Corrosion is one of the most destructive natural processes that affect metals and alloys. It is a gradual degradation caused by the environment, which leads to the weakening and eventual failure of structures, machinery, and tools. This has a significant economic impact, particularly in industries like oil and gas, chemical processing, transportation, and infrastructure. One way to combat this destructive process is by using Corrosion Resistant Alloys (CRAs). CRAs are materials specifically designed to withstand corrosive environments, which makes them highly valuable in industries where longevity, durability, and safety are paramount.
What are Corrosion Resistant Alloys (CRAs)?
Corrosion Resistant Alloys (CRA) are specifically designed to withstand the harsh effects of corrosion. They are typically composed of base metals like iron, nickel, or titanium, which are alloyed with other elements that enhance their resistance to corrosion. The main goal of these alloys is to reduce the rate of corrosion in harsh environments, thereby increasing the service life of equipment and structures.
Common Elements in CRAs
Several elements are commonly added to base metals to create corrosion-resistant alloys. Each element plays a specific role in improving the properties of the alloy.
- Chromium (Cr): Chromium is a key element in many CRAs, particularly stainless steel. When chromium reacts with oxygen, it forms a thin, stable layer of chromium oxide on the surface, which prevents further oxidation.
- Nickel (Ni): Nickel improves the overall toughness and ductility of an alloy. It is also very effective in resisting corrosion in both acidic and alkaline environments.
- Molybdenum (Mo): Molybdenum enhances the corrosion resistance of alloys in chloride-rich environments, making it valuable for applications like marine and chemical processing industries.
- Copper (Cu): Copper is often added to alloys that are designed to resist corrosion in acidic environments, such as in plumbing and roofing materials.
- Titanium (Ti): Titanium is highly resistant to corrosion, particularly in saltwater and acidic environments. It is used in industries like aerospace and medical implants.
- Tantalum (Ta): Tantalum is a rare and highly corrosion-resistant element that is used in very specific, high-performance applications, such as chemical processing equipment and medical devices.
Types of Corrosion Resistant Alloys
There are several types of CRAs, each with its own unique properties and applications:
Stainless Steels:
Stainless steels are the most common CRAs, known for their high chromium content (typically over 10.5%) and excellent resistance to oxidation and rust. There are different grades of stainless steel, such as austenitic, ferritic, martensitic, and duplex stainless steel, each offering different levels of corrosion resistance and mechanical properties.
Ferritic Stainless Steels
Ferritic stainless steel, like Type 430, is a type of rust-resistant steel made primarily by adding chromium to the alloy. While they can’t be strengthened through heat treatment, adding carbon and other elements transforms them into another type called Martensitic Stainless Steel.
Martensitic Stainless Steels
Common Martensitic Stainless steel, such as Type 410 (also called 13 Chrome), can be strengthened through heat treatment methods like quenching and tempering. Some of these steels, like Type 17-4, belong to the precipitation-hardened family, which further enhances their strength. Martensitic steels often contain nickel and molybdenum to boost their corrosion resistance.
Austenitic Stainless Steels
Austenitic Stainless Steels, such as Types 304 and 316, are created by adding enough Nickel to the alloy. These steels are highly resistant to rust. Some high-alloy types, like 28 Chrome and 2535, are commonly used in oil and gas production. Although most Austenitic Stainless Steels can’t be heat-treated for strength, they can be made stronger through cold working. One exception is the Precipitation Hardened Austenitic Stainless Steel, Type A286, which can be heat-treated.
Duplex Stainless Steels
Duplex Stainless Steels are a mix of Chromium, Nickel, and Molybdenum, balancing properties between Ferritic and Austenitic Stainless Steels. These alloys have a microstructure that is a combination of Ferrite and Austenite, which gives them their name. Duplex steels can be cold worked to achieve very high strength and are often used in environments where pitting or crevice corrosion is a problem, such as in water with high chloride content or dissolved oxygen.
Super Duplex Stainless Steels
The most alloyed type of Duplex steels is known as Super Duplex Stainless Steels. Along with Chromium, Nickel, and Molybdenum, these steels may include additional elements like Copper and Tungsten to improve their corrosion resistance in specific environments.
Nickel-Based Alloys:
These alloys contain high levels of nickel, which provides excellent resistance to corrosion in acidic and high-temperature environments. Examples include Inconel, Hastelloy, and Monel alloys, which are used in industries like aerospace, chemical processing, and nuclear power.
Titanium Alloys:
Titanium alloys are lightweight, strong, and highly resistant to corrosion, particularly in seawater. They are used in marine, aerospace, and biomedical applications due to their biocompatibility and excellent strength-to-weight ratio.
Copper Alloys:
Copper and its alloys (such as brass and bronze) are known for their resistance to corrosion, especially in water and marine environments. Copper alloys are commonly used in plumbing, electrical wiring, and heat exchangers.
Aluminum Alloys:
Aluminum has excellent resistance to corrosion due to the formation of a protective oxide layer. Aluminum alloys are lightweight and are commonly used in transportation, aerospace, and structural applications.
Applications of Corrosion Resistant Alloys
Corrosion Resistant Alloys are used in a wide range of industries where durability and resistance to corrosive environments are critical. Let’s explore some of the key sectors that rely heavily on CRAs.
Oil and Gas Industry
The oil and gas industry operates in some of the most corrosive environments, from offshore rigs exposed to seawater to deep wells where high pressures and temperatures can accelerate corrosion. CRAs, such as duplex stainless steel and nickel-based alloys, are essential for downhole tubing, pipelines, and other critical components that must withstand these harsh conditions.
- Pipelines: Pipelines transporting corrosive fluids like crude oil and natural gas need to be highly resistant to corrosion to avoid leaks and failures. CRAs are often used to line pipelines or manufacture critical sections of the pipeline infrastructure.
- Offshore Platforms: Offshore drilling platforms are exposed to constant moisture and salt, which can cause rapid corrosion of metal components. Stainless steel and titanium alloys are often used for structural components and equipment.
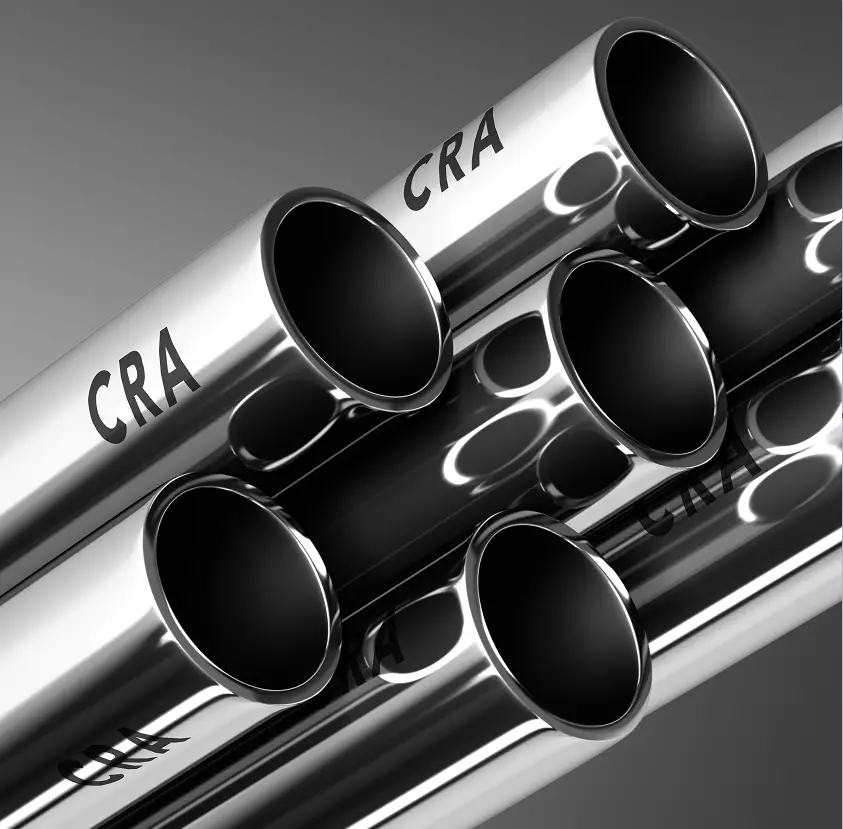
Chemical Processing Industry
The chemical processing industry deals with highly corrosive substances, including acids, alkalis, and solvents. Equipment in this industry must be highly resistant to corrosion to ensure safety and efficiency.
- Reactors and Tanks: Nickel-based alloys and stainless steel are commonly used for reactors, storage tanks, and piping systems in chemical plants to resist the corrosive effects of chemicals.
- Heat Exchangers: Heat exchangers are exposed to high temperatures and corrosive substances, making CRAs essential for ensuring their longevity and efficiency.
Aerospace Industry
The aerospace industry demands materials that can withstand extreme conditions, including high temperatures, pressure changes, and exposure to corrosive elements such as fuel and hydraulic fluids.
- Jet Engines: Nickel-based superalloys, such as Inconel, are used in jet engine components due to their ability to resist oxidation and maintain their strength at high temperatures.
- Aircraft Structures: Titanium alloys are used in aircraft structures and fasteners because of their high strength-to-weight ratio and resistance to corrosion, especially in coastal or saltwater environments.
Marine Industry
Marine environments are highly corrosive due to the presence of saltwater and humidity. Corrosion-resistant materials are crucial for ships, submarines, and offshore platforms.
- Shipbuilding: Stainless steel, aluminum, and titanium alloys are commonly used in the construction of ships to resist corrosion from saltwater exposure.
- Submarine Hulls: Titanium alloys are often used in submarine hulls because of their ability to withstand the corrosive effects of seawater while maintaining structural integrity under high pressure.
Biomedical Industry
The biomedical field requires materials that can withstand corrosion in the human body, particularly for implants and medical devices. These materials must be biocompatible and resistant to body fluids, which are naturally corrosive.
- Orthopedic Implants: Titanium and cobalt-chromium alloys are used in orthopedic implants such as hip and knee replacements because of their corrosion resistance and biocompatibility.
- Surgical Instruments: Stainless steel is commonly used for surgical instruments due to its resistance to corrosion from repeated sterilization processes and exposure to bodily fluids.
In conclusion, Corrosion Resistant Alloys are essential materials that play a critical role in modern industry. Their ability to withstand harsh environments and extend the lifespan of equipment and structures makes them invaluable in sectors such as oil and gas, aerospace, marine, and biomedical.