Gas sealants play a crucial role in various industries, ensuring the integrity and safety of systems that handle gases and liquids. Whether it’s in automotive, manufacturing, aerospace, or even household applications, gas sealants provide an effective solution to prevent leaks, maintain pressure, and enhance overall efficiency. In this blog post, we will delve into the world of gas sealants, understanding their composition, benefits, applications, and some key considerations.
What is a Gas Sealant?
Gas sealants are specialized materials designed to create a reliable barrier against escaping gases and liquids from sealed systems. They are typically used in joints, connections, and interfaces to prevent leakage, minimize waste, and maintain the desired pressure levels. Gas sealants are formulated to provide a secure seal even under extreme conditions, such as high temperatures, pressures, and chemical exposure.
In layman’s language, Gas sealant can be defined as a substance that is used to prevent the escape of gases from a particular area. It is typically used in applications where there is a risk of leaks, such as in the automotive industry, the construction industry, and the food and beverage industry.
Composition of Gas Sealants
Gas sealants are formulated from a variety of materials, each chosen based on its compatibility with specific gases, liquids, and environmental conditions. The composition can include polymers, elastomers, resins, fillers, and curing agents. Common types of gas sealants include:
- Anaerobic Sealants: These are used for threaded connections and cure in the absence of air. They are often used in applications where metal-to-metal contact is prevalent, such as pipe fittings and hydraulic systems.
- RTV (Room-Temperature Vulcanizing) Sealants: These silicone-based sealants cure at room temperature and are ideal for applications where flexibility and resistance to vibration and temperature fluctuations are crucial.
- PTFE (Polytetrafluoroethylene) Sealants: PTFE sealants are known for their excellent chemical resistance and low coefficient of friction. They are used in applications involving aggressive chemicals, extreme temperatures, and high pressures.
- Gasket Sealants: These are used to create custom gaskets in irregular or non-standard shapes. They are applied as a liquid and cure to form a flexible, resilient seal.
- Thread Sealants: These are used to seal threaded connections and prevent leakage. They provide a secure seal and also act as lubricants during assembly.
- Silicone sealants: Silicone sealants are flexible and durable, making them a good choice for applications where there is a lot of movement. They are also resistant to chemicals and weather.
- Rubber sealants: Rubber sealants are also flexible and durable, but they are not as resistant to chemicals as silicone sealants. They are a good choice for applications where there is a risk of moisture exposure.
- Epoxy sealants: Epoxy sealants are hard and durable, making them a good choice for applications where there is a risk of high temperatures or pressure. They are also resistant to chemicals.
- Urethane sealants: Urethane sealants are a combination of rubber and epoxy, giving them the best properties of both materials. They are flexible, durable, and resistant to chemicals.
Benefits of Gas Sealants
Gas sealants offer several advantages across various industries and applications:
- Leak Prevention: The primary function of gas sealants is to prevent leaks, which is crucial for maintaining operational efficiency and safety.
- Pressure Maintenance: Gas sealants help maintain the desired pressure levels within systems, ensuring optimal performance.
- Chemical Resistance: Different sealants are designed to withstand exposure to various chemicals and aggressive substances, ensuring longevity in challenging environments.
- Temperature and Pressure Resistance: Many gas sealants can withstand high temperatures and pressures, making them suitable for demanding applications.
- Vibration Damping: Gas sealants can absorb vibrations, reducing stress on joints and connections and extending the lifespan of components.
- Ease of Application: Gas sealants are available in various forms, such as liquids, pastes, tapes, and films, making them easy to apply to different surfaces and configurations.
How to Choose a Gas Sealant
The best way to choose a gas sealant is to consider the specific application. Factors to consider include the type of gas that needs to be sealed, the temperature and pressure conditions, and the level of exposure to chemicals.
It is also important to choose a sealant that is compatible with the materials that are being sealed. For example, silicone sealant should not be used to seal rubber because it can cause the rubber to deteriorate.
Applications of Gas Sealants
Gas sealants find applications across diverse industries:
- Automotive: Gas sealants are used in engines, transmissions, and exhaust systems to prevent leakage and maintain optimal performance.
- Manufacturing: They are essential in industries involving hydraulic systems, pneumatics, and various fluid-handling equipment.
- Aerospace: Gas sealants are used in aircraft engines, fuel systems, and hydraulic systems, where reliability and safety are paramount.
- Plumbing: Thread sealants are commonly used in plumbing applications to prevent leaks in threaded connections.
- Electronics: Sealants are used in electronic devices to provide environmental protection and improve the reliability of components.
- Construction: Gas sealants are used in HVAC systems, pipelines, and joints to ensure energy efficiency and prevent gas leaks.
How to Apply Gas Sealant
The instructions for applying a gas sealant will vary depending on the specific product. However, there are some general steps that are common to most applications.
- Clean and dry the surface that is being sealed.
- Apply the sealant according to the manufacturer’s instructions.
- Allow the sealant to cure according to the manufacturer’s instructions.
Safety Precautions during applying gas sealant
When working with gas sealants, it is important to take precautions to protect yourself from fumes and chemicals. These precautions may include:
- Wearing gloves, goggles, and a respirator.
- Working in a well-ventilated area.
- Avoiding contact with the skin and eyes.
- Dispose of the sealant properly.
Considerations and Best Practices
When selecting and using gas sealants, there are several considerations to keep in mind:
- Compatibility: Choose a sealant that is compatible with the materials and substances it will come into contact with.
- Temperature and Pressure Ratings: Ensure that the chosen sealant can withstand the temperature and pressure conditions of the application.
- Curing Time: Consider the curing time of the sealant, as some applications require rapid curing, while others allow for longer curing times.
- Application Technique: Follow manufacturer guidelines for application techniques, including surface preparation, curing methods, and recommended tools.
- Safety: Some sealants may emit fumes during curing. Ensure proper ventilation and adhere to safety precautions.
Notable Gas Sealant Brands
Several reputable gas sealant brands are available on the market, each offering a range of products designed to cater to various industries and applications. Here are some popular gas sealant brands that are known for their quality and effectiveness:
Loctite Gas Sealant:
Loctite is a well-known brand in the adhesive and sealant industry. They offer a variety of gas sealants, including anaerobic sealants for threaded connections, flange sealants, and gasket sealants. Loctite sealants are widely used in automotive, manufacturing, aerospace, and industrial applications.
Permatex Gas Sealant:
As mentioned in the previous sections, Permatex is a trusted brand known for its diverse range of gas sealants. Their products are widely used in automotive maintenance, manufacturing, construction, and other industries.
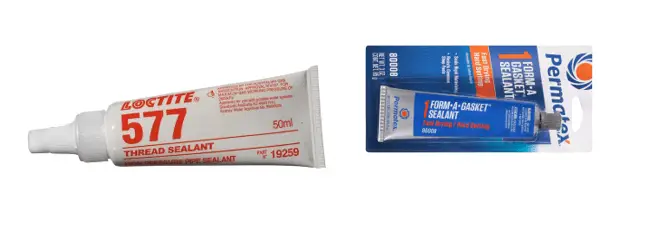
3M gas Sealant:
3M is a renowned global company known for its innovative products. Their line of gas sealants includes thread sealants, gasket sealants, and sealant tapes. 3M sealants find applications in automotive, aerospace, electronics, and various industrial sectors.
Henkel (formerly known as Hylomar):
Henkel offers a range of sealants and adhesives under the brand Hylomar. Their products are particularly well-regarded for their use in aviation, automotive, and industrial applications.
Teflon (by Chemours):
Chemours, the company behind Teflon, offers a range of PTFE-based sealants known for their excellent chemical resistance and high-temperature stability. Teflon sealants are often used in applications where aggressive chemicals or extreme temperatures are a concern.
Meguiar’s (for Automotive):
While primarily known for its car care products, Meguiar’s also offers gas sealants that are specifically formulated for automotive applications, such as sealing threaded connections and preventing leaks in engine components.
CRC Industries:
CRC Industries produces a variety of maintenance and repair products, including gas sealants. Their products are widely used in automotive, industrial, and electrical applications.
RectorSeal:
RectorSeal offers a range of specialty sealants and adhesives, including gas sealants for plumbing, HVAC, and industrial applications.
Fernox (for Plumbing and HVAC):
Fernox is known for its solutions in the plumbing and HVAC sectors. They offer gas sealants for sealing pipe threads and connections, particularly in water and heating systems.
Parker Hannifin:
Parker Hannifin produces a wide range of sealing solutions, including gas sealants and gaskets, for various industries like automotive, aerospace, and industrial manufacturing.
What is Gas Sealant Paste?
Gas sealant paste, often referred to simply as sealant paste, is a specialized compound formulated to create a reliable seal between mating surfaces, preventing the escape of gases and fluids. It is designed to be applied in paste form, which makes it easy to spread and conform to irregular surfaces, ensuring an effective barrier against leaks. Gas sealant paste is widely used in industries where sealing joints, connections, and interfaces is critical to maintaining operational efficiency and safety.
Gas sealant paste is typically composed of a blend of materials that impart adhesive, sealing, and resistance properties. The exact composition may vary depending on the specific brand and type of paste, but common components include:
- Fillers
- Binders
- Modifiers
- Curing Agents
There are mainly three types of gas sealant pase that are widely popular in industries. They are:
- Anaerobic Sealant Paste: Used for threaded connections, these pastes cure in the absence of air and are often used in industrial and automotive settings.
- Flange Sealant Paste: Designed for flange connections, these pastes provide a reliable barrier against leaks in equipment like pumps and valves.
- Gasket Sealant Paste: Used to create custom gaskets, these pastes are applied to surfaces before assembly to form a flexible and effective seal.
To conclude, Gas sealants are indispensable in maintaining the integrity and performance of systems that handle gases and liquids. With their ability to prevent leaks, withstand challenging conditions, and enhance efficiency, they find applications in a wide range of industries. Choosing the right type of sealant, considering compatibility, temperature, pressure, and application techniques, is essential for ensuring the success of any sealing project. By understanding the composition, benefits, applications, and considerations of gas sealants, industries can make informed decisions to improve reliability, safety, and overall performance.