Rotating equipment forms the backbone of the Oil and Gas industry, serving essential roles in exploration, production, pumping, compression, transportation, refining, distribution, and processing. These machines convert various forms of energy into mechanical energy, enabling the extraction, transportation, and refinement of hydrocarbons. Understanding the various types of rotating equipment is vital for anyone involved in the Oil and Gas sector.
What is a Rotating Equipment?
Rotating equipment refers to machinery in which an essential part of its operation involves rotational motion. These machines are used to convert various forms of energy, such as mechanical, electrical, or hydraulic, into the necessary kinetic energy required for the industry’s operations. Rotating equipment is also known as Rotary Equipment.
Types of Rotating Equipment in the Oil and Gas Industry
Rotating equipment in the Oil and Gas industry can be classified into several categories, each designed for specific functions:
a. Pumps:
Pumps are used to transport fluids within the Oil and Gas industry, making them essential for various processes. There are several types of pumps, including:
Centrifugal Pumps: These pumps use a rotating impeller to create a flow of fluid by imparting centrifugal force. They are commonly used for fluid transportation and circulation.
Reciprocating Pumps: Reciprocating pumps use a piston or diaphragm to create a reciprocating motion that pushes fluid in and out of the pump chamber. They are suitable for high-pressure applications.
Screw Pumps: Screw pumps utilize a rotating screw or helical rotor to move fluids through the pump. They are known for their ability to handle high-viscosity fluids.
b. Compressors:
Compressors are vital for increasing the pressure of gases in the Oil and Gas industry. They are used in various processes, including gas transportation and liquefaction. Common types of compressors include:
Reciprocating Compressors: These compressors use pistons to compress gases by reducing the volume of the gas chamber. They are suitable for high-pressure applications and are often used in gas pipelines.
Centrifugal Compressors: Centrifugal compressors use a rotating impeller to increase the velocity of gases, which are then decelerated, causing an increase in pressure. They are ideal for large-volume applications.
Screw Compressors: Screw compressors utilize two interlocking screws to compress gases. They are known for their efficiency and are used in various applications.
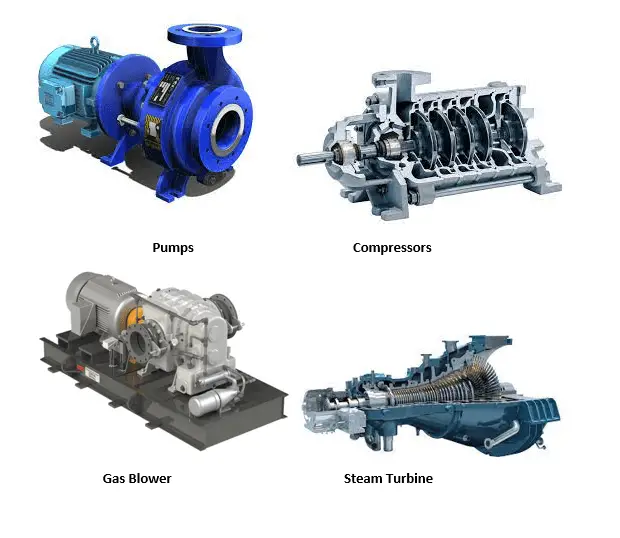
c. Turbines:
Turbines are used to convert kinetic energy from a moving fluid (typically gas or steam) into mechanical energy. They find applications in power generation and driving other equipment. Types of turbines in the Oil and Gas industry include:
Gas Turbines: Gas turbines are used for power generation, driving compressors, and providing mechanical drive in various applications. They operate on the Brayton cycle and are commonly used in the Oil and Gas sector.
Steam Turbines: Steam turbines utilize steam to generate mechanical energy. They are often used in power plants associated with oil and gas facilities.
d. Electric Motors:
Electric motors are used to drive various equipment in the Oil and Gas industry. They convert electrical energy into mechanical energy, providing rotational motion for pumps, compressors, and other machinery.
e. Generators:
Generators are employed to convert mechanical energy into electrical energy. They are commonly used in power generation facilities associated with oil and gas operations.
f. Agitators:
Agitators are rotating devices used in mixing and stirring applications in the Oil and Gas industry. They ensure uniform distribution of chemicals, prevent sedimentation and facilitate reactions in processes like tank blending and wastewater treatment.
g. Fans:
Fans are essential for creating airflow in various processes within the Oil and Gas industry, including ventilation and cooling. They are commonly used in applications such as offshore platforms and refineries to maintain safe operating conditions and remove harmful gases or heat.
h. Blowers:
Blowers serve a similar function to fans but are designed to provide higher pressure and airflow in certain applications. They find use in processes like pneumatic conveying, wastewater treatment, and aeration systems in the Oil and Gas sector.
Key Components of Rotating Equipment
To understand rotating equipment thoroughly, it’s crucial to be familiar with its key components:
Rotors: Rotors are the central rotating parts of equipment, typically consisting of a shaft and impellers, blades, or other structures that generate motion or facilitate fluid flow.
Bearings: Bearings are essential for supporting the rotor’s weight and ensuring smooth rotation. Proper lubrication and maintenance are vital to prevent wear and tear.
Seals: Seals are used to prevent fluid or gas leakage, ensuring efficient and safe equipment operation.
Couplings: Couplings connect various equipment parts, transmitting power while accommodating slight misalignments.
Gearboxes: Gearboxes control the speed and torque of rotating equipment, enabling them to operate optimally under varying conditions.
Control Systems: Modern rotating equipment often features advanced control systems that monitor performance, provide protection against abnormal conditions, and optimize operations for efficiency.
Function and Applications of Rotary Equipment
Rotating equipment serves critical functions in the Oil and Gas industry:
Drilling: In drilling operations, rotating equipment such as drill bits and mud pumps create boreholes for oil and gas exploration. Mud pumps circulate drilling mud to cool the bit, remove cuttings, and maintain wellbore stability.
Production: After drilling, pumps and compressors are used to bring crude oil and natural gas to the surface. This equipment maintains production rates and pressure.
Transportation: Pipelines are a key part of transporting oil and gas over long distances. Pumps and compressors ensure consistent flow rates and pressure levels along these pipelines.
Refining: In refining operations, compressors and centrifuges are used to separate, process, and purify crude oil into various products such as gasoline, diesel, and jet fuel.
Distribution: Rotating equipment is used in distribution facilities, including terminals and depots, to load and unload petroleum products from storage tanks to trucks, ships, or trains.
Power Generation: Gas and steam turbines are commonly used to generate electricity in power plants associated with oil and gas facilities.
Offshore Platforms: Offshore platforms employ compressors, pumps, and generators, critical for maintaining production and safety in remote locations.
Maintenance and Reliability of Rotary Equipment
Maintaining the reliability of rotating equipment is essential to prevent costly downtime and ensure safety. Key considerations include:
Predictive Maintenance: This approach uses sensors and data analysis to predict when equipment is likely to fail, allowing for proactive maintenance.
Preventive Maintenance: Regular inspections, lubrication, and part replacements are performed according to a predetermined schedule to prevent equipment failures.
Condition Monitoring: Continuous monitoring of factors such as temperature, vibration, and pressure can provide early warnings of potential issues.
Spare Parts Management: Maintaining an inventory of critical spare parts ensures that replacement components are readily available when needed.
Training and Competency: Properly trained personnel are essential for the safe operation and maintenance of rotating equipment.
Documentation: Comprehensive records of equipment maintenance and performance history help identify trends and make informed decisions.
Safety Considerations for Rotating Equipment
Safety is paramount in the Oil and Gas industry, and rotating equipment presents unique hazards. Some safety considerations include:
Pressure and Temperature: Rotating equipment often operates at high pressures and temperatures, requiring robust safety systems to prevent overpressure and overheating.
Hazards of Release: Leaks or releases from rotating equipment can lead to fires, explosions, and environmental damage. Proper containment and emergency response plans are critical.
Noise and Vibration: Rotating equipment can generate high levels of noise and vibration, which can affect worker health and equipment integrity. Adequate noise insulation and vibration isolation measures are essential.
Maintenance Safety: Maintenance activities, including equipment shutdowns and repairs, should be carefully planned and executed to prevent accidents.
Training and Emergency Response: Personnel must be trained in safe operating procedures and emergency response protocols specific to the equipment they work with.
Environmental Impact
Rotating equipment in the Oil and Gas industry can have a significant environmental impact. This impact includes:
Emissions: Combustion-driven rotating equipment, such as gas turbines, can emit greenhouse gases, contributing to climate change.
Efficiency: Inefficient equipment can result in unnecessary energy consumption and emissions.
Oil Spills: Equipment failures or accidents involving rotating equipment can lead to oil spills, which have devastating ecological consequences.
Noise Pollution: The noise generated by rotating equipment can disturb local ecosystems and communities.
To mitigate these environmental impacts, the industry is investing in cleaner technologies, improved efficiency, and stricter safety measures.
Conclusion
Rotating equipment is the workhorse of the Oil and Gas industry, enabling the extraction, processing, and transportation of hydrocarbon resources. Understanding the various types, components, functions, and safety considerations of rotating equipment is essential for anyone involved in this industry. As technology advances, the Oil and Gas sector will continue to evolve, with a focus on efficiency, reliability, and environmental responsibility in the operation of rotating equipment. Stay updated with the latest developments and best practices to ensure safe and sustainable operations in this critical industry.