FMECA or Failure modes, effects, and criticality analysis is a systematic and proactive technique to identify and analyze potential failure modes for various parts of a system. FMECA helps to assess the effects that these failure modes may have on the system and to rank the issues relative to severity. Then it devises the steps to avoid failure or mitigate the effects resulting from failures that will be on the system. The FMECA technique is therefore widely used to identify and resolve potential problems of any system before they occur.
FMECA was first developed in the United States by their Military team in 1949. It has now become one of the most widely used reliability analysis techniques in almost all industries involving products, designs, or processes. Even though the terminologies, purpose, and other details may slightly vary depending on the application of the FMECA technique, the base methodology is similar for all.
In general, FMECA is done during the starting phases (conceptual and initial design phase) of the system. This process ensures that all potential failure modes are considered early and the proper provisions to eliminate these failures are considered.
Uses of FMECA
FMECA methodology can be used in a wide array of applications. Some of the FMECA uses are:
- To provide a quantitative reliability and availability analysis basis.
- To assist in deciding alternative designs with high reliability and safety potential during the early stages of the design process.
- To ensure that all probable failure modes and their damaging effects on the system operators have been considered.
- To identify and list all potential failure modes and decide their severity of effects.
- To develop test planning criteria and requirements for test equipment.
- To provide historical documentation for future reference to aid in the analysis of field failures and consideration of design changes.
- To provide a maintenance planning basis.
Types of FMECA
Broadly, there are three types of FMECA methodologies. They are
- Design FMECA: The main aim to carry out designing FMECA is to identify and eliminate potential failures during design. This methodology takes into account all types of failure modes that may occur during the whole lifespan of the equipment and consideration of factors of safety and other criteria are made during design.
- Process FMECA: It focuses on problems that arise from the process of manufacturing, operation, and maintenance of the system or equipment.
- System FMECA: This type of FMECA thoroughly checks the larger processes to find potential problems for example an entire production line.
Codes and Standards for FMECA
Various standards provide guidelines for the FMECA process. Some of those FMECA standards are:
- MIL-STD 1629
- IEC 60812
- BS 5760-5
- SAE ARP 5580
- AIAG FMEA-4
- SAE J1739
- SEMATECH “Failure Modes and Effects Analysis (FMEA)
FMECA Approaches
There are two approaches to FMECA; the bottom-up approach and the Top-down approach.
When the system concept is already decided, a bottom-up approach will be beneficial. In the bottom-up approach, also known as the hardware approach, each component is studied individually, and when all components are considered the analysis is complete.
Whereas the top-down FMECA approach is widely used during early design stages when the complete system structure is yet to be finalized. This approach is function-oriented. The top-down FMECA analysis starts with the main system functions and identifies how these may fail. This approach can also be used on existing systems to decide on problem areas.
What are the elements of FMECA?
FMECA can be performed at the functional or component-part level. The major elements of the FMECA process are:
- Defining the system.
- Defining ground rules and assumptions to help drive the design.
- Construction of system block diagrams.
- Identification of failure modes.
- Failure cause and effect analysis.
- Feeding the results back into the design process.
- Classification of the failure effects according to severity.
- Performing criticality calculations.
- Ranking the failure mode based on their criticality.
- Determining the critical items
- Deciding on means of failure detection, isolation, and compensation
- Maintainability analysis
- Documentation
- Recommendations
- Follow up on corrective action implementation/effectiveness
FMECA Process
To apply FMECA, the system must be defined with proper system boundaries. The assumptions need to be made depending on the expected outcome from the analysis. The operational and environmental conditions that will impact the system must be considered. All available system information like drawings, specifications, component lists, schematic diagrams, functional descriptions, etc needs to be collected.
Next, the system is divided into manageable parts known as functional elements. It is preferable if the system is illustrated using a hierarchical tree diagram or functional block diagram.
To avoid wasting effort and money, the FMECA analysis is usually started with higher levels of the system hierarchy. When unacceptable consequences are found on this higher level, then the particular sub-elements (subsystem, sub-subsystem, or component) are then looked into to identify failure modes and failure causes on a lower level.
A suitable FMECA worksheet is decided at this stage. The FMECA analyst shall consider all the functions of all the elements, and judge if any element failure can result in any unacceptable system behavior. If the answer is no, then no further analysis of that specific element is required, else the element must be examined further.
In the next step, risks associated with various failure modes are studied and ranked. They are usually presented using any one of the following two methods:
- Risk Matrix
- Risk Priority Number (RPN)
Risk Matrix
The risk matrix is prepared considering the following two parameters:
- the risk associated with failure mode with a function of the frequency of the failure mode and
- the potential end effects (severity) of the failure mode.
Fig. 1 below shows a Typical Risk Matrix.
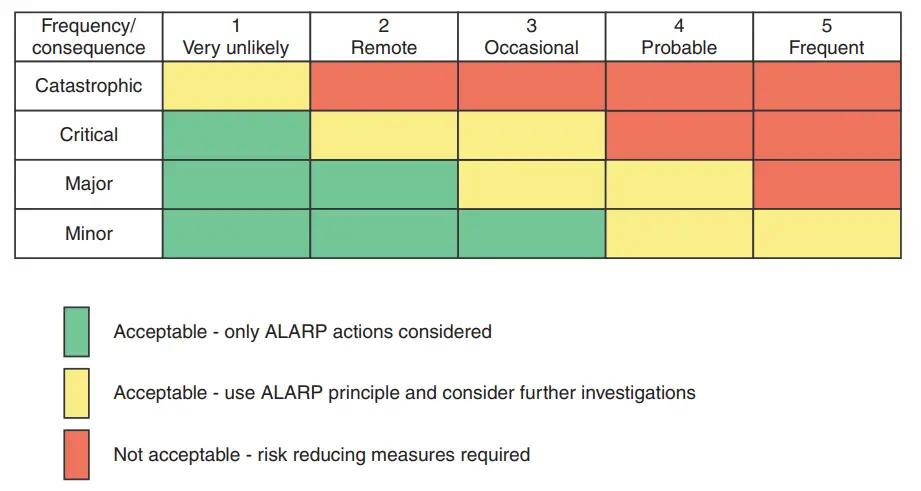
Risk Priority Number
The risk priority number (RPN) is calculated as follows:
RPN = S × O × D
Here,
- O = the rank of the occurrence of the failure mode.
- S = the rank of the severity of the failure mode.
- D = the rank of the likelihood that the failure will be detected before the system reaches the end-user/customer.
- All these ranks are given on a scale from 1 to 10
The smaller the RPN the better and vice versa.
FMECA Review Team
FMECA team consists of key industry professionals as listed below:
- Project manager
- Design engineer (hardware/software/systems)
- Test Engineer
- Reliability Engineer
- Quality Engineer
- Maintenance Engineer
- Field service engineer
- Manufacturing/process engineer
- Safety engineer
This review team studies the FMECA worksheets and the risk matrices or the risk priority numbers (RPN) with the purpose of:
- Deciding whether or not the system is acceptable.
- Identifying feasible improvements of the system to reduce the risk.
The FMECA review team works together to eliminate the likelihood of failure occurrences and to reduce the effects caused by unforeseen failures. Improvements of various kinds may be devised and accordingly, the FMECA worksheet and RPN should be updated. Some of the processes involving risk reduction are:
- Design changes aiming at risk reduction
- Introducing Engineered safety features
- Incorporating Safety devices
- Installing Warning devices
- Proper Procedures/training of concerned personnel.
Advantages and Disadvantages of FMECA
The main benefits of FMECA are:
- Reliable and structured method.
- Application and Concept are easy to learn.
- Better quality of the process, product, and services.
- Increased sales due to better quality and customer satisfaction.
- Increased safety margin.
- Effective control plan.
- Minimized warranty cost.
However, there are some disadvantages to the FMECA process as well. These are:
- Tedious and time-consuming process.
- Not suitable for multiple failures.
Online Course on Risk Analysis and Management by applying the most widely used and accepted methodology: FMEA/FMECA
Attend this online course by clicking here to learn about the following in detail:
- How to perform the FMEA/FMECA analysis on products and design/production processes.
- Understanding the meaning of criticality analysis.
- How to perform qualitative, semi-quantitative, and quantitative criticality analysis.
- Using the criticality matrix and Risk Priority Number to prioritize remedial or preventive actions.
- How to properly use an FMEA/FMECA worksheet, criticality matrix, and report.