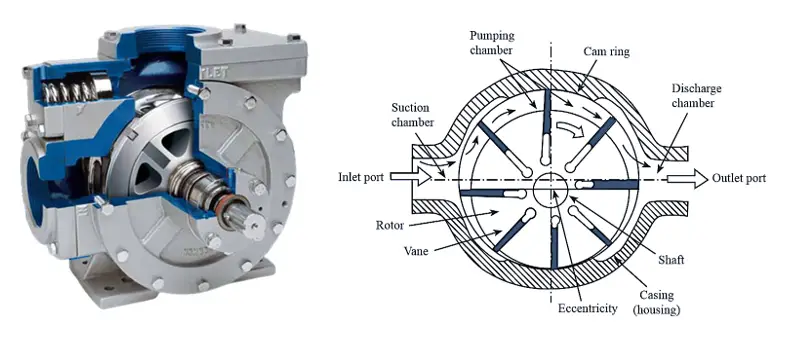
3. Housing:
- The housing, also known as the casing or chamber, is a cylindrical structure that encloses the rotor and vanes. It contains inlet and outlet ports for fluid entry and exit.
4. Inlet and Outlet Ports:
- Inlet and outlet ports are openings on the housing that allow fluid to enter and exit the pump. These ports are equipped with valves or check mechanisms to control the flow of fluid.
5. Cam Ring or Ring Sleeve:
- Some vane pumps feature a cam ring or ring sleeve, which helps maintain contact between the vanes and the housing as the rotor rotates. This design enhances efficiency and reduces wear.
Vane Materials
Vanes can be made from a variety of materials, each with its own advantages and limitations:
- Metal Vanes: Commonly made from materials like steel or aluminum, metal vanes are durable and suitable for handling a wide range of fluids, including those with high viscosity and temperature.
- Plastic Vanes: Plastic vanes are lightweight and corrosion-resistant. They are often used for applications involving chemicals that may corrode metal components.
- Composite Vanes: Composite vanes are a combination of materials, such as carbon fiber or graphite, embedded in a polymer matrix. They offer a balance of strength and corrosion resistance.
Housing and Ports
The housing of a vane pump is typically made of cast iron or aluminum alloy. It is designed to withstand the pressure generated during operation and maintain the integrity of the pump. The housing contains inlet and outlet ports, which are strategically positioned to facilitate the flow of fluid.
Inlet and outlet ports often feature valves or check mechanisms to ensure one-way flow. These valves prevent backflow and maintain the direction of fluid movement, enhancing the pump’s efficiency and performance.
3. Working Principles
Positive Displacement
Vane pumps are classified as positive displacement pumps, meaning they move a fixed amount of fluid with each revolution of the rotor. This characteristic sets them apart from centrifugal pumps, which rely on the imparted kinetic energy to move fluid continuously. The positive displacement nature of vane pumps makes them ideal for applications where precise control of flow and pressure is required.
The Vane Pump Cycle
The operation of a vane pump can be broken down into a series of steps, often referred to as the vane pump cycle:
1. Inlet Phase:
- During the inlet phase, the rotor and vanes rotate. As the rotor turns, the vanes are pushed outward by centrifugal force, creating a volume between the vanes and the housing. This volume increases as the vanes move away from the rotor.
2. Fluid Inlet:
- As the volume between the vanes and the housing increases, fluid is drawn into the pump through the inlet port. The fluid enters the spaces between the vanes.
3. Outlet Phase:
- As the rotor continues to rotate, the vanes are pushed back toward the rotor by a combination of centrifugal force and the shape of the housing (cam ring or ring sleeve). This reduction in volume between the vanes and the housing forces the fluid out of the pump through the outlet port.
4. Fluid Outlet:
- The fluid is expelled from the pump through the outlet port. The continuous rotation of the rotor and the movement of the vanes create a steady flow of fluid.
Inlet and Outlet Phases
The operation of vane pumps relies on the proper timing of the inlet and outlet phases. This timing is crucial for efficient and consistent fluid transfer. The cam ring or ring sleeve, if present, plays a significant role in controlling the movement of the vanes during these phases.
Vane Pump Efficiency
Vane pumps are known for their relatively high efficiency compared to other types of positive displacement pumps. This efficiency is attributed to several factors:
- Minimal Internal Leakage: Vane pumps have low internal leakage due to the close fit between the vanes and the housing. This results in less energy loss and improved overall efficiency.
- Constant Displacement: The positive displacement nature of vane pumps ensures a consistent and predictable flow rate, which is essential in applications requiring precise control.
- Low Noise and Vibration: Vane pumps operate with minimal noise and vibration, reducing wear and tear on components and providing a quieter working environment.
- Ease of Maintenance: The design simplicity of vane pumps makes them relatively easy to maintain and service, contributing to their long-term efficiency.
4. Types of Vane Pumps
Vane pumps come in two main types: fixed displacement and variable displacement pumps.
Fixed Displacement Vane Pumps
Fixed displacement vane pumps, as the name suggests, have a set displacement volume per revolution of the rotor. This means that they provide a constant flow rate, making them suitable for applications where a consistent flow is required. Fixed displacement vane pumps are often used in hydraulic systems, lubrication systems, and other applications where precise control is essential.
Variable Displacement Vane Pumps
Variable displacement vane pumps allow for the adjustment of the displacement volume. This adjustment can be manual or automated, making it possible to vary the flow rate and pressure output as needed. Variable displacement vane pumps are commonly used in mobile hydraulic equipment and applications where adaptability to changing conditions is crucial.
5. Applications
Vane pumps find applications across a wide range of industries due to their versatility and reliability. Here are some key sectors where vane pumps are commonly used:
Hydraulic Systems
Vane pumps are extensively employed in hydraulic systems, including industrial machinery, construction equipment, and manufacturing systems. Their ability to provide precise control over fluid flow and pressure makes them indispensable in these applications.
Automotive Industry
In the automotive industry, vane pumps are utilized in power steering systems, transmission systems, and engine lubrication systems. They play a critical role in ensuring smooth and efficient vehicle operation.
Aviation Industry
Vane pumps are used in aircraft hydraulic systems for functions such as landing gear operation, flap movement, and flight control. Their compact size and reliability are particularly valuable in aviation applications.
Agricultural Machinery
Farm equipment, such as tractors and combine harvesters, often rely on vane pumps for various hydraulic functions, including lifting and steering mechanisms. Vane pumps contribute to the efficiency and productivity of agricultural operations.
Chemical and Process Industries
Vane pumps are suitable for handling a wide range of chemicals and fluids, making them essential in the chemical and process industries. They are used for transferring, mixing, and processing various substances.
Food Processing Industry
In the food processing industry, vane pumps are employed for tasks such as transferring liquids, filling containers, and maintaining consistent flow rates in food production lines. Their ability to handle food-grade materials safely is a significant advantage.
6. Advantages and Disadvantages
Advantages
- Precise Control: Vane pumps offer precise control over flow and pressure, making them suitable for applications where accuracy is critical.
- Reliability: Vane pumps are known for their reliability and long service life when properly maintained.
- Versatility: They can handle a wide range of fluids, including corrosive and high-viscosity substances.
- Quiet Operation: Vane pumps operate with minimal noise and vibration, improving workplace comfort.
- Efficiency: Their low internal leakage and constant displacement contribute to high overall efficiency.
- Ease of Maintenance: Vane pumps have a simple design, making maintenance and repairs relatively straightforward.
Disadvantages
- Limited Pressure Range: Vane pumps may not be suitable for high-pressure applications when compared to piston pumps.
- Wear and Tear: Over time, the vanes and housing can experience wear, affecting pump performance.
- Temperature Sensitivity: Some vane pumps may be sensitive to temperature variations, requiring additional cooling measures in certain applications.
- Variable Displacement Complexity: Variable displacement vane pumps can be more complex and costly than their fixed displacement counterparts.
7. Maintenance and Troubleshooting
Maintenance Tips
To ensure the longevity and reliability of vane pumps, regular maintenance is essential. Here are some maintenance tips:
- Lubrication: Properly lubricate the vanes and rotor to reduce friction and wear.
- Inspect Vanes: Periodically inspect the vanes for signs of wear or damage and replace them as needed.
- Check Seals: Ensure that seals and gaskets are in good condition to prevent leaks.
- Monitor Temperature: Keep an eye on the operating temperature and implement cooling measures if necessary.
- Change Fluids: Regularly change the fluid to maintain its quality and prevent contamination.
Common Issues and Solutions
- Reduced Flow Rate: If the pump is delivering less fluid than expected, it may be due to worn vanes. Inspect and replace them if necessary.
- Fluid Leakage: Check for leaks around seals and gaskets, and replace any damaged components.
- Excessive Noise or Vibration: Excessive noise or vibration can be caused by misalignment or worn components. Ensure proper alignment and replace any worn parts.
- Overheating: Overheating can occur due to excessive friction or insufficient cooling. Address the root cause, whether it’s worn vanes, misalignment, or inadequate cooling.
8. Comparative Analysis
Vane Pumps vs. Gear Pumps
Vane pumps and gear pumps are both positive displacement pumps, but they have distinct differences:
Vane Pumps:
- Vane pumps have a higher efficiency compared to gear pumps.
- They offer better suction capabilities, making them suitable for applications with a vacuum or low inlet pressure.
- Vane pumps operate more quietly and with less vibration.
- Vane pumps can handle a wider range of fluid viscosities and are less sensitive to fluid properties.
Gear Pumps:
- Gear pumps are simpler in design and easier to manufacture.
- They are more cost-effective for low-pressure applications.
- Gear pumps are suitable for higher-pressure applications compared to vane pumps.
- Gear pumps may have limited capabilities with highly viscous fluids.
Vane Pumps vs. Piston Pumps
Another common comparison in the realm of positive displacement pumps is between vane pumps and piston pumps:
Vane Pumps:
- Vane pumps are generally less expensive and have lower maintenance costs.
- They are suitable for medium-pressure applications.
- Vane pumps offer good efficiency and control but may not match the precision of piston pumps in some applications.
Piston Pumps:
- Piston pumps are capable of higher pressures and are often used in heavy-duty applications.
- They provide precise control over flow and pressure.
- Piston pumps are more complex and expensive to manufacture and maintain compared to vane pumps.
9. Future Trends and Innovations
The field of vane pumps continues to evolve, with ongoing research and development aimed at improving performance, efficiency, and durability. Some notable trends and innovations include:
- Materials Advancements: Continued development of advanced materials for vanes and housing to enhance wear resistance and reduce friction.
- Variable Displacement Technologies: Further refinement of variable displacement vane pump technologies to provide greater control and adaptability in various applications.
- Smart Pumping Systems: Integration of sensors and IoT technologies to monitor pump performance in real-time and enable predictive maintenance.
- Environmental Considerations: Development of eco-friendly vane pump designs that minimize environmental impact through reduced fluid consumption and energy efficiency.
10. Conclusion
Vane pumps are a versatile and reliable class of positive displacement pumps that have found widespread use in a diverse range of industries. Their positive displacement nature, precise control over flow and pressure, and ability to handle various fluids make them invaluable in applications where consistency and efficiency are paramount.
Understanding the design, working principles, types, advantages, disadvantages, and maintenance requirements of vane pumps is essential for anyone involved in the fields of engineering, manufacturing, or fluid dynamics. As technology continues to advance, vane pumps are likely to see further refinements and innovations, ensuring their continued relevance in the industrial and hydraulic landscapes.