You must be aware that the Process Piping Code ASME B31.3-2022 has been issued on 31st January 2023 and it will be applicable in projects from 1st August 2023 onwards. Similar to every new issue of ASME B31.3, this 2022 edition also provides various changes. For the first time, the ASME B31.3-2022 document clearly notifies the changes by a margin note (22), wherever a revision has taken place
In this article, I will list down some of the changes that ASME B31.3-2022 emphasizes with respect to its earlier revision ASME B31.3-2020
New Definitions:
In clause 300.2, the 2022 edition of ASME B31.3, added the following definitions which are not provided in AME B31.3-2020.
- Construction: This is an engineering activity or process that consists of fabrication, assembly, erection, inspection, examination, and testing.
- Designated lot: It is a pre-defined group of welded, brazed, fused, or bonded piping joints from which a specified percentage is randomly selected for examination.
- Combination welded (COW) pipe: These are electric-fusion welded pipes that are made using a combination of the gas metal-arc welding (GMAW) and submerged-arc welding (SAW) processes. In this type of pipe, the GMAW bead is not completely removed by the SAW passes. The pipe is made with a straight seam (COWL) or a helical (spiral) seam (COWH).
- Postweld hydrogen bakeout: It is a process of holding a completed or partially completed weld to facilitate hydrogen diffusion from the weld. Post-weld hydrogen bakeout is performed at an elevated temperature below 425° C (800° F). The post-weld hydrogen bakeout requirement has been included in clause 331.1.2 (c) of the code.
- Set pressure: Set pressure is the pressure at which a pressure relief device (PRV/PSV/Rupture Disk) begins to relieve. Typical examples are the lift pressure of a spring-actuated relief valve, the bursting pressure of a rupture disk, or the breaking pressure of a breaking pin device.
New Component Standards
The following new component standards have been added in ASME B31.3-2022.
- AWWA C228
- MSS SP-128
- MSS SP-136
- ASTM D6041
- ASTM F1970
Accidental Blast as Dynamic Impact Force
In clause 301.5.1, the effect of the accidental blast is added as a dynamic impact force which must be evaluated along with other impact forces generated due to flow rate change, slugging, hydraulic shock, and geysering. However, these effects must be specified in the engineering design.
Stress Range Factor:
Equation 1c, providing a formula for calculating the stress range factor (clause 302.3.5), f has been changed entirely in the latest ASME B31.3-2022 edition. Equation 1d for the calculation of the equivalent number of full displacement cycles is also modified. The exact 1c and 1d equations are provided below in Fig. 1 for your comparison purpose.
As explained by Mr. Don Frikken; The slope of the curve for the stress range factor (f) was changed from a slope of 5:1 to a slope of 3:1 based on the ASME Pressure Vessel and Piping paper PVP-61871 authored by Hinnant & Paulin. Their work proves that using a fatigue curve with a slope of 3:1 is more accurate than the Code’s previous fatigue curve with a slope of 5:1.
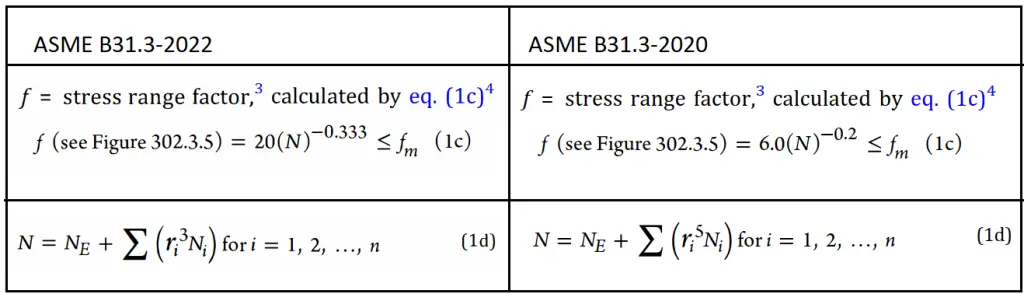
As per the above equations, if we calculate the stress range factor, f for a specific N value, we can find that the f value is lower as per the new formula mentioned in ASME B31.3-2022. So, the new code provides a stringent requirement for cyclic services as allowable displacement stress values will be less as compared to ASME B31.3-2020.
N (No of Cycles) | Stress Range Factor, f as per ASME B31.3-2022 | Stress Range Factor, f as per ASME B31.3-2020 |
9000 | 0.964422291 | 0.97118675 |
10000 | 0.931172187 | 0.950935915 |
11000 | 0.902082445 | 0.932980815 |
12000 | 0.876319833 | 0.916885281 |
13000 | 0.853270752 | 0.902324148 |
14000 | 0.832471472 | 0.889048888 |
15000 | 0.813563782 | 0.876865531 |
16000 | 0.796265761 | 0.865619944 |
17000 | 0.780351923 | 0.85518774 |
18000 | 0.76563936 | 0.845467172 |
19000 | 0.751977847 | 0.836374013 |
20000 | 0.739242636 | 0.827837797 |
21000 | 0.727329111 | 0.819799014 |
22000 | 0.716148758 | 0.812206974 |
23000 | 0.705626084 | 0.805018171 |
24000 | 0.695696234 | 0.798194998 |
25000 | 0.686303119 | 0.791704746 |
Specific Requirements for Double-Seated valves:
A new clause 307.2.3 is added in ASME B31.3-2022 to explain the requirements for double-seated valves with more than 2 inches NPS size. As per that, the designer should determine if a change in fluid phase or temperature can result in pressure between the valve seats above the pressure rating of the valve, and if that happens the valve cavity must be designed to absorb that increase in pressure or equipped with a relief system.
Impact testing of Steel Welds
In clause 323.2.2, sub-paragraph f, the requirement for impact testing of steel welds has been revised from a minimum design temperature of -18 Deg C (As per ASME B31.3-2020) to -29 Deg C in ASME B31.3-2022.
Table 323.2.2A which provides the values for minimum temperatures without impact testing for carbon steel materials are entirely revised. In table 323.3.4, the celsius temperature values for the Charpy impact test temperature reduction are rounded off to the nearest integer values.
Requirements for Fillet Welds and Fabricated Laps:
Additional welding requirements have been added for fillet and socket welds in clause 328.5.2. Similarly, enhanced requirements for fabricated laps are added in clause 328.5.5 of the latest ASME B31.3.
Requirements for Attachment Welds:
New requirements for attachment welds have been added in the 2022 edition of ASME B31.3. As per the new edition:
For temporary attachments on pressure-retaining components, the surfaces where attachments have been removed shall be finished by grinding or other acceptable means. Surfaces shall be blended smoothly into the surrounding base metal without encroaching on the minimum required thickness, tm, and examined.
Requirements for Leak Test Pressure Gages:
Clause 345.2.2, subparagraph (d) explains the requirements for test gages for the first time. ASME B31.3-2022 mentions:
- One or more pressure-indicating gages shall be connected to the piping in a manner in which they will receive full test pressure.
- Dial indicating pressure gages used in leak testing should be graduated over a range of about double the intended test pressure, but in no case shall the range be less than 1 1/2 nor more than 4 times the test pressure.
- Digital reading pressure gages having a wider range of pressure may be used, provided the readings give the same or greater degree of accuracy as obtained with dial pressure gages.
- The level of accuracy for pressure test gages should be specified in the engineering design.
- Each gage shall be calibrated against a standard dead weight tester or a calibrated master gage. The gage shall have been calibrated within 12 months prior to each test, or any time there is reason to believe the gage is in error. Calibration may exceed 12 months with the owner’s approval.
Miscellaneous
- Clause 301.7.2 of ASME B31.3-2022, further clarified the meaning and interpretation of loads due to temperature gradients by modifying the statement of the clause.
- A new clause A321.6 was added in ASME B31.3-2022 to explain supporting requirements for piping lined with non-metals. Earlier version ASME B31.3-2020 was not clearly specifying such requirements.
What’s up, the whole thing is going nicely here and ofcourse every one is sharing facts, that’s actually good, keep up writing.
I visit each day some web pages and blogs to read articles or reviews, however
this website provides feature based posts.
Excellent pieces. Keep posting such kind of info on your blog.
Im really impressed by it.
Hi there, You’ve done a fantastic job. I’ll certainly digg it and in my opinion suggest to my
friends. I am confident they will be benefited from this website.
Thanks a lot for your help.