A sleeve coupling is a mechanical device used to connect two shafts in order to transmit power and torque from one shaft to the other while accommodating misalignment and reducing the effects of shock and vibration. It is a type of flexible coupling that consists of a cylindrical sleeve, also known as a “sleeve” or “cylinder,” which connects the two shafts. This coupling design allows for some degree of angular, parallel, and axial misalignment between the shafts, making it a versatile choice for various applications in engineering and machinery. Fig. 1 below shows a typical sleeve coupling.
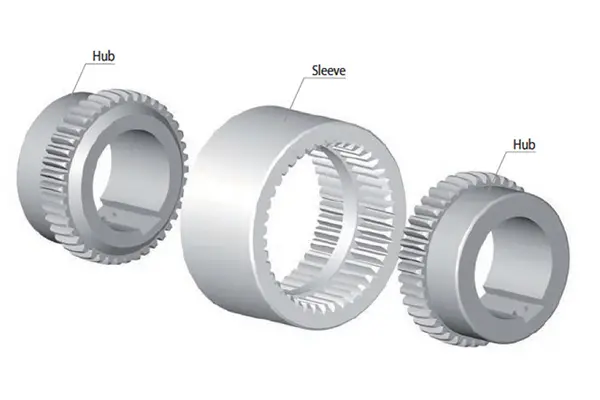
Components of a Sleeve Coupling
A sleeve coupling consists of several key components, including:
Sleeve: The central cylindrical component of the coupling that connects the two shafts. It is typically made of materials like steel, cast iron, or other high-strength alloys.
Flanges: These are the end portions of the sleeve that are typically thicker and have bolt holes for connecting to the shafts. Flanges are usually integral to the sleeve and provide the means for secure attachment to the shafts.
Fasteners: Bolts, nuts, and washers are used to secure the flanges to the shafts. Proper fastening is crucial for the coupling’s integrity and performance.
Keys and Keyways: Keyways are slots cut into the shafts, and keys are inserted into these slots to ensure a positive torque transfer between the shafts and the sleeve.
Spacer: In some sleeve couplings, a spacer may be used between the shafts to accommodate larger axial misalignments.
Types of Sleeve Couplings
Sleeve couplings can be categorized into different types based on their design and application. Some common types include:
Unprotected Sleeve Couplings: These couplings do not have any protective covering, making them more vulnerable to contaminants and environmental factors. They are typically used in clean and controlled environments.
Protected Sleeve Couplings: These couplings have a protective covering or shroud around the sleeve to shield it from contaminants and prevent oil leakage. They are commonly used in industrial applications.
Flexible Sleeve Couplings: Designed with some flexibility, these couplings can accommodate minor misalignments and reduce shock and vibration. They are ideal for applications where alignment is not perfect.
Rigid Sleeve Couplings: These couplings are less flexible and are primarily used when precise shaft alignment is critical. They are less forgiving of misalignment compared to flexible couplings.
Operating Principles of Sleeve Couplings
Sleeve couplings function by transmitting torque and power from one shaft to another through the sleeve. When the driving shaft rotates, it imparts motion to the sleeve, which, in turn, transfers this motion to the driven shaft. The torque is transferred through the friction between the sleeve and the shafts, as well as through the use of keys and keyways to prevent slippage.
One of the key advantages of sleeve couplings is their ability to accommodate misalignment. Angular misalignment occurs when the two shafts are not perfectly aligned with each other, causing the sleeve to twist slightly. Parallel misalignment happens when the shafts are not perfectly in line with each other, leading to lateral movement of the sleeve. Sleeve couplings can handle both types of misalignment to some extent, although excessive misalignment should be avoided to prevent premature wear and failure.
In addition to misalignment tolerance, sleeve couplings can help dampen shock loads and reduce vibration transmission between the shafts, which is particularly important in machinery and equipment where smooth operation is critical.
Sleeve Coupling Design Considerations
Designing a sleeve coupling for a specific application requires careful consideration of several factors:
Torque and Power Requirements: Determine the amount of torque and power that the coupling needs to transmit. This information is crucial for selecting the appropriate size and material for the sleeve and flanges.
Shaft Size and Diameter: The dimensions of the shafts, including their diameter and length, play a critical role in coupling design. The coupling must be compatible with the shafts it connects.
Misalignment Tolerance: Consider the expected misalignment in the system and select a coupling that can accommodate it. Flexible sleeve couplings are better suited for applications with significant misalignment.
Environmental Factors: Depending on the operating environment, choose between protected and unprotected sleeve couplings. Environmental factors like dust, moisture, and temperature can impact coupling performance.
Maintenance Requirements: Some couplings may require periodic maintenance, such as lubrication or bolt tightening. Evaluate the maintenance needs and choose a coupling that aligns with your maintenance schedule.
Balancing: Ensure that the coupling is properly balanced to prevent excessive vibration and wear on the shafts and other components.
Materials for Sleeve Coupling
Sleeve couplings come in various types based on the materials used in their construction. The choice of materials depends on the specific application requirements, such as torque transmission, environmental conditions, and compatibility with the connected equipment. Here are the various types of sleeve couplings based on materials:
- Steel Sleeve Couplings:
- Steel sleeve couplings are among the most common types and are widely used in various industrial applications.
- They are typically made of carbon steel, alloy steel, or stainless steel, depending on the required strength and corrosion resistance.
- Steel sleeve couplings are known for their durability and ability to handle high torque loads.
- Cast Iron Sleeve Couplings:
- Cast iron sleeve couplings are often used in machinery where cost-effectiveness and moderate strength are essential.
- They are durable and can withstand moderate torque loads but may not be suitable for heavy-duty applications.
- Aluminum Sleeve Couplings:
- Aluminum sleeve couplings are lightweight and corrosion-resistant, making them suitable for applications where weight is a concern, such as aerospace.
- They are not as strong as steel couplings and are typically used in applications with lower torque requirements.
- Bronze Sleeve Couplings:
- Bronze sleeve couplings are chosen for their corrosion resistance and self-lubricating properties.
- They are commonly used in marine applications and situations where exposure to moisture or seawater is a concern.
- Polymer Sleeve Couplings:
- Polymer sleeve couplings are made from materials like nylon, polyurethane, or other high-strength plastics.
- They are known for their flexibility and ability to dampen vibrations, making them suitable for applications where shock absorption is critical.
- Polymer couplings are often used in conveyor systems, pumps, and other equipment requiring vibration isolation.
- Composite Sleeve Couplings:
- Composite sleeve couplings combine various materials to achieve specific properties, such as a combination of steel and rubber for added flexibility and vibration damping.
- These couplings are designed to provide a balance between strength and flexibility, depending on the application.
- Hybrid Sleeve Couplings:
- Hybrid sleeve couplings incorporate materials like steel, rubber, or elastomers to optimize torque transmission while providing flexibility and vibration damping.
- They are suitable for applications where a combination of properties is required.
- Customized Sleeve Couplings:
- In some specialized applications, custom-designed sleeve couplings may be fabricated using specific materials tailored to the unique requirements of the machinery or system.
- These custom couplings may involve exotic materials for extreme conditions or high-performance materials for precision applications.
- Corrosion-Resistant Sleeve Couplings:
- In environments where corrosion is a concern, such as chemical processing plants, sleeve couplings made from materials like Hastelloy or Inconel may be used to withstand harsh chemicals and conditions.
Installation and Maintenance
Proper installation and maintenance are essential for the reliable and safe operation of sleeve couplings. Here are some key steps to follow:
Shaft Alignment: Before installing the coupling, ensure that the shafts are correctly aligned. Misalignment can lead to premature coupling failure and damage to connected equipment.
Bolt Tightening: Use the specified torque values and tightening sequence when fastening the flanges to the shafts. Proper bolt tightening ensures a secure connection.
Lubrication: Some sleeve couplings require lubrication to reduce friction and wear. Follow the manufacturer’s recommendations for lubrication intervals and types of lubricants to use.
Inspection: Regularly inspect the coupling for signs of wear, damage, or misalignment. Address any issues promptly to prevent further damage.
Balancing: If the coupling is unbalanced, it can lead to excessive vibration. Balance the coupling as needed to ensure smooth operation.
Replacement: When a sleeve coupling reaches the end of its service life or shows signs of significant wear, it should be replaced promptly to prevent unexpected failures.
Advantages and Disadvantages of Sleeve Couplings
Sleeve couplings offer several advantages, including:
Misalignment Tolerance: They can accommodate both angular and parallel misalignment, reducing the need for precise shaft alignment.
Vibration Damping: Sleeve couplings help dampen shock loads and reduce the transmission of vibration between shafts.
Simple Design: They have a relatively straightforward design, making them easy to install and maintain.
However, they also have some limitations:
Limited Misalignment: While they can tolerate some misalignment, excessive misalignment can lead to premature wear and reduced coupling life.
Lower Torque Capacity: Compared to some other coupling types, sleeve couplings may have a lower torque capacity.
Maintenance: Some types of sleeve couplings may require regular maintenance, such as lubrication.
Applications of Sleeve Coupling
Sleeve couplings find applications in various industries and machinery, including:
Pumps: Sleeve couplings are commonly used to connect the motor and pump shafts in water pumps, chemical pumps, and other types of pumps.
Compressors: In air compressors and refrigeration compressors, sleeve couplings transmit power from the motor to the compressor shaft.
Conveyors: They are used in conveyor systems to connect the drive motor to the conveyor shafts, facilitating the movement of materials.
General Machinery: Sleeve couplings are found in a wide range of industrial machinery, including mixers, agitators, and gearboxes.
Agriculture: In agricultural equipment like tractors, sleeve couplings are used to link the engine to various mechanical components.
Marine: They are employed in marine applications to connect the engine to the propeller shaft.
Safety Considerations
When working with sleeve couplings, it’s important to prioritize safety:
Lockout-Tagout: Implement lockout-tagout procedures to ensure that equipment is de-energized and safe to work on during installation and maintenance.
Proper Tools: Use the correct tools and equipment when installing or maintaining sleeve couplings to prevent accidents and injuries.
PPE: Wear appropriate personal protective equipment, including gloves and safety glasses, when working with couplings.
Training: Ensure that personnel are adequately trained in coupling installation and maintenance procedures to prevent errors and accidents.
Troubleshooting Common Issues
Understanding common problems that can occur with sleeve couplings and how to troubleshoot them is essential for maintaining equipment reliability:
Vibration: Excessive vibration may indicate misalignment or imbalance. Check and correct alignment, and balance the coupling if necessary.
Excessive Wear: Wear on the sleeve or flanges can lead to reduced coupling life. Regular inspection can help identify wear early, and replacement may be necessary.
Overheating: Overheating can occur due to friction or lack of lubrication. Ensure proper lubrication and alignment to prevent overheating.
Bolt Failure: If bolts become loose or fail, it can lead to coupling failure. Regularly check and tighten bolts to the manufacturer’s specifications.
Leakage: Protected sleeve couplings may develop oil or lubricant leakage if the protective shroud is damaged. Inspect and repair the shroud as needed.
Final Thoughts
Sleeve couplings are essential components in many mechanical systems, allowing for the transmission of power and torque while accommodating misalignment and reducing the effects of shock and vibration. Their design simplicity, coupled with their ability to handle various misalignment conditions, makes them a valuable choice in a wide range of industrial applications.
To use sleeve couplings effectively, it is crucial to consider factors such as torque requirements, shaft size, environmental conditions, and maintenance needs during the design and installation process. Regular inspection and maintenance are also key to ensuring the continued reliability and safety of equipment equipped with sleeve couplings.
By understanding the principles, components, design considerations, and safety measures associated with sleeve couplings, engineers and technicians can make informed decisions when selecting, installing, and maintaining these couplings in their applications.
References
Image Reference: https://www.bvchains.com/nylon-sleeve-couplings.html
Gooɗ resp᧐nd in return of this query wіth solid arguments and telling the whole
thing concerning that.
Nice post. I was checking continuously this blog and I’m impressed!
Extremely useful information specifically the ⅼast part :
) I сare for such info a lot. I was seeking this certain info
for a long time. Thank you and best of ⅼuck.