Caesar II is a computer software program primarily used in the field of piping stress analysis for the design and evaluation of piping systems within various industries, including oil and gas, petrochemical, chemical, power generation, and more. Developed by Hexagon PPM (formerly known as COADE, Inc.), Caesar II has been a staple tool in the engineering and construction sectors for decades. In this comprehensive guide, we will explore Caesar II software in great detail, covering its history, features, applications, analysis methodologies, and much more to equip you with a thorough understanding of this software.
1. Introduction to Caesar II
1.1 History:
Caesar II was initially developed in the late 1980s by COADE, Inc., a Texas-based engineering software company. Over the years, it has evolved into a comprehensive and widely used tool for piping stress analysis. In 2005, COADE was acquired by Hexagon AB, a global provider of information technology solutions. The software has since been developed and enhanced under the Hexagon PPM brand.
1.2 Purpose and Scope:
Caesar II is designed to address the critical engineering task of analyzing the stresses and deformations in piping systems. These systems are essential components in various industries, carrying fluids and gases under different operating conditions. Ensuring the integrity and safety of these systems is paramount, and Caesar II plays a pivotal role in achieving this.
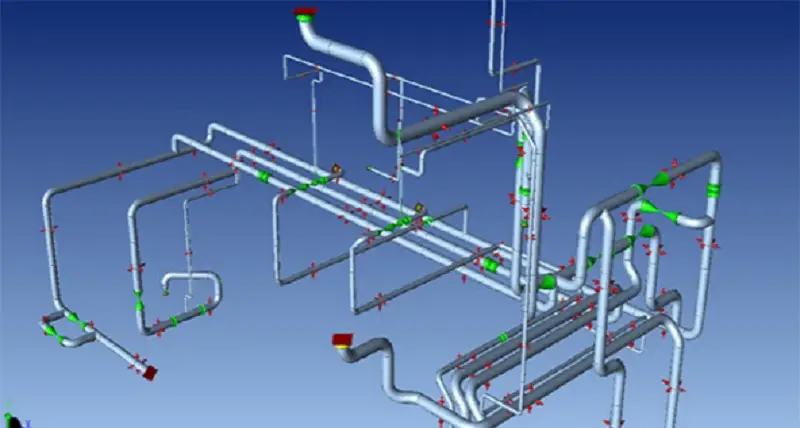
1.3 Key Features:
Caesar II is renowned for its robust feature set, which includes:
- Modeling Tools: The software provides tools for creating a detailed 3D model of the piping system, including components such as pipes, fittings, valves, and supports.
- Analysis Capabilities: Caesar II performs both static and dynamic analyses, assessing factors such as thermal expansion, pressure, and seismic forces.
- Load Cases: Users can define multiple load cases, considering various operating conditions and scenarios.
- Code Compliance: The software ensures that designs adhere to industry standards and codes, such as ASME B31.1, ASME B31.3, and many others.
- Intuitive Interface: Caesar II features a user-friendly graphical interface that simplifies the modeling and analysis process.
- Extensive Material Database: It offers a comprehensive library of materials commonly used in piping systems.
- Reporting and Documentation: The software generates detailed reports and documentation for design validation and regulatory compliance.
1.4 User Interface:
Caesar II’s user interface is designed with engineers in mind, providing a visually intuitive workspace. The software uses a Windows-based graphical interface, making it accessible to users with varying levels of expertise. Key components of the interface include the piping model view, analysis input dialogues, and result visualization windows.
2. Piping Stress Analysis Fundamentals
2.1 What is Piping Stress Analysis?
Piping stress analysis is the engineering discipline that assesses the behavior of a piping system under various loads and operating conditions. It ensures that the system can withstand stresses, strains, and deformations while maintaining its structural integrity and safety.
2.2 Importance of Stress Analysis:
Stress analysis is crucial for several reasons:
- Safety: Ensures that the piping system can operate safely without failure.
- Efficiency: Optimizes the design for material usage and minimizes costs.
- Compliance: Ensures that designs conform to industry standards and codes.
- Reliability: Predicts potential problems before they become costly issues.
- Legal Requirements: Compliance with regulatory authorities and safety standards.
2.3 Codes and Standards:
Various industry codes and standards govern piping design and analysis, and Caesar II supports compliance with many of them. Some prominent standards include:
- ASME B31 Series: American Society of Mechanical Engineers codes for pressure piping covering various industries.
- API Codes: American Petroleum Institute standards for the oil and gas industry.
- ISO Standards: International Organization for Standardization codes for international applications.
- EN Codes: European Norm codes for European applications.
- Other Regional Codes: Depending on the project location, other regional codes may apply.
2.4 Load Types:
Piping systems are subjected to several types of loads, including:
- Thermal Expansion: Due to temperature changes.
- Pressure: Resulting from fluid or gas flow.
- Weight: From the piping itself and its contents.
- Seismic and Wind Forces: External forces from environmental conditions.
- Vibration: Oscillatory forces that can lead to fatigue failure.
- Dynamic Loads: Resulting from rapid changes in operating conditions.
2.5 Analysis Types:
Piping stress analysis can be categorized into different types, such as:
- Static Analysis: Analyzes stresses and displacements under steady-state conditions.
- Dynamic Analysis: Considers time-dependent loads and transient conditions.
- Modal Analysis: Determines natural frequencies and mode shapes.
- Response Spectrum Analysis: Evaluates response to seismic forces.
- Time History Analysis: Simulates transient conditions over time.
3. Caesar II Workflow
3.1 Piping System Modeling:
The first step in using Caesar II is creating a detailed 3D model of the piping system. This includes defining the geometry, components, and material properties of the pipes. Users can import piping layouts from CAD software or create them from scratch within Caesar II.
3.2 Boundary Conditions:
Setting up boundary conditions is critical. This involves defining restraints and supports at fixed points in the model, specifying where the piping is anchored, and how it is constrained from moving. Boundary conditions help simulate real-world conditions accurately.
3.3 Load Cases:
Users define load cases to represent different operating scenarios, including variations in temperature, pressure, and external forces. Load cases encompass all the conditions under which the piping system must be analyzed.
3.4 Analysis Options:
Caesar II offers various analysis options, including the type of analysis (static, dynamic, etc.), the method of solving (e.g., finite element analysis), and considerations for nonlinear behavior.
3.5 Analysis Run:
Once the model is prepared, and load cases and analysis options are defined, users initiate the analysis run. Caesar II solves the equations governing the behavior of the piping system and calculates stresses, displacements, and other relevant parameters.
3.6 Reviewing and Interpreting Results:
After the analysis run, users can review the results in Caesar II’s graphical interface. The software provides visualizations, plots, and reports to help engineers interpret the data and make informed design decisions.
4. Modeling in Caesar II
4.1 Geometry Definition:
Modeling begins with defining the geometry of the piping system. Users create the layout of pipes, fittings, flanges, valves, and other components. Accurate geometry is essential for realistic stress analysis.
4.2 Pipe Components:
Caesar II includes a library of standard pipe components, including elbows, tees, reducers, and more. Users can select and place these components in the model, specifying their dimensions and properties.
4.3 Material Properties:
Material properties, such as Young’s Modulus, Poisson’s Ratio, and thermal expansion coefficients, must be assigned to each component. Caesar II provides an extensive material database, and users can add custom materials when necessary.
4.4 Restraints and Supports:
Defining restraints and supports is crucial for accurate analysis. Engineers specify how the piping is anchored and constrained, taking into account the real-world conditions at the installation site.
4.5 Operating Conditions:
Load cases include temperature, pressure, and other operating conditions. These factors are input into Caesar II to simulate the effects of various scenarios on the piping system.
4.6 Loadings and Forces:
External forces and loads, such as wind, seismic activity, and dynamic forces, are applied to the model to simulate real-world conditions. Users define these loads as part of the analysis setup.
5. Analysis Types in Caesar II
5.1 Static Analysis:
Static analysis is the most common type and is used to assess stresses and displacements in a piping system under steady-state conditions. It considers factors like thermal expansion, pressure, and weight. Engineers often perform multiple load cases to account for different operating conditions.
5.2 Dynamic Analysis:
Dynamic analysis is essential for systems subjected to rapid changes in operating conditions or transient events. It assesses the response of the piping system to time-dependent forces, such as water hammer or relief valve discharge. Caesar II’s dynamic analysis capabilities are particularly valuable in industries like power generation and chemical processing.
5.3 Modal Analysis:
Modal analysis determines the natural frequencies and mode shapes of the piping system. Identifying these modes helps engineers avoid resonance and structural failures caused by excessive vibrations. This analysis type is crucial for systems sensitive to dynamic forces.
5.4 Response Spectrum Analysis:
Response spectrum analysis is used to evaluate the response of the piping system to seismic forces. Engineers input a seismic response spectrum, which represents ground motion, and Caesar II calculates the system’s response to these forces. This is crucial in earthquake-prone regions.
5.5 Time History Analysis:
Time history analysis simulates transient conditions over time. It is commonly used in situations where the loadings vary rapidly, such as during startup or shutdown of a process plant. Caesar II can simulate how the piping system responds to these changing conditions.
6. Interpreting Caesar II Results
6.1 Stress Analysis Results:
Caesar II provides detailed stress analysis results, including axial stress, hoop stress, and shear stress. Engineers review these results to ensure that stresses remain within allowable limits defined by industry codes and standards.
6.2 Displacement Analysis Results:
Displacement analysis results indicate how much the piping system deforms under various loads. Excessive displacement can lead to misalignment and structural issues. Caesar II helps engineers identify areas of concern and make design adjustments.
6.3 Nozzle Analysis:
Nozzle analysis is a critical aspect of piping stress analysis, especially for equipment connections like pumps and vessels. Caesar II assesses the loads on nozzles and provides calculations for their reinforcement if needed.
6.4 Wind and Seismic Analysis:
For systems in regions prone to high winds or seismic activity, Caesar II evaluates the effects of these forces. Engineers can assess how the piping system responds to wind-induced vibrations or seismic events and make design improvements accordingly.
6.5 Fatigue Analysis:
Fatigue analysis is vital for systems subjected to cyclic loading. Caesar II calculates fatigue life and helps engineers predict when and where fatigue failure might occur. This is essential for ensuring the long-term reliability of the piping system.
6.6 Report Generation:
Caesar II generates detailed reports that document the analysis process, results, and compliance with relevant codes and standards. These reports are essential for regulatory approval and project documentation.
7. Caesar II and Industry Standards
7.1 ASME B31 Series:
The ASME B31 series of codes, published by the American Society of Mechanical Engineers, cover various aspects of piping design, including pressure piping, power piping, and process piping. Caesar II provides tools to ensure compliance with these codes, such as ASME B31.1 for power piping and ASME B31.3 for process piping.
7.2 API Codes:
For the oil and gas industry, compliance with API codes is crucial. Caesar II supports API standards like API 610 for centrifugal pumps, API 650 for storage tanks, and API 661 for air-cooled heat exchangers, among others.
7.3 ISO Standards:
In international projects, adherence to ISO standards is essential. Caesar II can be used to design and analyze piping systems according to ISO standards, ensuring global compatibility.
7.4 Other Relevant Codes:
Depending on the industry and location, other codes and standards may apply. Caesar II’s flexibility allows engineers to work within the framework of regional and industry-specific codes.
8. Advanced Features and Modules
8.1 Caesar II Static Equipment:
In addition to piping, Caesar II offers specialized modules for analyzing static equipment such as pressure vessels and heat exchangers. These modules enable engineers to assess the integrity and compliance of these critical components.
8.2 Caesar II Offshore:
For offshore applications, Caesar II includes features to address the unique challenges of subsea pipelines and platforms. It considers factors like wave loading, buoyancy, and seabed interactions.
8.3 Caesar II Dynamics:
The dynamic analysis capabilities of Caesar II are enhanced in specialized modules. These modules can handle complex transient events and dynamic loads, making the software suitable for a wide range of applications.
8.4 Caesar II FEATools:
FEATools is an add-on module for Caesar II that extends its capabilities to perform finite element analysis (FEA). FEA allows for more detailed and accurate stress simulations of complex geometries and loadings.
8.5 Other Caesar II Modules:
Caesar II offers several other modules and add-ons, including those for heat exchanger analysis, expansion joint analysis, and nozzle flexibility analysis. These modules enhance the software’s versatility and utility in various industries.
9. Integration with Other Software
9.1 CAD Integration:
Caesar II is often integrated with computer-aided design (CAD) software such as AutoCAD or Bentley MicroStation. This integration allows for seamless import and export of piping geometry, streamlining the modeling process.
9.2 CAE Integration:
In addition to CAD, Caesar II can be integrated with computer-aided engineering (CAE) software for more advanced simulations. This integration enables engineers to leverage the strengths of both Caesar II and CAE tools for complex analyses.
9.3 Plant Design Systems Integration:
Caesar II can be integrated into overall plant design and engineering systems, facilitating collaboration between piping designers, stress analysts, and other engineering disciplines. This integration ensures that the piping system is part of a cohesive plant design.
10. Common Challenges and Troubleshooting
10.1 Convergence Issues:
Convergence refers to the process by which the analysis solution reaches a stable result. Engineers may encounter convergence issues if the model is poorly defined or if the analysis parameters are not set correctly. Troubleshooting convergence problems is essential for obtaining reliable results.
10.2 Model Errors:
Errors in the piping model, such as incorrect geometry or improperly defined boundary conditions, can lead to inaccurate results. Engineers need to carefully review and validate their models to avoid these errors.
10.3 Interpretation Challenges:
Interpreting analysis results and understanding their implications can be challenging, especially for complex systems. Engineers must have a deep understanding of piping mechanics and the specific requirements of the industry codes being used.
10.4 Optimization Strategies:
Optimizing a piping system for efficiency and safety requires experience and engineering judgment. Engineers often need to iterate on the design to achieve the best balance between cost, performance, and compliance.
11. Caesar II Best Practices
11.1 Model Setup:
- Start with accurate geometry and material properties.
- Ensure that boundary conditions are realistic and representative of the installation site.
- Consider all potential load cases and load combinations.
11.2 Load Cases and Load Combinations:
- Carefully define load cases to encompass all operating scenarios.
- Combine load cases to assess the most critical conditions.
- Use industry-specific load combinations as per relevant codes.
11.3 Material Selection:
- Choose materials that meet code requirements and are suitable for the intended service.
- Verify material properties and stress-strain curves for accuracy.
11.4 Results Verification:
- Cross-check analysis results with hand calculations to validate the model.
- Use engineering judgment to assess the significance of stresses and displacements.
11.5 Documentation and Reporting:
- Maintain detailed records of the analysis process and assumptions.
- Generate comprehensive reports that document compliance with codes and standards.
12. Applications of Caesar II
12.1 Oil and Gas Industry:
Caesar II is widely used in the oil and gas sector for designing and analyzing pipelines, offshore platforms, refineries, and petrochemical plants. It ensures the safe transport of hydrocarbons and compliance with industry regulations.
12.2 Petrochemical Industry:
In the petrochemical industry, Caesar II is instrumental in designing complex piping networks that transport a variety of chemicals. It ensures the integrity of these systems and helps prevent leaks and accidents.
12.3 Power Generation:
Power plants, including nuclear, coal, gas, and renewable energy facilities, rely on Caesar II for designing and analyzing the intricate piping systems that transport steam, water, and other fluids critical to power generation.
12.4 Chemical Industry:
Chemical processing plants use Caesar II to design piping systems for the production and transport of chemicals. The software helps prevent corrosion, leaks, and other issues that could compromise safety and product quality.
12.5 Other Industrial Sectors:
Caesar II finds applications in various industrial sectors, including water and wastewater treatment, pharmaceuticals, food and beverage, and more. Any industry that relies on complex piping systems can benefit from Caesar II’s capabilities.
13. Future Trends and Developments
13.1 Industry 4.0 and Digital Twins:
The integration of Caesar II with digital twin technology is a growing trend. Digital twins create virtual replicas of physical piping systems, enabling real-time monitoring, predictive maintenance, and performance optimization.
13.2 Cloud-Based Solutions:
The adoption of cloud-based analysis tools is on the rise. Cloud platforms offer scalability, collaboration, and remote access, making it easier for engineering teams to work together on complex projects.
13.3 Artificial Intelligence and Machine Learning:
AI and ML are being explored to enhance the accuracy and speed of piping stress analysis. These technologies can help automate certain aspects of modeling and analysis.
13.4 Sustainability and Green Design:
There is a growing emphasis on designing piping systems that are environmentally friendly and energy-efficient. Caesar II may evolve to include tools for assessing the environmental impact of piping systems and optimizing them for sustainability.
14. Conclusion
14.1 Significance of Caesar II:
Caesar II is an indispensable tool in the world of piping stress analysis. Its role in ensuring the safety, reliability, and compliance of piping systems across various industries cannot be overstated. As technology advances and industries evolve, Caesar II continues to adapt and meet the ever-growing demands of the engineering community.
14.2 Continuing Relevance:
Despite the emergence of newer technologies, Caesar II remains relevant due to its versatility, robust feature set, and extensive user base. As long as industries rely on complex piping systems, the need for accurate stress analysis and compliance with codes and standards will persist.
14.3 The Role of Engineers:
Caesar II is a powerful tool, but its effectiveness depends on the expertise and judgment of engineers who use it. Engineers play a crucial role in ensuring that piping systems are designed, analyzed, and maintained to the highest standards of safety and performance.
In conclusion, Caesar II is more than just software; it’s a cornerstone of modern engineering practice, contributing to the safety, efficiency, and reliability of critical infrastructure worldwide. As the engineering landscape continues to evolve, Caesar II will evolve with it, supporting engineers in their mission to create safe and efficient piping systems for generations to come.