Dear Readers,
HAZOP is a popular tool in risk assessment and a required skill for process/technical safety professionals. We will look into the details of this topic in this blog.
The blog includes:
- What is HAZOP?
- Methodology of HAZOP
- The Team required for the HAZOP Study
- Important Documents required
1. What is HAZOP?
HAZOP is the acronym for the term Hazard and Operability. It is a systematic study of the process to identify process deviations that can cause incidents and recommend actions to prevent them (reducing the likelihood of incidents to acceptable levels).
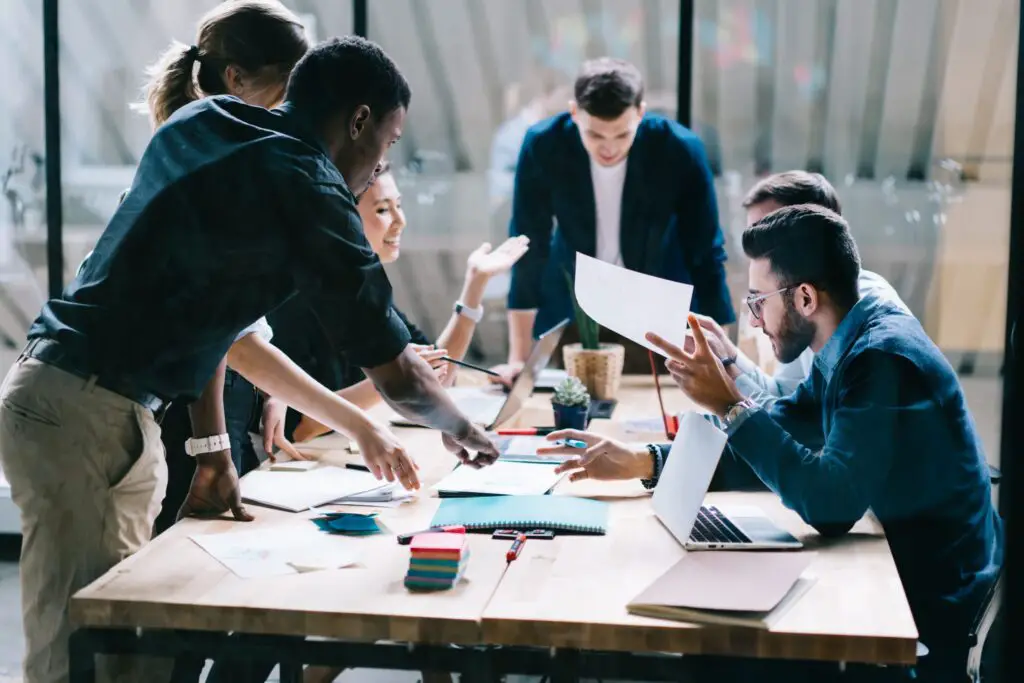
2. Methodology of HAZOP
The methodology can be divided into steps, which are as follows:
A. Node Creation
For detailed risk assessment, the process is divided into steps involved, and these steps are called Nodes. Nodes are defined so that a process step can be selected for detailed risk assessment. Ex. Charging of raw materials A and B inside the reactor and heating the reactor to x degC by steam to carry out the reaction to produce material C.
Node limits the scope of work and allows for more detailed analysis. It also ensures no part of the process is skipped from the risk assessment.
B. Process Deviations:
Understanding the impact of maloperation on the process is the main aim of HAZOP. Thus, process deviations are created and assessed in HAZOP sessions. Process deviation is nothing but a combination of guidewords like more, less, high, low, reverse, etc, and process parameters like temperature, pressure, flow, quantity, etc. So the deviations look like “more temperature,” “low flow,” and so on. These deviations trigger important questions to be answered so that risk can be identified.
C. Causes
Once the deviation is selected, we look for the causes that can cause this deviation. These causes are generally human error or control loop malfunction (also called the failure of the operational level). These causes are general drivers of the probability of an event taking place and are assigned a number based on either organizational guidelines or CCPS (Centre for Chemical Process Safety) standard frequencies for a cause to occur. For example, in a manually handled transfer operation from one tank to another based on observation of level gauges, human error can cause the tank to overflow.
D. Consequences
The consequence is the resultant damage that can occur in case the cause turns out to be real. It can range from negligible impact to catastrophic consequences, including multiple fatalities and irreversible damage to the environment. The higher the impact, the higher will be the severity of the consequences. For example, the overflow of material from a tank can cause impacts like toxic exposure or damage to the eye and skin based on its properties. MSDS is a good starting point to estimate the consequences and can be modified based on expected quantities to be released and the state of the material getting released (like temperature)
E. Risk Ranking
Risk ranking is nothing but the quantification of probabilities that the process deviation will occur (or cause will create process deviation) and the severity of the consequences ranging from negligible to Catastrophic. Risk ranking gives HAZOP a semi-quantitative nature as the result of a deviation carries a risk number with it. For example, the probability of a human error is generally considered to be more than once in a year (probability = 4), and if it causes a reversible injury like skin burns, the severity can be considered as 3. A resultant multiplication will give 12 as a risk number. The categorization of this risk into acceptable, as low as reasonably practicable (ALARP), and unacceptable is done based on a risk matrix.
Example of Risk Matrix
An example of a risk matrix (a commonly used 5X5 risk matrix)
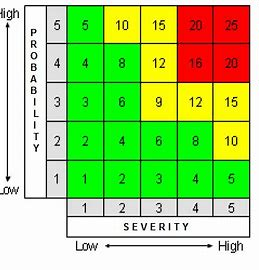
3. Team Required for HAZOP Study
HAZOP is a group exercise performed with a team consisting of representatives from operations, process engineering, instrumentation, maintenance, and safety. R&D and electrical personnel can be contacted in case of query. A Process Safety professional leads the discussion and can also play the role of a scribe (writer) additionally.
4. Important Documents Required for HAZOP
To avoid guesswork and conflicts during risk assessment, the following documents are required to start the HAZOP. Ensuring the correctness of these documents is really important, as the risk assessment will be based on these documents, and an error can cause a wrong judgment, leading to a major process safety incident.
- A. Updated and As-built P&ID
- B. Updated SOP with tag numbers of equipment
- C. Interlock Matrix with Interlock set values
- D. Heats of reactions and thermal Stability data of intermediates and products
- E. Powder safety properties of any solids involved
- F. MSDS
- G. Other technical documents may be required based on risk assessment, like scrubber capacity, condenser sizing, etc.
It should be noted here that HAZOP considers that a sound process design study has been performed for the sizing of equipment and generally does not seek to review the same during HAZOP. It can convert a HAZOP session to a process design workshop otherwise!
Summarizing,
The intention of HAZOP is to suggest the measures so that overall risk is preferably in an acceptable range and at least in the ALARP range. As severities are mostly unchanged as those are based on material properties, the frequency of causes is reduced by means of safeguards. This reduces the overall risk number and brings it into an acceptable range.
However, the reduction in probabilities of high-risk events should not be done semi-quantitatively, and the LOPA approach should be applied. We will understand what LOPA is in a separate blog. If you want an example of a HAZOP on the actual process, do let us know in the comments.
I am welding students who like to read about the oil and gas industry,, upon what intervals is it acceptable for HAZOP performance.
Hazop cycles are generally carried in a span of 3 to 5 years. However, incase of major process change, HAZOP is performed to assess the safety relevant impact of the change.