Yield strength is the stress level at which a material begins to deform plastically or permanently. In other words, it is the maximum amount of stress that a material can withstand before it starts to deform permanently. Yield strength is an important characteristic of a material because it determines the maximum load it can handle before it fails. It is an important material property that is widely used for designing any component.
The Yield Strength of a material is typically determined by performing a tensile test on a sample of the material, which involves stretching it until it deforms permanently. Yield strength is expressed in units of stress, such as pounds per square inch (psi) or pascals (Pa). The yield strength of a material is a critical parameter in the design and engineering of structures and components that are subject to stress or load, such as bridges, aircraft, and automobiles. In general, the yield strength of a material is denoted by the symbol σy
Refer to Fig. 1 which shows the stress-strain curve of a material. Point Y of the curve denotes the Yield Strength of the material.
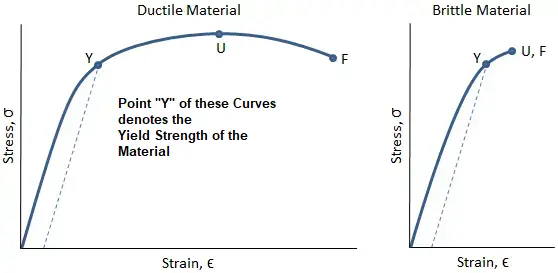
Significance of Yield Strength
The yield strength of a material is significant because it is an indication of the material’s ability to withstand deformation without breaking or failing. It is a crucial factor in determining the mechanical properties of a material and plays a key role in designing structures and components that are expected to withstand high levels of stress or load. Some of the reasons why yield strength is so significant are:
Design considerations: Engineers and designers use yield strength as a basis for designing structures and components. It helps them determine the maximum load that a material can handle before it deforms permanently. This information is crucial for ensuring the safety and reliability of the structure or component.
Material selection: Yield strength is an important factor when selecting a material for a particular application. Materials with higher yield strengths are generally preferred for applications where high loads or stresses are expected.
Safety: Knowing the yield strength of a material is critical for ensuring the safety of structures and components that are subjected to high loads or stresses. If a material is not strong enough to handle the expected loads, it can deform, buckle, or fail, potentially leading to catastrophic consequences.
Manufacturing: Yield strength also plays a role in manufacturing processes. Knowing the yield strength of a material can help manufacturers determine the best way to form, shape, or process the material without causing it to deform or fail.
Overall, yield strength is a critical parameter that helps engineers and designers ensure the safety and reliability of structures and components subjected to high loads or stresses.
Factors affecting Yield Strength
The yield strength of a material can be affected by a variety of factors, including:
Composition: The chemical composition of the material can affect its yield strength. For example, adding alloying elements to a metal can increase its yield strength by forming solid solutions, precipitates, or other strengthening mechanisms.
Microstructure: The microstructure of the material, including its grain size, shape, and distribution, can affect its yield strength. Materials with smaller grains and a more uniform distribution tend to have higher yield strengths.
Temperature: The yield strength of a material can also be affected by temperature. In general, materials become stronger at lower temperatures, but they can also become more brittle, which can affect their ability to withstand deformation.
Strain rate: The rate at which a material is deformed can also affect its yield strength. Higher strain rates can lead to a higher yield strength because they do not allow dislocations to move as easily.
Heat treatment: Heat treatment can be used to alter the yield strength of a material. Processes such as annealing or quenching can increase or decrease the yield strength depending on the specific treatment.
Surface defects: The presence of surface defects such as cracks or scratches can significantly reduce the yield strength of a material.
Understanding the factors that affect yield strength is important for engineers and designers when selecting and designing materials for specific applications.
Measuring the Yield Strength of a Material
The yield strength of a material can be measured through various mechanical testing methods. The most common method is the tensile test, which involves applying a gradually increasing load to a test specimen until it reaches the yield point.
The steps involved in measuring the yield strength of a material through the tensile test are:
- Sample preparation: A sample of the material is machined or cut to a specific shape and size according to the testing standard.
- Mounting: The specimen is mounted onto the testing machine, usually with special grips to ensure proper alignment.
- Preload: A small amount of force is applied to the specimen to remove any initial slack or looseness.
- Tensile loading: A gradually increasing load is applied to the specimen until it reaches the yield point. During this process, the machine measures the load and elongation of the specimen.
- Yield determination: Once the load and elongation data are collected, the yield point can be determined through various methods, including the 0.2% offset method or the intersection of the stress-strain curve with a line parallel to the elastic region.
- Yield strength calculation: The yield strength is calculated as the stress at the yield point, which is the load at the yield point divided by the original cross-sectional area of the specimen.
Other methods for measuring the yield strength of a material include the compression test and the torsion test, which are similar to the tensile test but apply different types of loads to the specimen. The choice of testing method depends on the material being tested and the specific application.
Yield Strength of Steel
The yield strength of the most widely used engineering material steel is provided in the Table below:
Steel Material | Tensile Strength (MPa) | Yield Strength (MPa) | Tensile Strength (ksi) | Yield Strength (ksi) |
Structural Steel, ASTM A36 | 400-550 | 250 | 58-80 | 36 |
Mild Steel, 1090 | 841 | 247 | 122 | 36 |
Maraging Steel, 2800 | 2693 | 2617 | 391 | 380 |
Chromium Vanadium Steel | 940 | 620 | 136 | 90 |
API 5L X65 | 531 | 448 | 77 | 65 |
ASTM A514 | 760 | 690 | 110 | 100 |
Chromium-Nickel Austenitic Stainless Steel | 520-720 | 210 | 75-104 | 30 |
Molybdenum Chromium Nickel Austenitic Stainless Steel | 520-670 | 220 | 75-97 | 32 |
Duplex Steels | 640-850 | 460 | 93-123 | 67 |
Stainless Steel AISI 302 | 860 | 502 | 125 | 73 |
Ferritic Stainless Steel | 500 | 280 | 73 | 41 |
Martensitic Stainless Steel | 650 | 350 | 94 | 51 |
Precipitation Hardening Stainless Steel | 1100 | 1000 | 160 | 145 |
Ordinary Carbon Steel | 315-610 | 195-275 | 46-88 | 28-40 |
Tool Steel-Annealed | 280-700 | 180-360 | 41-102 | 26-52 |
Tool Steel-Normalised | 530-760 | 380-430 | 77-110 | 55-62 |
Tool Steel-Cold Hardened | 750-1200 | – | 109-174 | – |
Alloy Structural Steel | 500-750 | – | 73-109 | – |
API 5L X42 | 414 | 290 | 60 | 42 |
API 5L X52 | 455 | 359 | 66 | 52 |
API 5L X60 | 517 | 414 | 75 | 60 |
A106 B | 414 | 241 | 60 | 35 |
API 5L B | 414 | 241 | 60 | 35 |
A333-6 | 414 | 241 | 60 | 35 |
A516-70 | 483 | 262 | 70 | 38 |
The yield strength of some of the most common materials is listed below:
Material | Tensile Strength (MPa) | Yield Strength (MPa) |
Diamond | 2800 | 1600 |
Bamboo | 265 | 142 |
Brass | 250 | |
Cast Iron, ASTM A48 | 200 | 130 |
Copper | 220 | 70 |
HDPE | 37 | 26-33 |
Marble | 15 | |
Rubber | 15 | |
Tungsten | 1510 | |
Aluminum | 40-50 | 15-20 |
Gold | 100 | |
Iron | 350 | 80-100 |
Lead | 12 | |
Nickel | 140-195 | 14-35 |
Silver | 170 | |
ABS plastics | 40 | |
A53 Seamless and Welded Standard Steel Pipe – Grade A | 331 | 207 |
A53 Seamless and Welded Standard Steel Pipe – Grade B | 414 | 241 |
A106 Seamless Carbon Steel Pipe – Grade A | 400 | 248 |
A106 Seamless Carbon Steel Pipe – Grade C | 483 | 276 |
A252 Piling Steel Pipe – Grade 1 | 345 | 207 |
A252 Piling Steel Pipe – Grade 2 | 414 | 241 |
A252 Piling Steel Pipe – Grade 3 | 455 | 310 |
A501 Hot Formed Carbon Steel Structural Tubing – Grade A | 400 | 248 |
A501 Hot Formed Carbon Steel Structural Tubing – Grade B | 483 | 345 |
A523 Cable Circuit Steel Piping – Grade A | 331 | 207 |
A523 Cable Circuit Steel Piping – Grade B | 414 | 241 |
A618 Hot-Formed High-Strength Low-Alloy Structural Tubing – Grade Ia & Ib | 483 | 345 |
A618 Hot-Formed High-Strength Low-Alloy Structural Tubing – Grade II | 414 | 345 |
A618 Hot-Formed High-Strength Low-Alloy Structural Tubing – Grade III | 448 | 345 |
API 5L Line Pipe | 310 – 1145 | 175 – 1048 |
Acetals | 65 | |
Acrylic | 70 | |
Aluminum | 110 | 95 |
Boron | 3100 | |
Brass | 250 | |
Cast Iron 4.5% C, ASTM A-48 | 170 | |
Cellulose, cotton, wood pulp, and regenerated | 80 – 240 | |
Cellulose acetate, sheet | 30 – 52 | |
Cellulose nitrate, celluloid | 50 | |
Chlorinated polyether | 39 | |
Concrete, High Strength (compression) | 40 | |
Copper | 220 | 70 |
Douglas fir Wood | 50 | |
Epoxy resins | 26 – 85 | |
Marble | 15 | |
Nylon-6 | 45 – 90 | 45 |
Nylon-66 | 60 – 80 | |
Phenolic cast resins | 33 – 59 | |
Phenol-formaldehyde molding compounds | 45 – 52 | |
Pine Wood (along the grain) | 40 | |
Polyacrylonitrile, fibers | 200 | |
Polycarbonates | 52 – 62 | |
Polyethylene HDPE (high density) | 15 | |
Polyethylene Terephthalate, PET | 55 | |
Polyamide | 85 | |
Polyisoprene, hard rubber | 39 | |
Polyimide aromatics | 68 | |
Polypropylene, PP | 28 – 36 | |
Polystyrene, PS | 30 – 100 | |
Polyurethane cast liquid | Oct-20 | |
Polyurethane elastomer | 29 – 55 | |
Silicon Carbide | 3440 | |
Steel, High Strength Alloy ASTM A-514 | 760 | 690 |
Steel, stainless AISI 302 | 860 | 502 |
Steel, Structural ASTM-A36 | 400 | 250 |
Titanium Alloy | 900 | 730 |
Difference between Yield Strength and Tensile Strength
Yield strength and tensile strength are two important mechanical properties of materials. Here are the main differences between them:
Definition: Yield strength is the stress at which a material begins to deform plastically and no longer returns to its original shape when the load is removed. Tensile strength is the maximum stress a material can withstand before it breaks or fractures.
Magnitude: In general, the tensile strength of a material is higher than its yield strength. This is because the tensile strength is the maximum stress the material can withstand before failure, while the yield strength is the stress at which the material begins to deform plastically.
Importance: Yield strength is more important than tensile strength for many engineering applications. This is because materials are often designed to operate within their elastic range, where they can be subjected to stresses up to their yield strength without undergoing permanent deformation. Tensile strength is important for materials that need to withstand high loads without breaking, such as structural components.
Testing: Yield strength is determined through mechanical testing methods such as the tensile test, while tensile strength is determined by applying a load to a material until it fractures.
In summary, yield strength is the stress at which a material begins to deform plastically, while tensile strength is the maximum stress a material can withstand before breaking. While tensile strength is important for materials that need to withstand high loads without breaking, yield strength is more important for many engineering applications, as materials are often designed to operate within their elastic range.