Aluminum alloys are a remarkable class of materials that have transformed the way we design, build, and use various products across industries. Renowned for their exceptional blend of properties, including lightweight nature, corrosion resistance, good conductivity, and ease of fabrication, aluminum alloys are integral to modern engineering. In this comprehensive guide, we will delve deep into the world of aluminum alloys, offering insights into their composition, properties, manufacturing processes, diverse types, common applications, advantages, disadvantages, and future trends.
Composition of Aluminum Alloys
To understand the remarkable diversity of aluminum alloys, it’s essential to explore their composition. Aluminum alloys are primarily composed of aluminum (Al) and various alloying elements that are carefully selected and blended to achieve specific material properties. These alloying elements include:
- Copper (Cu): Copper is added to aluminum alloys to enhance their strength and corrosion resistance. It also improves the alloy’s ability to withstand elevated temperatures, making it suitable for applications in the aerospace and automotive industries.
- Magnesium (Mg): Magnesium contributes to both strength and corrosion resistance, particularly in marine environments. Aluminum-magnesium alloys are favored for their lightweight, making them a staple in aircraft construction.
- Silicon (Si): Silicon is utilized to improve the castability and fluidity of aluminum during manufacturing processes. This is particularly useful in the production of intricate components.
- Zinc (Zn): Zinc enhances the strength and hardness of aluminum alloys, making them ideal for structural applications. It also contributes to improved corrosion resistance.
- Manganese (Mn): Manganese is used in aluminum alloys to enhance their strength and workability. It is commonly found in alloys used for automotive components and construction materials.
- Lithium (Li): In high-performance aerospace alloys, lithium is introduced to reduce weight while maintaining strength and stiffness. Aluminum-lithium (Al-Li) alloys are renowned for their lightweight properties.
- Iron (Fe): Iron is added to aluminum alloys to increase their strength; however, it can reduce the alloy’s corrosion resistance. Careful consideration is required in applications where corrosion is a concern.
- Nickel (Ni): Nickel is employed to enhance the strength and toughness of aluminum alloys, making them suitable for critical structural components in aerospace and defense industries.
The precise combination and proportions of these alloying elements result in a vast array of aluminum alloys, each tailored to fulfill specific requirements across industries.
Types of Aluminum Alloys
The extensive family of aluminum alloys is organized into different series based on their alloying elements and properties. Understanding these series is vital for selecting the right alloy for a specific application. Here are some of the most common aluminum alloy series:
1000 Series:
The 1000 series comprises nearly pure aluminum, with a minimum aluminum content of 99%. These alloys are primarily valued for their exceptional corrosion resistance and excellent electrical conductivity. They are commonly used in electrical conductors, packaging materials, and food containers.
2000 Series Aluminum Alloy:
Alloys in the 2000 series incorporate copper as the primary alloying element. The addition of copper imparts excellent strength and high-temperature performance. As a result, aluminum-copper alloys are prevalent in aerospace applications, including aircraft components and structural parts. The most common aircraft alloy is 2024.
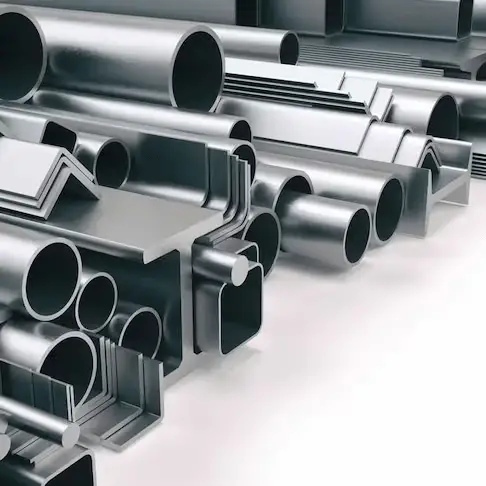
3000 Series Aluminium Alloy:
Aluminum-manganese alloys make up the 3000 series. These alloys offer a balanced combination of strength, formability, and corrosion resistance. They are frequently employed in applications such as cooking utensils, chemical equipment, and beverage cans. The widely favored alloy within this series is 3003, known for its ease of workability and moderate strength. It is commonly utilized in the production of cooking utensils. Additionally, alloy 3004 is among the alloys employed in the manufacturing of aluminum beverage cans.
4000 Series Aluminum Alloy
The primary alloying element in the 4000 series is silicon, which imparts remarkable qualities to aluminum. Silicon enhances aluminum’s molten fluidity and reduces shrinkage during solidification. This series exhibits good machinability, moderate strength, and commendable corrosion resistance. It is particularly favored in the automotive sector for applications such as engine blocks, where efficient heat dissipation is essential. Alloy 4043 is used to make filler alloys for welding cars and structural elements.
5000 Series Aluminum Alloy:
Alloys in the 5000 series are characterized by the addition of magnesium, which enhances both strength and corrosion resistance. These alloys are widely used in marine applications, automotive components, and structural parts. Alloy 5182 is used to make the lid of aluminum beverage cans.
Aluminium Alloy 6000 Series:
Aluminum-silicon alloys define the 6000 series. These alloys are appreciated for their excellent formability, weldability, and heat resistance. They find extensive use in architectural and structural applications, including window frames and extrusions. The prevalent alloy within this series is 6061, primarily employed in the construction of truck and boat frames. Extruded components derived from the 6xxx series find application in architectural projects, as well as in the manufacture of the iPhone
7000 Series:
The 7000 series is known for its high strength and toughness. Zinc is the main alloying constituent of these series. These alloys are utilized in demanding aerospace and high-performance applications where superior mechanical properties are essential. Important alloys are 7050 and 7075, both of which are used to construct aircraft.
8000 Series Aluminum Alloy:
The 8000 series encompasses specialized alloys, including aluminum-lithium (Al-Li) alloys. Al-Li alloys are highly regarded for their exceptional strength-to-weight ratios, making them a preferred choice in aerospace applications for weight reduction without sacrificing structural integrity. Examples include 8500, 8510, and 8520.
Properties of Aluminum Alloys
Aluminum alloys exhibit a remarkable range of properties, which contribute to their widespread usage in various applications. Understanding these properties is crucial to appreciating the versatility of aluminum alloys:
- Lightweight: Aluminum is inherently lightweight, with a density of approximately one-third that of steel (Click here to learn major differences between Aluminum and Steel). This unique characteristic makes aluminum alloys an ideal choice for applications where weight reduction is critical, such as aerospace, automotive, and consumer electronics.
- Corrosion Resistance: Aluminum alloys naturally form a thin oxide layer on their surface, providing excellent corrosion resistance. This oxide layer acts as a protective barrier against environmental factors, ensuring the longevity of aluminum components even in harsh conditions.
- High Strength-to-Weight Ratio: Many aluminum alloys offer an impressive strength-to-weight ratio, which means they provide substantial strength while remaining exceptionally lightweight. This property is especially valuable in structural and load-bearing applications.
- Good Conductivity: Aluminum is an excellent conductor of both heat and electricity. This property finds extensive use in electrical applications, including power transmission lines, electrical conductors, and heat sinks in electronic devices.
- Malleability and Ductility: Aluminum alloys possess excellent malleability and ductility, allowing them to be easily shaped, rolled, extruded, and machined into various forms. This versatility in fabrication methods makes them suitable for a wide range of manufacturing processes.
- Non-Magnetic: Aluminum alloys are non-magnetic, a property that is advantageous in applications where electromagnetic interference needs to be minimized, such as in electronic devices and MRI machines. Click here to explore Why is Aluminum Non-Magnetic
- Recyclability: Aluminum is highly recyclable, and the recycling process requires significantly less energy compared to primary aluminum production. This sustainability aspect contributes to the environmental appeal of aluminum alloys.
Manufacturing of Aluminum Alloys
The manufacturing process of aluminum alloys can vary depending on the desired product, alloy composition, and intended application. However, several common steps are involved in the production of aluminum alloys:
- Extraction of Aluminum: The journey of an aluminum alloy begins with the extraction of aluminum from bauxite ore. This process, known as the Bayer process, converts bauxite into alumina (aluminum oxide). Subsequently, alumina is reduced to aluminum metal through the energy-intensive process of electrolysis in a smelting cell.
- Alloying: Once aluminum metal is obtained, it is meticulously combined with alloying elements in precise proportions to achieve the desired alloy composition. The alloying process involves melting the aluminum and introducing the alloying elements to create a homogenous alloy.
- Casting: The molten aluminum alloy is cast into various shapes, such as ingots, billets, or custom molds. Casting methods can include die casting, sand casting, and continuous casting, depending on the intended application and production scale.
- Heat Treatment: Heat treatment processes play a critical role in refining the properties of aluminum alloys. Annealing, quenching, and tempering are some of the common heat treatment techniques used to improve mechanical properties, such as hardness and ductility.
- Forming and Machining: Following casting and heat treatment, aluminum alloys undergo further processing through methods like rolling, extrusion, and machining. These processes allow manufacturers to create specific shapes and dimensions tailored to the application’s requirements.
- Surface Treatment: In some cases, aluminum alloys undergo surface treatments for various purposes. Anodizing is a common surface treatment that enhances corrosion resistance and provides an aesthetic finish. Painting or coating may also be applied for additional protection or customization.
The intricate manufacturing process ensures that aluminum alloys meet stringent quality and performance standards, making them suitable for a wide range of applications.
Common Applications of Aluminum Alloys
The versatility of aluminum alloys is evident in their broad spectrum of applications across various industries. These alloys play pivotal roles in shaping modern technologies and products. Here are some of the most common applications of aluminum alloys:
- Aerospace: The aerospace industry heavily relies on aluminum alloys due to their lightweight nature, high strength, and exceptional corrosion resistance. Aluminum alloys are used in the construction of aircraft frames, wings, fuselages, and engine components.
- Automotive: In the pursuit of fuel efficiency and reduced emissions, the automotive industry extensively incorporates aluminum alloys. These alloys find application in car bodies, engine components, suspension systems, wheels, and transmission housings to minimize weight and enhance performance.
- Construction: Aluminum alloys are preferred materials in the construction sector. They are used for structural elements, windows, doors, facades, and roofing due to their corrosion resistance, low maintenance requirements, and ability to withstand harsh environmental conditions.
- Electrical and Electronics: Aluminum’s excellent electrical conductivity makes it indispensable in the electrical and electronics industries. Aluminum alloys are employed in power transmission lines, electrical conductors, heat sinks for electronic devices, and electrical enclosures.
- Packaging: Aluminum foils and containers are popular choices for packaging food and beverages. Their impermeability to light, moisture, and oxygen ensures the preservation of food quality and freshness.
- Marine: Aluminum alloys are well-suited for marine applications, thanks to their corrosion resistance in saltwater environments. They are utilized in boat hulls, masts, decks, and other marine components.
- Consumer Goods: The consumer goods industry benefits from aluminum alloys in the production of various products, including kitchen utensils, sports equipment, mobile phone casings, and even bicycles.
- Transportation: Aluminum alloys are essential in multiple modes of transportation, including trains, bicycles, and ships, where lightweight materials are crucial to improve fuel efficiency and overall performance.
The adaptability of aluminum alloys to diverse applications underscores their significance in modern manufacturing and engineering. As industries continue to evolve and innovate, aluminum alloys are likely to remain at the forefront of material choices for new products and technologies.
Advantages and Disadvantages
As with any material, aluminum alloys come with their own set of advantages and disadvantages, which should be carefully considered when selecting them for specific applications.
Advantages of Aluminum Alloys:
- Lightweight: Aluminum alloys are significantly lighter than steel, contributing to improved fuel efficiency, higher payload capacities, and ease of handling in various applications.
- Corrosion Resistance: The natural oxide layer on aluminum provides exceptional corrosion resistance, allowing aluminum alloys to endure harsh environmental conditions without deteriorating.
- High Strength-to-Weight Ratio: Many aluminum alloys offer a remarkable strength-to-weight ratio, ensuring structural integrity while keeping weight to a minimum.
- Conductivity: Aluminum is an excellent conductor of electricity, making it invaluable in electrical and electronic applications, where efficient energy transfer is essential.
- Recyclability: Aluminum is highly recyclable, with recycling processes consuming significantly less energy compared to primary aluminum production. This recyclability reduces environmental impact and resource consumption.
Disadvantages of Aluminum Alloys:
- Lower Strength than Steel: While aluminum alloys are strong, they generally have lower tensile strength compared to steel alloys. In applications requiring exceptionally high strength, steel may be a preferred choice.
- Susceptibility to Galvanic Corrosion: When in contact with certain dissimilar metals, aluminum can undergo galvanic corrosion. Proper material selection and corrosion prevention measures are necessary in such situations.
- Higher Cost: Aluminum alloys can be more expensive than some other materials, impacting production costs. However, the long-term benefits, such as reduced maintenance and improved fuel efficiency, often justify the initial investment.
- Limited High-Temperature Performance: Aluminum alloys can experience a reduction in strength at elevated temperatures, limiting their use in applications with high thermal loads.
- Fatigue Resistance: Some aluminum alloys may have lower fatigue resistance compared to steel, requiring careful consideration in applications subjected to cyclic loading.
Future Trends in Aluminum Alloy Technology
The realm of aluminum alloy technology is continually evolving to meet the ever-changing demands of industries and the need for sustainability. Several notable trends are shaping the future of aluminum alloys:
- Advanced Alloys: Research and development efforts are focused on creating new aluminum alloys with enhanced properties, including higher strength, improved corrosion resistance, and better high-temperature performance. These advanced alloys open doors to novel applications and materials engineering solutions.
- Hybrid Materials: The combination of aluminum with other materials, such as carbon fiber composites, is gaining prominence. Hybrid materials offer the potential to achieve superior strength-to-weight ratios, enabling innovative designs and structural solutions.
- Sustainability: Environmental concerns are driving the aluminum industry to reduce energy consumption during primary production and increase the use of recycled aluminum. Sustainable practices, including closed-loop recycling systems, are being adopted to minimize the environmental footprint of aluminum alloys.
- Additive Manufacturing: 3D printing technology is being harnessed to produce complex and lightweight structures with aluminum alloys. This additive manufacturing approach allows for rapid prototyping and the creation of intricate parts, especially in the aerospace and automotive industries.
- Lightweighting: Industries such as automotive and aerospace continue to prioritize lightweight strategies to enhance fuel efficiency and reduce emissions. Aluminum alloys, with their exceptional strength-to-weight ratio, are integral to these efforts.
Final Thoughts
In conclusion, aluminum alloys stand as a testament to human ingenuity and innovation in materials science and engineering. Their versatility, ranging from lightweight construction to exceptional corrosion resistance, has made them indispensable across a multitude of industries. The precise composition of aluminum alloys, carefully tailored to meet specific requirements, showcases the remarkable breadth of their applications.
Understanding the properties, advantages, disadvantages, and future trends of aluminum alloys equips individuals and industries with the knowledge needed to make informed decisions about material selection. As we continue to push the boundaries of technology and sustainability, aluminum alloys will remain at the forefront of material choices, enabling us to build a more efficient, sustainable, and interconnected world.